Consider the Source part 2: Factoring in embodied carbon
Solar PV panels — the symbol of the industry — are a bit of Rorschach test. What do you see when looking at one? The starting point of renewable energy generation or the end of a murky supply chain? A marvel of scientific innovation, or the shortcomings of global mass production? Maybe all of it. A solar field is large, its modules contain multitudes. All we can say for sure is every solar panel needs photons to generate electricity, the same photons our eyeballs use for sight. In our Summer edition of the magazine (coming soon – subscribe here), we’ll illuminate a few solar panel production and procurement issues for you to see.
Here’s Part 1: The fight against forced labor in polysilicon if you missed it.
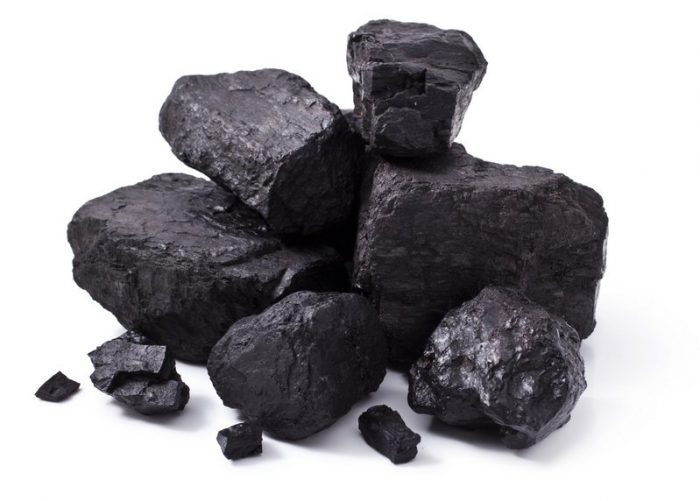
Solar photovoltaic technology produces electricity without generating carbon emissions, but carbon is tied to the manufacture, transportation and construction of the system itself. The “embodied carbon” of PV modules in particular is drawing more scrutiny these days.
An example is the European Union, which is putting a mandatory carbon footprint disclosure requirement for PV panels in place this year. France has already incorporated embodied carbon criteria for solar modules in its tenders, and South Korea has as similar policy.
“There isn’t a constraint to supply here, it’s a question of market demand and a willingness of the developers to embark on that,” says Andreas Wade, global sustainability director at First Solar. “If you look at PPA space, thought leaders here like Salesforce and Microsoft are no longer saying let’s look at the MW we purchase. They want to look beyond and maximize their impact with renewables purchasing.”
Indeed, the Renewable Energy Buyers Alliance (REBA) Institute is working with corporations to enable a demand signal for carbon transparency in solar manufacturing via the DISC-e program (Decarbonizing Industrial Supply Chain Energy). This will establish RFP standard language for zero/low carbon module procurement and Environmental Product Declarations (EPDs) request letters to send module suppliers.
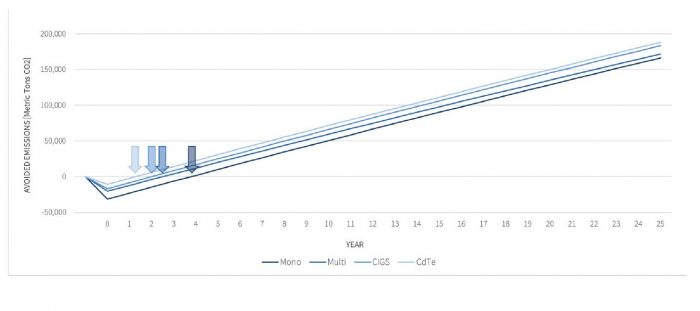
WattTime uses an avoided emissions analysis combined with lifecycle analysis to determine the net emissions benefit of a project. Here is an “emissions avoided” timeline for four different PV technologies when installed in California. The arrows = payback of net zero emissions..
“Commercial and industrial sector energy buyers currently participating in the DISC-e Solar Working Group have indicated the intent to prioritize request for proposal [RFP] bids with low-carbon solar panels as early as next year,” says Jen Snook, manager of supply chain and international collaboration at REBA.
Why PV modules?
Cement, steel and glass are carbon intensive inputs into the solar supply chain, for sure, but they are minor compared to polysilicon, the semiconductor in most PV modules. The difference in lifecycle emissions between the least and most emissions-intensive technologies can vary by nearly a factor of three, according to research done by WattTime.
Polysilicon, specifically, is the outcome of an extremely energy intense process: Quartzite is combined with charcoal or woodchips in a furnace at a high temperature to leave a silicon metal that’s 98 to 99 percent pure. That silicon metal is then sent for polysilicon production — a refining operation that converts the solid silicon metal into a gas, which is then ultra-purified through a chemical vapor deposition process and turned back into a solid. This leaves a 99.999999+ percent pure solar grade polysilicon. And that’s just the poly. Traditional wafer manufacturing uses a method known as Czochralski (Cz) ingot pulling, where that ultra-pure polysilicon is melted again, at over 1,440 C, and a single-crystal is literally pulled out of the melt over hours.
So, yes, to make a renewable omelet, you need to melt and re-melt a few eggs. That’s why the location of that process — and what ultimately fuels it — makes a big difference. The U.S. Department of Energy’s Argonne National Laboratory in 2014 noted a 50 percent increase in the carbon footprint of a module made in coal-powered Western China compared to one made in Europe. That is closer to 40 percent today according to Hemlock Semiconductor’s 2020 Sustainability Report.
