How new solar module technology lifts efficiency, limits price
The SolarCity technology is a silicon-based bifacial PV cell, which combines “n-type substrates, copper electrodes, thin-film passivation layers and a tunneling oxide layer that yields high conversion efficiencies.” This Triex technology should be available at close to 55 cents per watt by the time the Buffalo plant hits its 10,000-panel-per-day peak, Bass says. The company also projects a 10 cent per watt savings in BOS equipment and labor as a result of the higher efficiency panels.
Trina, too, is continuously pushing up the efficiency bar.
“We have broken the record four times thus far and now offer 21.5 percent efficiency with an output of 330 W from our 60 cell modules,” Tian notes.
Funding R&D for new ideas
New research is also continuing in order to find solar power production from new technology approaches. For example, President Obama recently authorized $24 million to fund 11 new solar technologies within ARPA-E’s Micro-scale Optimized Solar-cell Arrays with Integrated Concentration (Mosaic). Mosaic project teams will design technologies and concepts for cost-effective, high-performance solar modules “using thousands of small lenses to concentrate light onto an array of PV cells to achieve higher solar-to-electricity conversion,” the agency reports. The micro scale concentrated PV (micro-CPV) technologies will be integrated into flat plate solar panels to improve efficiency and reduce cost.
Sneak PV-eek: Rayton Solar’s radical new process
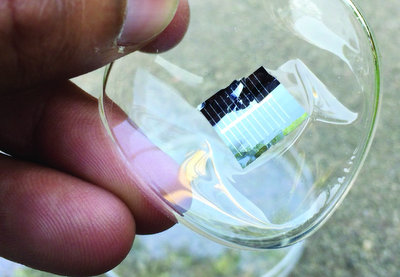
The Rayton process produces an extremely thin layer of silicon — 4.7 micron thick as opposed to a conventional 200-micron thick layer.
The technique used for cutting silicon with a diamond wire saw started in the ’50s in order to cut tiny wafers of silicon for microprocessors. This remains the predominant way to cut silicon for uses such as solar PV; it also leads to a significant amount of waste in the form of silicon sawdust because the process wasn’t originally concerned with reducing waste for large-scale production. So, as we now start to cover acres of land in silicon solar technology, is there a better way?
Andrew Yakub, the brains behind Rayton Solar, believes there is, specifically the process of using a wire saw to cut silicon.
“We developed a process using ion implantation to cut our very thin pieces of silicon, and there is zero sawdust in the process, so it allows us to increase the yield of the raw silicon and get a 60 percent reduction in the cost to make a solar panel,” he says.
The Rayton process produces an extremely thin layer of silicon — 4.7 micron thick as opposed to a conventional 200-micron thick layer. Because of this, Rayton uses a higher quality silicon that is about 10 times as expensive.
“So that gives a 25 percent efficiency boost, but by using so little we get a huge cost reduction,” he says. “We would be able to manufacture for 22 cents a watt and sell for 60 cents a watt.”
The technology is still in the process of UL-certification, but Rayton expects to begin manufacturing in 12 to 18 months.
Global markets
More of the major players are developing regional production capabilities as the market expands at its current rapid pace. Trina is now expanding production in China, India, Malaysia and Thailand and eventually will produce somewhere in South America to meet growing demand.
Canadian Solar is selling into 40 markets around the world, Koerner says. While the company has production capability in China, its Canada plants can produce 500 MW of panels per year, Koerner says. Next up for a production base is likely Brazil, he says. Brazil has high local content requirements for solar components — rising to a blanket 60 percent in 2020; but when these are met, low-cost loans are typically available from the national development bank BNDES.
TenKsolar will also add 80 MW of panel capacity in Thailand over the next year, matching its home production level. The company also has limited production capability in China, where it recently penetrated the rooftop markets.
Among new players in the panel manufacturing space is IUSAsol, based in Mexico, which made a commitment in May to invest $750 million in its Pastejé, state of Mexico assembly plant, to reach a production capacity of 400 MW per year. The company also has been considering a facility in Merida, Yucatan.
Solar roof shingles
Advances are continuing in the solar shingle niche as well. CertainTeed’s Apollo II shingle “is now wholly manufactured in the United States and we have upgraded to higher efficiency mono-crystalline cells to increase power production to 60 W,” says Chris Fisher, solar product manager for CertainTeed, based in Malvern, Pa.
Warranties Extend
CertainTeed also has bolstered its warranty provisions. “We provide a 25-year warranty on power output for CertainTeed’s solar modules, warranties ranging from 10 to 25 years on the other system components, and a 15-year workmanship warranty on the installation of the system,” Fisher says. “Our warranty also provides for us to reimburse the installer for labor needed to replace a defective product.
“Further, if there is an installation workmanship issue and an installer is no longer in business at that time, the homeowner has direct recourse with CertainTeed,” Fisher adds. “Overall, we are the single warranty provider for both the homeowner and the installer.”
Similarly, Canadian Solar is now offering 30-year warranties on its panels. And LG’s new 72-cell panels come with a 25-year performance warranty, reducing an expected loss of 3 to 2 percent in the first year and reducing the following 24 years of loss from 0.7 percent to 0.6 percent per year, the company says.
new solar modul technology and i am indian and i have solar power project in makeing indaia 1 megawatts cost and letest technology to sending my email