Winding down rapid shutdown issues on C&I rooftops
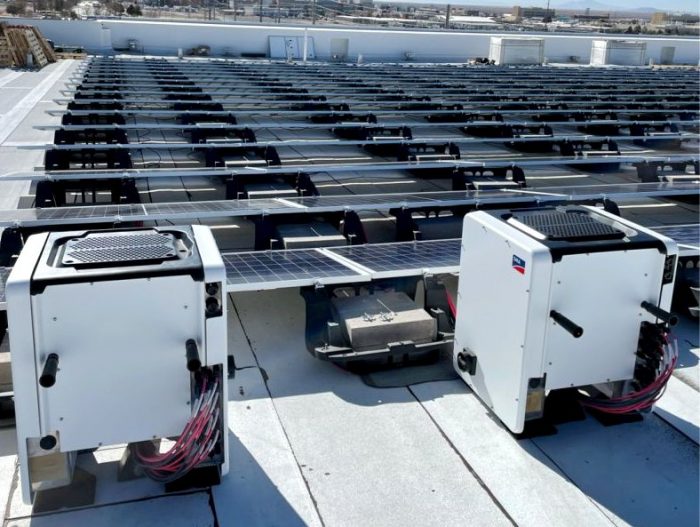
Assuring safety for first responders on solar rooftops – and how to codify it – has been an ongoing struggle for years, pitting solar installers, inverter and optimizer manufacturers, and rapid shutdown device makers against code writers.
On the technical side, two major problems with solar rapid shutdown systems (RSS) and module level power electronics (MLPE) designs are:
- Wiring crosstalk in power line communications (PLC)
- Malformed or mismatched PV connectors
Thankfully, new technology and more tailored installer services may have solved much of the crosstalk problem, while continuing connector problems may point to an opportunity for greater installer — and procurement — education on best practices.
Rapid problems
RSS problems have been all too widespread in the solar industry, according to one knowing source.
“Solar professionals are increasingly aware of the issues posed by rapid shutdown device (RSDs) requirements,” opines James Nagel, the co-founder and COO of HelioVolta, a third-party auditor of solar systems.
“While the industry still lacks comprehensive field data on RSDs and the issues they cause, by now practically everyone working in the C&I market has personally experienced the additional challenges of working with these devices.”
Another problem with RSS functionality is the mere statistical likelihood of a failure between connectors, exacerbated by installers that mismatch PV connectors, leading to hot spots.
Adjusting to the safety defense of the industry is the evolving UL 3741, written to meet the PV Hazard Control subsection of NEC 690.12(B)(2) to comply with rapid shutdown. While inverter and optimizer makers were quick to comply with the code, released in 2020, and updated in 2023, racking companies are leading the charge to certify their systems with compliant wire management techniques to enable string inverter designs without RSS that compete with MPLE-based systems.
“Fewer components mean less connections between modules, which leads to a more reliable system. It also creates less upfront cost, less installation time on the roof, and ultimately less O&M time to service individual components in the future. PV systems that rely solely on rapid shutdown devices for each module have a higher rate of failure at each connection point, making the UL 3741 compliance a more reliable and safer solution than MLPE solutions,” Bob Wszolke, a content marketing specialist at Fronius USA told SB as part of the 2023 Solar Inverter Buyer’s Guide.
While MPLE systems now seem to have the most traction on solar design tables, UL 3741 refinements are permitting, if not encouraging design alternatives.
“In our experience, UL 3741-certified products are used for new projects whenever possible because they avoid the many problems associated with RSDs/MLPEs,” Nagel suggest. “Systems that use UL 3741 products are also faster and easier to install.”
SB Editor-in-Chief recently got a crash course in UL 3741. Read that right here.
Certain rooftop projects do have design constraints that require inverter installation outside of the array boundary, and RSD compliance via MLPE is therefore mandatory, he points out.
Cancelling out crosstalk
Perhaps the most vexing problem with RSS functionality on MPLE equipment is crosstalk between wires that should otherwise not be talking to one another during power line communications. The result of crosstalk can be a rapid shutdown/restart toggling that can cause thermal hot spots in the equipment. Similarly, arc fault signals can be confused with normal RSS communications.
Among companies challenged by the problem, Tigo worked through problems with crosstalk in early 2022 and by July of that year came out with its Pure Signal RSS transmitter, which eliminated many crosstalk instances by phasing signals among wires. While wireless communications virtually eliminate crosstalk, the slightly higher cost of wireless inspires many designers and installers to choose the wired solution, which often is not monitored.
