Consider the source part 3: PV failures on the rise
Solar PV panels — the symbol of the industry — are a bit of Rorschach test. What do you see when looking at one? The starting point of renewable energy generation or the end of a murky supply chain? A marvel of scientific innovation, or the shortcomings of global mass production? Maybe all of it. A solar field is large, its modules contain multitudes. All we can say for sure is every solar panel needs photons to generate electricity, the same photons our eyeballs use for sight. In our Summer edition of the magazine (subscribe here), we’ll illuminate a few solar panel production and procurement issues for you to see.
Part 1: The fight against forced labor in polysilicon
Part 2: Factoring in embodied carbon
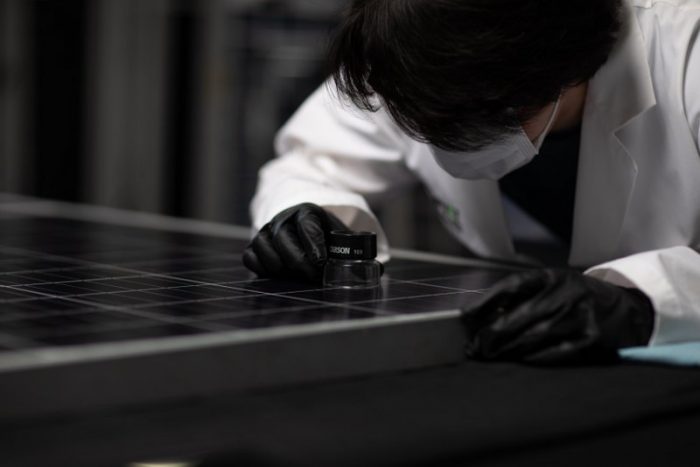
The road to a massive capacity expansion of high-power PV modules is proving to be bumpy. One in three participating PV module manufacturers failed to implement basic quality controls that protect end-users from safety failures, reports PV Evolution Labs (PVEL) in its 2021 PV Module Reliability Scorecard. Twenty-six percent of the bills of material (BOMs) eligible for this year’s Scorecard had at least one failure as compared to 20 percent in 2020.
“An unprecedented expansion of PV module manufacturing capacity is underway. New factories and production lines are vital as demand for solar power soars, but buyers must be vigilant to avoid the risks inherent to rapid growth,” comments Jenya Meydbray, PVEL CEO. “The preventable safety failures observed in this year’s Scorecard underscore the complex challenges that manufacturers face as they race to meet demand in a highly dynamic global market.”
Same old failures
Hiccups in scaling up and deploying new technology are to be expected, but PVEL’s results are disheartening in that modules are still failing PVEL tests in the same way they did five years ago.
“I wish I could say it was because we found this new degradation issue no one knows about, but instead these are problems that we’ve known about for years and reported on,” says Tristan Erion-Lorico, head of PV module business at PVEL, and in some cases it is getting worse. PVEL finds that more manufacturers are suffering from junction box failures, and that PID degradation rates have increased.
Plus, newer issues are cropping up too. The greatest number of failures occurred during the mechanical stress sequence, a test PVEL recently added to the PQP to address durability concerns, especially for extreme weather.
With GWs of modules being deployed every quarter (100 million cells are being soldered every day!) and with failures increasing in third-party testing — that sounds like an exponential increase in PV performance problems, right?
“Mathematically speaking that’s probably correct, but the exponent is quite low,” he says, tempering our panic. “I don’t know how many modules that include the BOMs in which we found issues are being sold, or what BOMs comprise what percentage of a module’s supply. It’s difficult to draw market-wide conclusions like that.”
Scorecard stats
• 117 model types of PV modules from 26 manufacturers were Top Performers
• 26 percent of BOMs had at least one failure (20 percent in 2020)
• 1 in 3 manufacturers showed safety failures due to junction box defects (1 in 5 in 2020)
• 5 manufacturers received their first Top Performer listing
Small stuff makes a big difference
Keep in mind there are also “plenty of examples of manufacturers doing things properly and achieving excellent results for all of these new technologies.”
The failures in these test results aren’t an indictment of the market; they are a reminder that solar modules are complex. Manufacturing modules to scale, in a dynamic industry in need of constant innovation and product updates is maybe impossible. Erion-Lorico breaks it down:
“Take a big player who has a 10 percent share. That means soldering 10 million cells a day. The scale is just enormous. Had they maintained their volume from a few years ago and nothing had changed about the product, they’d probably be able to make the perfect module every time now.”
Also consider how crucial every single component is to achieve that perfect outcome, especially with the global supply chain issues involved when scaling to meet demand. Multi-busbar modules, for example. PVEL ranks plenty of multi-busbar modules as top performers in thermal cycling. Yet, on average, the degradation of a multi-busbar module is higher than traditional 4 to 6 busbar modules. So, what are non-top performers doing to drag down the average?
Could be a zillion things. Erion-Lorico rattles off a few:
“All of their cell designs are slightly different. How many contact points there are on the ribbons has an effect. The ribbons can be slightly different. They can have different tensile strength or hardness depending on supplier.”
Another example: One manufacturer that did poorly in damp heat testing used the exact same BOM as the top performer except for the flux. “Just using the wrong flux in the string soldering process resulted in high levels of corrosion during damp heat testing.”
Large format questions looming
Another crucial note from our chat is that PVEL has not yet been able to put large-format modules through its PQP testing, despite many of these modules being announced a year ago and deployed this year (since our interview, PVEL has started testing a number of these modules).
“There’s not a lot of data on those, but we’re concerned they are getting substantially larger while the glass isn’t getting thicker and the frames aren’t getting thicker,” Erion-Lorico says. “The previous module designs worked when the module was 1 meter by 2 meters, and now they going 15 or 20 percent longer and 30 percent wider without corresponding changes in the materials being used.”
Based on PVEL’s assessment of the smaller format modules, they weren’t exactly overengineered. They used just enough glass thickness and just the right wafer size to be economically efficient and mechanically durable “and yet we found mechanical durability issues then.” Also, consider that 60- and 72-cell format modules already showed a substantial difference in load testing performance, with the latter, larger formats showing more microcracks.
“Now, instead of 72 cells that are 158.75 mm, they are now 182 or 210 without coming up with a new frame style with cross members or thicker frames or glass. I think that’s a risk.”
Bottom line: BOMs matter
Despite all we’ve discussed, Erion-Lorico, who is constantly thinking about all of these issues, remains optimistic.
“We’re finding issues that are concerning, but it shows why testing and qualification is needed, and you can’t just buy a module because you know the salesperson. We have recommended best practices for what you should do to mitigate these risks. The risks are real but avoidable if you do your due diligence.”
Comments are closed here.