Large and in charge: Storage integrators, EPCs share 7 trends in MW-scale battery projects
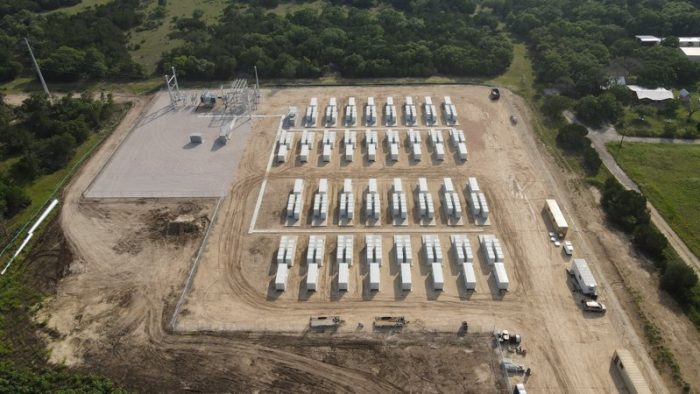
Large-scale energy storage is a pretty big deal right now in the sense of both status and economics. One to four MW-hour sites are being designed and pumped out faster than ever, with most of the energy storage growth last year coming from large-scale installations by utility companies, according to the U.S. Energy Storage Monitor from Wood Mackenzie and the U.S. Energy Storage Association.
“The duration, scale and geographic diversity of projects are expanding,” says Yann Brandt, CFO of FlexGen, the second-largest U.S. energy storage technology company (that just landed another $150 million equity investment). “Project structure is heavily driven by regional policy constructs.”
For example, he points to the Resource Adequacy rules of the California Independent System Operator (CAISO) that are driving four-hour duration projects with capacity and efficiency guarantee structures that enable bankability of off-take agreements. In the Electric Reliability Council of Texas (ERCOT) merchant market, one- and two-hour projects have dominated the interconnection queue, “owing to importance of ancillary service and low cost of installing one-hour systems.”
In all cases, Brandt says he is seeing more projects with strong economics, which is the largest driver of development. “We are seeing that storage is not only the enabling technology for the energy transition, but also a key building block for more resilient and cost-effective municipal, cooperative and rural utility systems,” he says.
This all means large-scale storage is a pretty big deal to solar EPCs, too. We chatted with five leaders in this space to understand today’s deal parameters, emerging battery technology and how they have evolved their operations to build out the solar + storage era of the U.S. grid. Here are seven takeaways.
Utility value stacks and payback evolve with improved storage economics at higher durations.
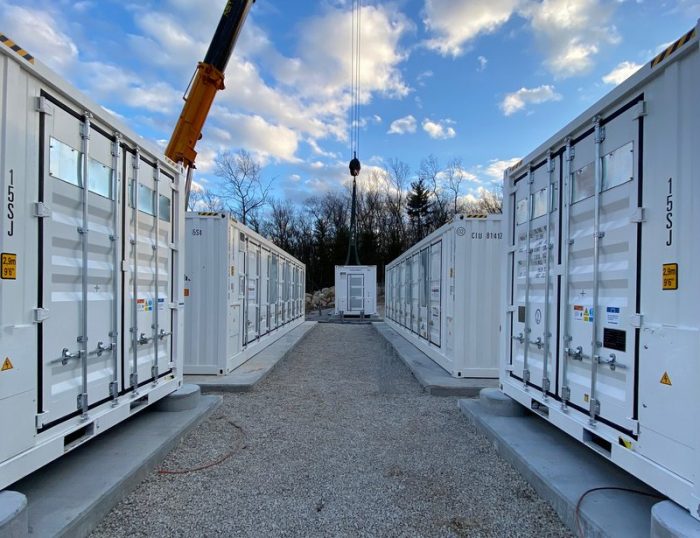
The first wave of large-scale storage projects paired with solar over the past five years tended to feature short-duration storage solutions (<one hour) because they were the first storage solutions to become economical.
“These short-duration projects were focused on providing ancillary services, such as frequency regulation, to enhance grid resiliency and were paired with solar to get the economic benefits of the 30 percent ITC,” notes Mark Frigo, VP of energy storage at Nexamp. “But now, as the cost of batteries drops, the shift of applications has moved toward longer duration [i.e. four hours] to provide a more firm or shaped solar product.”
Over the past 12 months there has been a noticeable shift in how storage technology gets utilized as it relates to value stacking and deals for off-takers.
“As utilities across the country pursue carbon-neutral goals, having firm renewable power sources are important in achieving these goals,” says Dhruv Patel, senior vice president of renewables for McCarthy Building Companies.
“We are currently installing projects with utilities with payback periods of between two and four years,” Brandt says.
Battery size is status quo, but longer durations are close.
Grid operators are increasingly calling for the commercialization of storage technologies that can dispatch for longer periods of time, especially during extreme weather events. The widespread adoption of longer duration energy storage systems (10 MWh+) isn’t here just yet, but it’s on the horizon.