“It’s a design choice. There is no situation where you must have wireless, and there’s no situation where you must have wired. It’s a choice of the designer, the project manager, and procurement,” says James Dillon, Tigo’s Chief Marketing Officer.
“The wireless solution, frankly, avoids all of that [crosstalk],” Dillon continues. “It costs a little bit more, but you’ve got tradeoffs. We’ve tried to present the tradeoffs to installers and quite a few of them have moved to the wireless just because it doesn’t have the concerns of wired.”
As an alternative to standard wired RSS, Sol-Ark in December 2023 adopted Enteligent’s NMax Rapid Shutdown with Optimization platform for its MLPE line of products.
“Sol-Ark commissioned the 0900-80V to serve as much more than a rapid shutdown device. By combining the important safety role of an RSD with additional features around energy optimization and data monitoring, this device serves as a holistic solution for the core needs of Sol-Ark’s customers,” said Tom Brennan, CEO of the company in a statement.
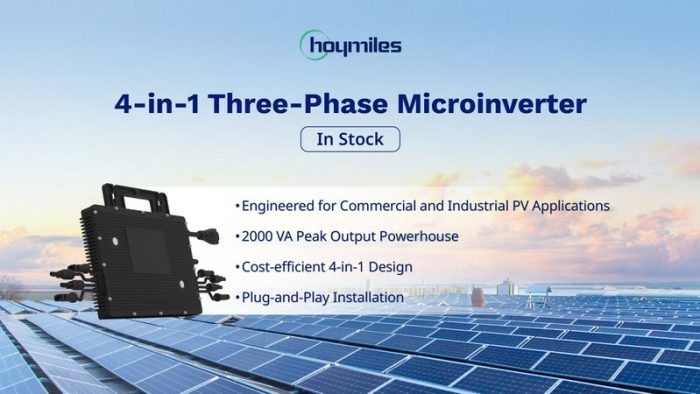
Hoymiles opted for the wireless solution for its new line of HMT three-phase microinverters introduced in April 2023. The inverters come with power options of 1600 VA, 1800 VA and 2000 VA, featuring Sub-1G wireless communication with the Data Transfer Unit communication gateway DTU, “making the data transmission more stable across a longer distance,” the company said in a statement.
Northern Electric Power (NEP) in April announced their All-In-One for High Power Modules Microinverter, adding a setting to their RSS platform for installers to perform IV Curve Trace Testing. The test sweeps the electrical load connected to the solar PV module or string and measures both the current and voltage at multiple points during the sweep.
“Based on NEP’s proprietary, PLC-based two-way data and control, this testing can enable installers and independent engineers to sign off on new installs, and the same process can be used over time to ensure site performance year to year,” the company said in a statement.
Installation service as a solution
Regardless of technology or NEC code pathway, everyone agrees quality workmanship (and a quality QA/QC process) is crucial to reducing issues with rapid shutdown.
PV connector mismatches are an all-too-common quality assurance/quality control problem, according to Nagel.
“Cross-mated connectors can introduce incompatibility between tolerances and material. Over time, the mismatch can grow to a hot spot that can only be identified with a thermal camera. Even when connectors are not cross-mated, the use of factory-made jumpers from multiple vendors introduces varying levels of quality control and makes traceability for warranty claims, in the event of a failure, incredibly difficult. This is common on large utility-scale projects utilizing pre-assembled whips and harnesses and multiple sub-contractors,” writes Nagel (see SB March 27, 2023).
“The increased use of mass-produced power electronics components over the years has statistically added more failure points to U.S. rooftop solar systems. More failures mean more thermal events,” observes Nagel.
The continuing need to educate installers on RSS design precautions led Tigo to roll out its Green Glove program in September 2023, which includes special services ranging from six-point plan checks to a Tigo representative visiting the site during commissioning and following up thereafter.
“You’ve got an EPC contractor that does the actual installation, the financier, the panel or the module maker, the inverter maker and you’ve got us; that’s a lot of companies,” Dillon says. “It’s too easy to point fingers. We’re here to solve the problem, not to fix blame on anybody. We have got to work together. That’s what is most important here: training and working together.”
Charles W. Thurston is a freelance contributor to Solar Builder.
Comments are closed here.