How smart tech is driving solar PV jobsite efficiency
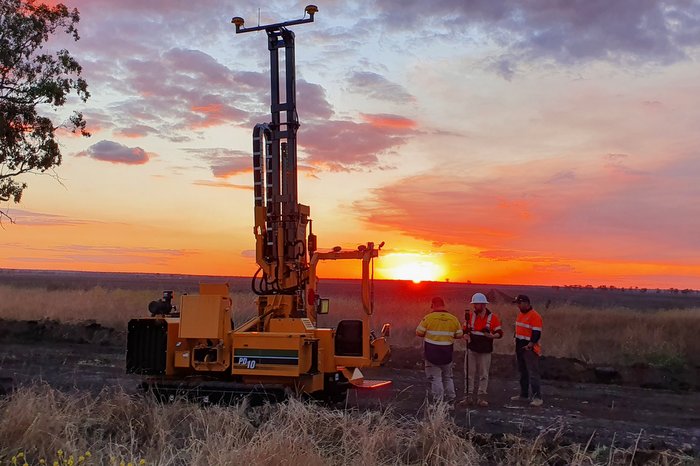
Solar balance-of-system (BOS) costs are dropping like a stone, thanks in part to the jobsite efficiency gains brought on by new and developing smart technologies. Indeed, solar EPCs have increasingly adopted new jobsite efficiency technology over the past two years, and the trend is headed upward, suppliers say.
These improvements in jobsite efficiency all translate into machine and/or man-hour savings, which of course, mean cost savings. While some solution costs are more readily amortized over a larger solar array, these same solutions often are available for smaller jobs, since the specialized sub-contractors that license the tech can schedule multiple jobs in a day, if a larger job is not tying up the equipment.
“On one end of the spectrum, there may only be a need for a few piles for a distributed site, and on the other end, a site may need tens of thousands of piles; it’s all scalable, and you really can’t do it without the machines,” says Ed Savage, the product manager for utility tractors and pile drivers at Vermeer.
Machine controls become standard
One critical piece of technology being rapidly adopted by solar EPCs is the machine control system, particularly for driving piles. Some posts in an array need to be sunk 10 ft, which excludes normal manual labor. Beyond the mere feat of driving the pile, design tolerances for vertical positioning now routinely stipulate a 1-degree maximum deviation. Here, machine control systems are the only real option.
One solar-focused machine control company, Carlson Machine Control, can adapt its smart 3D control system to any machine used for pile driving, as well as for other equipment like horizontal drills, frequently used for laying conduit. “There’s not anything out there we can’t position,” says Tim Jones, director of the company.
Carlson’s PDGrade, optimized for the solar industry, is a machine guidance and positioning system that uses Global Navigation Satellite System information (GNSS) for pile driving applications. The system includes machine sensors, 3D operator screens with information layering capability and WiFi communications that can be accessed by workflow managers and others. The system provides operators with detailed information such as pile navigation, pile location, positioning and height information and project progression tracking.
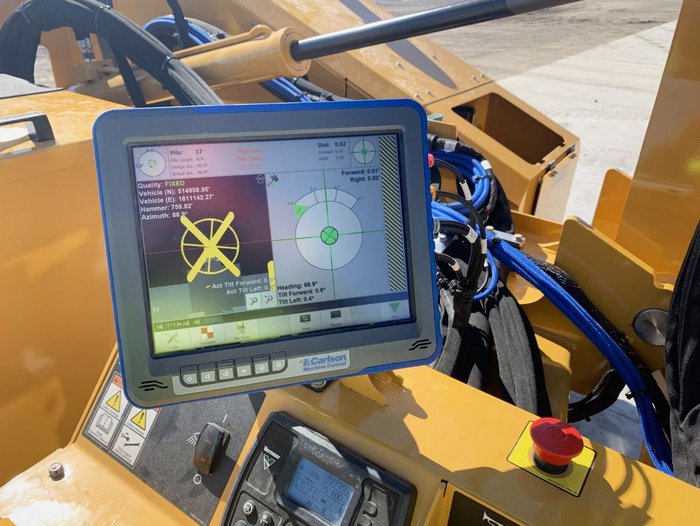
Carlson’s supporting fleet management solution, Carlson Command, is additionally supportive of pile driving applications. Site supervisors are able to monitor multiple and single machines with different viewing options for productivity analysis as well as custom project planning.
