How lead-acid batteries remain viable in solar applications
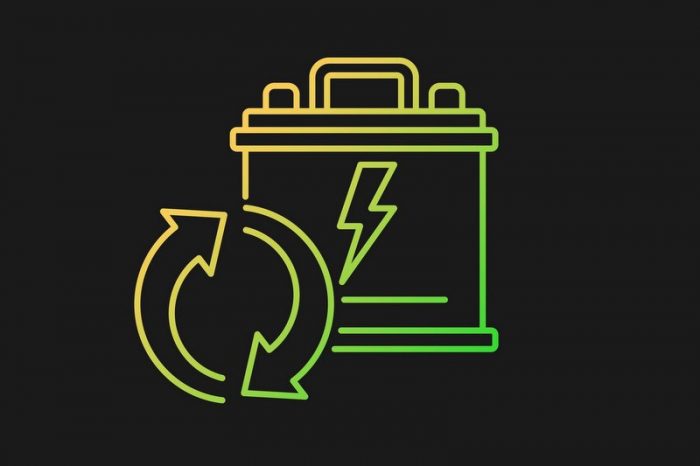
The global race to produce enough batteries for energy storage applications is only beginning to pick up speed. While many battery startups are investing in lithium chemistry R&D and production, both newer and more established companies with long experience in lead-acid batteries also are making technological advances in materials and designs to keep pace with demand.
For many energy storage system adopters, the greatest advantage of lead-acid-based battery storage may be that the upfront cost of installation is much less — some say 40% to 50% — than the cost of lithium-based systems. Lower upfront cost means more residential and commercial energy storage systems will pencil out, which accelerates adoption rates.
However, this lower cost for lead-acid systems is often counter-balanced with the need for more maintenance and a shorter cycle life. Two or more lead-acid batteries might be needed in place of each lithium battery in a residential or commercial storage system. Only time, and a few years of actual lithium performance documentation, will tell what the true lifetime ratio of lead to lithium will be.
Nano-Carbon enhances lead chemistry
Good news for lead-acid chemistry include recent advances in the use of nano-scale carbon in the construction of so-called carbon-lead-acid batteries, which are reducing acid volume requirements and maintenance frequency, while extending cycle life.
Carbon nano-coatings, perhaps the current leading materials advance for lead-acid batteries, yield substantial recharge performance gains. For example, Advanced Battery Concepts’ GreenSeal bipolar batteries can recharge twice as fast as standard lead storage batteries, provide higher power and offer an increased cycle life by about 300% compared to conventional lead storage batteries, according to CEO Edward Shaffer.
Similarly, Rolls Battery’s premium Series 5000 flooded lead-acid models, designed for residential use to large-scale energy storage, feature rigid heavy-duty plate structure, a unique modular cell dual-container case design, and can perform over 7,000 cycles at a 20% depth of discharge, and 5,000 cycles at close to a 50% discharge level.
“The addition of Rolls’ proprietary Advanced NAM nano carbon additive in the negative plate structure of flooded lead-acid models increases overall charge acceptance and lowered charge temperatures, offering improvements of 10-15% in charge efficiency, requiring shorter charge times, and improved performance in conditions of partial state of charge (PSOC),” says Jeff Myles, marketing manager for Rolls Battery Engineering.
Silicon mats reduce lead content
The use of silicon in lead battery design also offers strong performance benefits. “Advanced AGM (Absorbent Glass Mat) batteries that swap out lead grids for novel active materials have several advantages over lithium-ion or conventional lead,” says Gridtential CEO John Barton. Silicon wafer plates, when stacked and sealed, can eliminate non-uniform current density, increase material utilization, alleviate failure mechanisms, and improve performance of conventional lead electrochemistry, the company indicates.
“Silicon bi-pole batteries are lower cost. They have a much longer lifecycle and they allow for deeper discharge than lead batteries — typically limited to about 50% discharge,” Barton says. Bipolar batteries utilize an electrode that is a cathode and an anode at the same time.
“Deeper discharge means fewer batteries are required. The long lifecycle means fewer battery replacements will be needed. That all translates to a lower lifetime cost of ownership,” Barton reckons.
Safety and weight benefits
Safety is also advancing with new lead-acid designs, avoiding the risk of fire from lithium batteries. “Silicon bi-pole batteries require less battery management electronics and fireproof cages. When you need fewer electronics to track and report battery cell temperature and health, that saves on cost and complexity,” Barton notes.