“We have certainly seen the size of energy storage projects grow as traditional peaker plants are now being replaced by large-scale energy storage systems,” says John Zetterstrom, director of business development, energy storage for CS Energy. “We also see more utilities and grid operators using energy storage to solve a myriad of distribution and transmission problems, ranging from easing circuit congestion to providing black start services to substations.”
“While the preferred eight- to 10-hour duration is on the horizon, and the industry is pushing for it by 2026 or 2028, today’s focus is on two- to four-hour duration systems,” Patel says. “This is being accepted to allow for the industry to gain more knowledge and experience, which will ultimately have a positive impact on the longer-term systems when they are ready.”
“As the power generation and financial communities have gotten more comfortable with the technology, we are seeing the scale of projects scale-up rapidly,” Brandt says. “Three years ago, a 40-MWh project was a very large project in the market. We now have many projects in our pipeline at between 200 MWh to over 1 GWh in a single project.”
“A 500-MW RFP seeking long-duration energy storage was recently issued in California, which illustrates the increasing realization of the need for long-duration storage,” says Barrett Bilotta, president and managing partner of Agilitas Energy.
Key system attributes include modularity, power density and flexibility.
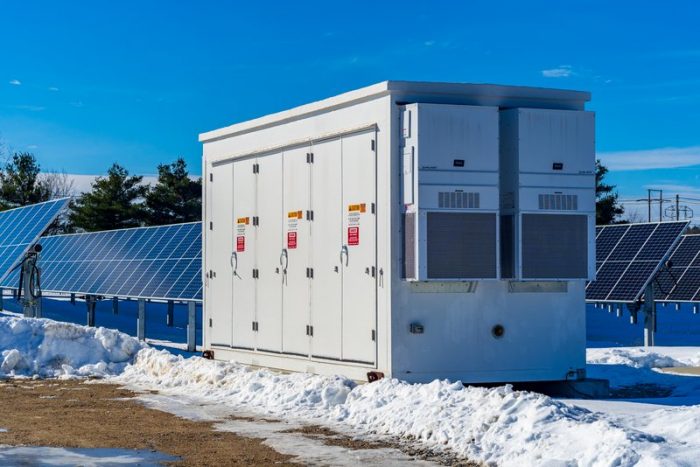
There is much more to an energy storage system than the battery chemistry, and it’s with these system components that EPCs are innovating, bringing together various vendor solutions that best complement the solar project’s parameters and site constraints.
“We’ve utilized the new modular, power-dense and containerized products to achieve our desired system size and capacity within limited footprints, especially in land-constrained cities like New York, or on the sites where the best balance between solar and energy storage requires minimal footprint for the ESS containers,” Bilotta says. “We have been partnering with energy storage integrators and manufacturers that can provide us with solutions that meet our project requirements with a minimal footprint. We always favor energy storage solutions that are more power- and energy-dense.”
“We have created a truly vendor agnostic approach,” says Kelsey Hogue, commissioning manager for energy storage at CS Energy. “We tailor our equipment selection and designs to the specific use case for each project, factoring in safety, cost, energy density, site access, feasibility, long-term servicing and warranties.”
For energy storage projects where sites are constrained by space or elevation changes, Hogue is seeing that preloaded, custom cabinets are coming to market as a versatile tool in developing projects. Several vendors are now deploying these types of energy storage systems or have them on their product roadmap.
“It’s also worth noting that recent supply chain constraints within the industry, which are being caused partly by the EV market taking up an enormous amount of battery supply, has caused a shift from container to prefabricated plug-and-play energy storage, HVAC and fire suppression systems,” Patel says. “These are delivered on site and installed rather than traditional containerized solutions, which require additional onsite installation work. McCarthy prefers the plug-and-play because it is easier and more efficient to design and build into a storage project.”
Lithium is still on top, but NMC is on the way out.
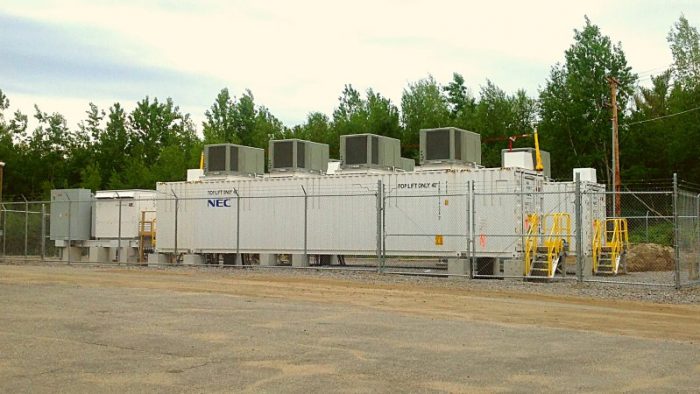
The lithium nickel manganese cobalt (NMC) chemistry led the energy storage industry out of the gate, but it’s only a matter of time for new chemistries to overtake it, largely due to the flammable and toxic nature of cobalt. That time might be right now.
