Lean manufacturing lessons to manage solar supply shortages, skyrocketing costs
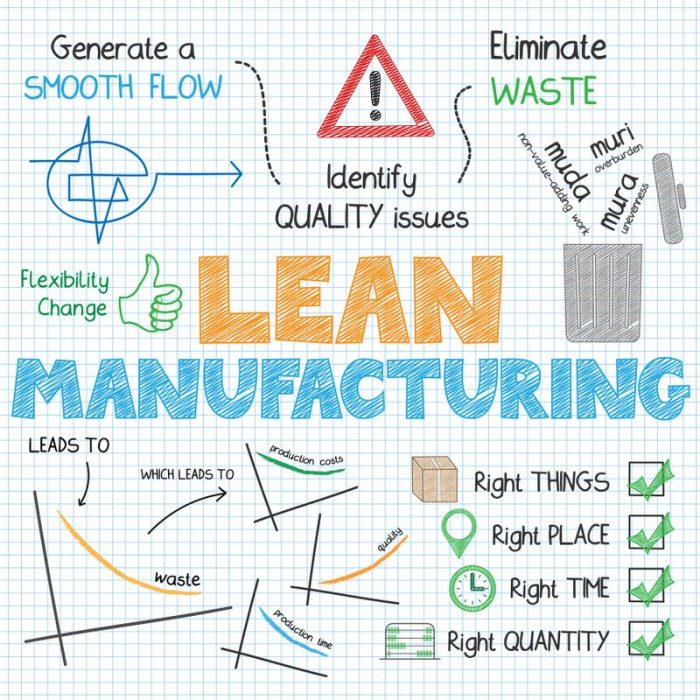
The pandemic and climate change-related disasters have dismantled our global supply chain and impacted every organization — no matter the industry, business model or location. In the solar sector, in addition to unreliable sourcing, we’ve also struggled with rising costs that specifically impact tracker, racking and PV manufacturing. In fact, according to analysts at the consulting firm Rystad Energy, manufacturing costs for PV modules surged 50 percent from 2020 to 2021, as the cost of polysilicon, a core PV component, saw a 300 percent cost increase. Other raw material costs for silver, copper, aluminum and glass have jumped substantially since January 2020, increasing module prices.
As racking and tracker suppliers, we have experienced a similar situation as the price of steel has skyrocketed. A 5-MW tracker project would’ve averaged in the 17 cent per W range last year at this time; these projects are now ranging from 31 to 33 cents, almost entirely due to higher material costs.
Clearly, a crippled global supply chain, rising materials costs, overseas shipment delays and additional associated freight costs have fused into what feels like a major catastrophe. It makes sense that solar asset owners, developers and suppliers are preoccupied with project costs, sloth-like lead times and the aforementioned supply chain issues.
Steel pricing has definitely thrown off the economics, but that is offset somewhat by the overall drop in deployment costs, as well as the incredible demand for clean energy. According to SEIA, the cost to install solar has dropped by more than 70 percent over the last decade. Solar has ranked first or second in new electric capacity additions in each of the last eight years. In 2020, 43 percent of all new electric capacity added to the grid came from solar, the largest such share in history and the second year in a row that solar added the most generating capacity to the grid.
In the distributed generation market — 10 MW and under — we’ve seen a significant amount of demand, and it continues to grow. Solar installations are expected to expand significantly over the upcoming decade. DNV’s Energy Transition Outlook forecasts that new solar PV installations will triple by 2030.
Positive news to be sure. For the short term, however, we do expect supply chain disruptions may delay or cancel projects for at least a year or more.
That being said, there are some insights and key learnings that can potentially lessen these impacts.
As an executive with more than 25 years of experience in supply chain, advanced manufacturing and operations, I look to my “lean” principles to help our partners navigate through these challenging times.
Let’s take Just-in-Time (JIT) as an example.
In manufacturing, speed to market and costs of production can make or break a company. JIT is a standard lean manufacturing practice, essentially a workflow methodology aimed at reducing flow times within production systems, as well as response times from suppliers and to customers. Those core principles can be expanded and applied to mitigate the supply chain challenges we face. The advice goes something like this:
- Maintain visibility into your supply chain
- Control risks and costs as much as possible
- Ensure your suppliers are knowledgeable, reputable and collaborative
You may be asking, ‘well, what does that mean in actual solar project commissioning, installation and energizing?”
On the supply chain side, ‘visibility’ is simply knowing where materials are sourced. Domestic sourcing is an important consideration and a pathway to reduced risk and costs. In the case of mounting structures, sourcing steel locally the majority of the time circumvents overseas shipment delays and freight costs and offers protection against global shortages. And, domestic manufacturing typically ensures a much faster turnaround — plus the opportunity to fine-tune or pivot as needed.
Working with suppliers that are laser-focused on tracking costs and speeding delivery times is equally important. A supplier that has the capacity to be strategic on margins and is willing to pass on the absolute best pricing is the one you want to work with. Partnerships that are made up of dedicated, solution-oriented teams will absolutely make a difference. Manufacturing expertise, a domestically sourced supply chain and a collaborative, roll-up-your-sleeves mindset are key differentiators when comparing options.
Despite rising material costs and supply chain woes, assessing the strength of your supplier network and their manufacturing capacities will go a long way toward project success. Finding reliable suppliers and logistics providers, building supply chain sustainability as much as possible, and insisting on visibility and information exchange are key aspects.
One thing is for certain: The solar industry consistently continues to persevere and rise above expectations. And, my bet is that the years ahead may just prove to be a perfect example of our industry’s resilience.
Eric Goodwin is director of solar business development with OMCO Solar and leads the sales and marketing team. He has more than 25 years of experience in supply chain, manufacturing and operations. Prior to OMCO, Goodwin helped lead the tracker start-up RayTracker to a successful exit to First Solar in 2011, and also led First Solar’s Supply Chain Tracker launch.
Comments are closed here.