Weight is also dropping for new lead-acid designs, which is helpful for installers who may prefer more smaller batteries to fewer heavier batteries.
“Our Silicon Joule batteries are up to 40% lighter because they use specially treated-silicon wafers in place of heavy lead grids,” Barton points out.
Recycling cuts replacement cost
Along with these advances, carbon-lead-acid batteries can be economically recycled at a rate of over 99%, in stark contrast to lithium batteries, for which recycling technology is still in its industrial infancy (and jury is out on how effective it will ever be). Energy storage generally is a green solution compared to fossil fuel use, but materials stewardship is an important element of the big picture.
While lead-acid batteries are considered hazardous, the mature global recycling industry currently makes the chemistry more environmentally friendly than lithium chemistry. While carbon-lead-acid batteries might need replacing in five years, compared to an expected but not yet proven 10 years for lithium batteries, installers can remove an old lead-acid battery and replace it with a battery that has been built from mostly recycled components.
“Lead-acid batteries are the most recycled consumer product in the world with a recycling rate of 99.3% in North America. Nearly 90% of the lead used in manufacturing our products has been previously recycled,” notes Myles.
Lead battery recycling embraces a cradle-to-grave management of all the materials used in the product. “The best news about our battery is at end of life, we can go get it, take it apart, flush it, and reuse the plastic and active materials,” says Shaffer. “We have developed a low-temperature process to convert the materials, so we can reduce battery replacement cost considerably. And we can do again and again; we’re not mining new lead (or lithium) and smelting it or grinding new plastic.”
Market demand from here
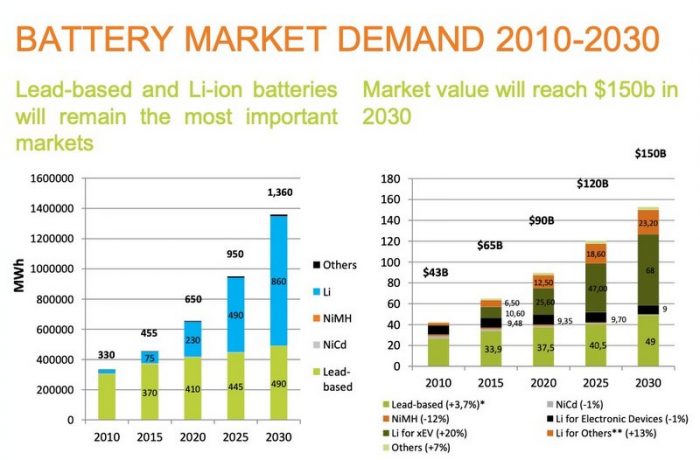
The struggle between Pb and Li-ion batteries for ESS (energy storage systems) applications is now heating up, suggests Dr. George Brilmyer, the Principal Consultant at Batt-Tek Consulting.
“In 2018, global Pb and Li-ion sales were about equal at $35 billion annually, but Pb sales were 4x greater in terms of GWh, so in 2018 Pb was 4x less in terms of $/KWh. Now in 2020 the global Pb battery market was worth about $37.5 billion, with 410 GWh produced. The global Li-ion market was worth $47.5 billion with 230 GWh. That translates into an average $91/kWh cost for Pb and $206/kWh for Li-ion so the price gap is now only 2.3x,” he says.
Brilmyer’s statistics are based on research by global battery market guru Christophe Pillot, the Director of Avicenne Energy, who conducted a 2021 study for the Association of European Automotive and Industrial Battery Manufacturers (Eurobat).
The study states: “It is very clear that both lead- and lithium-based chemistries will become the main players over the next decade. Both technologies will be critical in achieving the clean energy transition, catering for the specific application requirements in the automotive and industrial markets.”
The study suggests more specifically that for uninterruptible power supply (UPS) and telecom applications, “lead-based batteries will still be dominant in 2030”. However, “for energy storage systems, the preferred technology will be almost exclusively lithium-based by 2030.” The race is on.
Brilmyer would add that Avicenne’s numbers are global and sales figures do not differentiate between markets, which should really be considered in this type of analysis.
Charles W. Thurston is a contributor to Solar Builder.
Comments are closed here.