“If you look at most U.S., European and Malaysian producers, their poly is coming from hydro power or mixed grids. Most of the poly in Western China is 100 percent coal-fired power,” says Michael Parr, executive director of the Ultra Low-Carbon Solar Alliance (ULCSA), which is comprised of PV manufacturers across the supply chain reducing the carbon intensity of solar manufacturing. “It is deeply subsidized and there’s not a lot of motivation to have it be energy efficient.”
Coal-powered module manufacturing means 260 lbs of coal burned in additional emissions compared to an ultra-low carbon module. REBA Institute estimates that deployment of low embodied carbon solar vs. regular solar over the next 20 years could avoid 14-18 gigatons of CO2 emissions, which on an annual basis would be greater than the emissions of the global aluminum industry in 2040.
“Solar buyers can send a strong signal to decarbonize solar manufacturing by buying lower carbon modules,” Parr says. “An ultra low-carbon solar eco-label is under development by an independent standards body.”
What to look for?
• Most of Tier 1 suppliers have done a full-blown ISO 14040 life cycle assessment. Check those out.
• EPEAT labels. The ISO 14024 certified Global Electronics Council (GEC) manages the EPEAT Type 1 eco-label, which is a registry for sustainable electronics. Last October, GEC debuted categories for PV modules and inverters. EPEAT criteria judge the full product life cycle and are based on the industry’s first sustainability leadership standard NSF/ANSI 457. It is incorporating embodied carbon into this label.
• French carbon certificate. You could possibly specify modules that are being sold in the French or South Korean markets, which have done their own calculations in terms of acceptable embodied carbon levels.
• The ULCS eco-label. The GEC is currently developing an ULCS designation for PV as well that will be added to their current EPEAT PV sustainable eco-label. This will provide a single eco-label for buyers seeking solar modules with a low-carbon footprint.
Domestic example
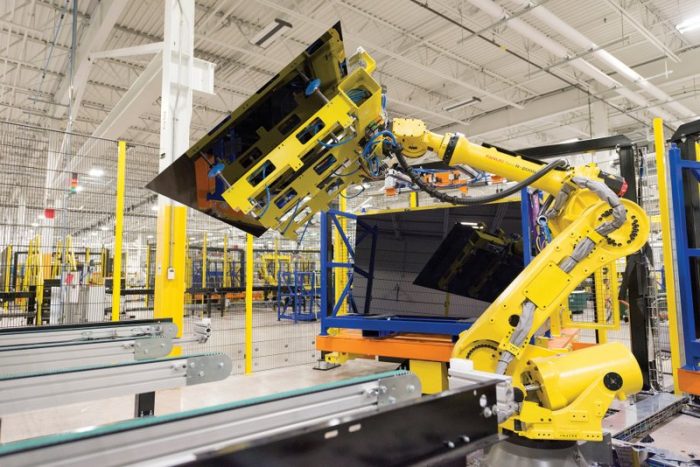
First Solar has the only PV module currently listed in the EPEAT registry. According to its 2020 Sustainability Report, in 2019 alone, First Solar reduced its GHG emissions intensity by nearly 40%. Its manufacturing energy intensity (energy consumption per watt produced) decreased by 36% compared to 2018 to 0.16 kWh per watt, primarily due to the increased throughput and efficiency of its Series 6 manufacturing process. In 2019 and 2020, First Solar received an A- from the Carbon Disclosure Project (CDP) in recognition of the company’s disclosure and management of its climate change risks and greenhouse gas emissions. In 2020, it joined RE100 and committed to powering its global operations with 100% renewable energy by 2028.
Green wafers on the way
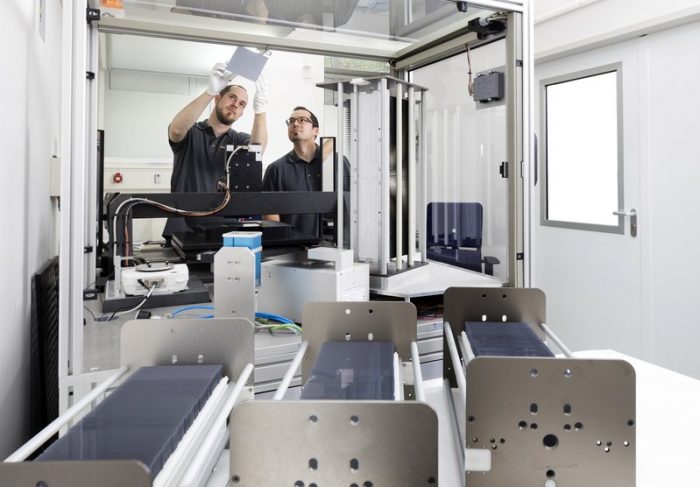
One contender looking to reduce the carbon footprint of wafers is NexWafe. Spun out from Fraunhofer Institute for Solar Energy Systems ISE in 2015, NexWafe’s Green Silicon EpiNex silicon wafers production “eliminates intermediate steps and avoids mechanical machining from ingots,” says NexWafe CEO Davor Sutija. “This reduces waste to nearly zero, and means we form much thinner wafers that are highly performant. This doubles the amount of watts per gram of silicon. Since our wafers are not sawn from ingots, no etching is required to remove saw damage, meaning they can be used in many low-temperature cell process lines.”
NexWafe ensures that 95 percent of the silicon in the chlorosilane feedstock ends up in the wafers, minimizing waste and eliminating the many energy intensive steps inherent in traditional Cz wafer manufacturing. The result is more watts per gram Si feedstock and 70 percent less energy used in the wafer manufacturing itself.
NexWafe’s focus is on n-type monocrystalline wafers for high-efficiency cell lines, especially those using HJT, TopCon or IBC cell technologies. NexWafe expects to complete its commercial readiness in 2022 and is positioned to scale-up and break ground on a factory with wafer capacity equivalent to 400 MW cell equivalent.