Another machine control system provider, Trimble, has metered massive labor cost savings through the use of its equipment. “Customers have found that they can achieve a 50 percent reduction in labor costs, and up to an 80 percent reduction in survey costs versus traditional methods,” says Brian Choi, the head of drilling and piling operations for the company.
Several years ago, TerraSmart, a utility-scale solar solution provider recently acquired by Gibraltar Industries, teamed with SITECH Nevada to equip five drill rigs with the full 3D Trimble Drilling System. In just four months with the Trimble-enabled rigs, crews completed the rock drilling portion of the process 50 percent faster than traditional methods.
McCarthy Building Companies teamed with Trimble and Tennessee-based SITECH Tri-Rivers to install Trimble’s Piling System on a GAYK Hydraulic Ram piling machine to support a 400-acre utility-scale solar field project in Millington, Tenn. The team used Trimble Business Center to process and prepare geospatial data so it can be read by the piling system. The pile plan included pile length, elevation, required embedment depth and alignments. Once exported to the Trimble system, the plans were visible by the operators from the on-board displays to facilitate drilling. Operators were also able to view completed piles compared against planned piles in both 2D and 3D views.
Using this 3D machine-guided approach, the contractor reduced the labor required for prep and pile installation by more than 50 percent, reduced the crew required from 12 people to a crew of three or four people.
With a more precisely defined labor cost estimate for a prospective project, solar bids can be crafted more competitively. “When EPCs are bidding for solar contracts, they now can make an offer that is a lot lower than a competitor using traditional methods,” says Choi.
Automating panel placement
Panel handling has long been a challenge for solar installers, but now automated systems are capable of doing the heavy lifting. For example, RE2 Robotics is now offering a system that uses mobile outdoor, autonomous robotic technology, which includes computer vision and machine-learning to enable the autonomous transfer, manipulation and placement of PV modules.
RE2 Robotics announced in March that it has been selected for $1.9 million in funding from the U.S. Department of Energy Solar Energy Technologies Office (SETO) to develop a robotic system for the Outdoor Autonomous Manipulation of Photovoltaic Panels (O-AMPP).
“Using RE2’s mobile intelligent manipulation technology, we seek to improve labor productivity, bolster worker safety, reduce construction costs and improve the efficiency and quality of installation by automating processes that are currently done manually,” said Jorgen Pedersen, president and CEO, in a statement.
Aerial mapping for better baselines
Aerial mapping also has come a long way since the first drones showed up at Intersolar a decade ago. Mapping now incorporates smarter and better-equipped drones, low flying aircraft equipped with light detection and ranging equipment (LiDAR) and satellite imagery from a host of free and for-fee sources.
These aerial systems can help in site design, post placement, commissioning and followup O&M. While the former functions can be cost savings, the real value of aerial analysis comes in at commissioning.
“We have benchmarked an average of 1.9 percent of total production adversely affected at commissioning, and we have found that when we don’t do a commissioning inspection, in year two, more anomalies tend to arise,” says Shane Carey, the marketing coordinator for Raptor Maps.
All that data is traveling more efficiently, too. In its annual Global Aerial Inspection Report, released in Q1, Raptor Maps included a new statistic: collaboration. The company discovered that, on average, asset owners share their PV system inspection results with 22 other users. The most frequently shared analyses were IEC TS 62446-3:2017-compliant inspections for commissioning and warranty claims and inspections incorporating on-site pyranometer data.
“The data and our customer interactions indicate that by leveraging software to collaborate with counterparties, owners and operators receive more positive resolutions from EPCs and module manufacturers,” says co-founder and CEO Nikhil Vadhavkar. “Additionally, owners have become more sophisticated and are setting more appropriate thresholds for remediation, which has reduced the barrier to collaboration with their O&M. … Software is now a requirement, and we all must do our part to collaborate effectively, achieve positive outcomes and keep the proverbial solar flywheel spinning.”
Charles W. Thurston is a contributor to Solar Builder.
Comments are closed here.