“Initially, NMC was the battery chemistry of choice due to its high energy density characteristics installed in short-duration applications like ancillary services,” Frigo says, noting that Nexamp has a number of energy storage projects underway featuring lithium iron phosphate (LFP) chemistry. “One important benefit of LFP is that it does not have cobalt, which is an expensive metal. It also has better safety characteristics as it has a higher temperature threshold for thermal runaway.”
“Many of our early projects deployed NMC cells, but recently we have favored LFP cells as they provide a stronger safety profile, potentially longer lifespan and seem to be more cost-effective,” Bilotta says. “We believe that lithium-ion batteries are the most cost-effective solution for our projects as they are the durable, energy dense solution that can respond quickly and effectively to our various use cases.”
“We are actively evaluating a range of alternative chemistries, including emerging Zinc chemistries,” Brandt says. “LFP currently has the advantage of manufacturing at scale, which is continuing to drive pricing down. We do expect long-duration chemistries will play a significant role on the grid as the technology improves.”
Advancements in workflow and service are saving time and money.
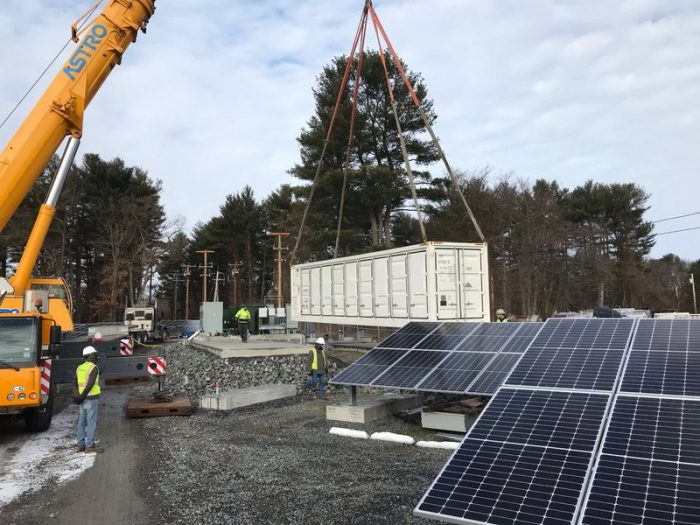
Two areas McCarthy has been innovating most recently are commissioning and reactive power strategy, Patel tells us. The first, a remote commissioning service, uses a virtual technology developed in partnership with an integrator.
“Our team has commissioned sites remotely, which brings the benefits of expediting the commissioning process, optimizing the overall schedule and cost savings,” Patel notes.
The second is a reactive power strategy. McCarthy’s engineers look at the use case of the battery system, the solar PV system and substation system design to optimize the overall plant’s power output.
“Through our process, McCarthy’s teams evaluate and adjust, to find efficiencies in equipment throughout the design process to incorporate ways that design can better address power capacity, and owners can save by minimizing the number of inverters and capacitor banks needed in the substation yielding additional savings and schedule benefits,” he says.
At CS Energy, its commissioning team can easily aggregate data from the power conversion system (PCS) or energy storage system as well as handle the communications throughput from one end of the system to the other. “This in turn has enabled us to reduce project timelines and costs as well as deliver real-time system information to our customers,” Hogue says.
“It’s hard to point to a standard approach that meets all needs because every storage solution varies depending on a customer’s situation and application,” Frigo says. “As such, at Nexamp, we do not have a portfolio of standard solution offerings, but we do have a deep bench of internal expertise and technology partners that we work with to ensure that the best solution is developed and implemented for the customer.”
Safety, of course, is also top of mind.
McCarthy engages stakeholders early in the design process and educates everyone on how the project’s technology works. The team collaborates to develop multiple layers of safety precautions that are designed to isolate issues and help to ensure any issues are quickly identified, contained and addressed.
“By considering increased layers of safety during the design-phase, the precautions can be built into the project more efficiently and cost-effectively, as opposed to it being an after-thought that requires re-design or re-engineering to accommodate,” Patel says.
CS Energy has also placed a focus on developing long-term service for energy storage systems in order to minimize costs and de-risk projects.
“We have designed our Long-Term Service Agreement [LTSA] offering to incorporate and align with OEM’s standard warranties for individual components in order to ensure our clients do not pay double for maintenance with multiple equipment providers,” Zetterstrom says. “We are also continuously improving our quality assurance program to ensure that systems installed by CS Energy meet or exceed all relevant safety codes and standards.”
In fact, CS Energy received the New Jersey Governor’s Safety Award as part of the 92nd Annual Governor’s Occupational Safety and Health Awards Program in 2020.
Challenges include supply chain, policy and the quality of newer, souped-up batteries.
The impact of supply chain constraints. “Early engagement and committing to partners at each level within the supply chain is the best approach as lead times are increasing throughout the entire chain,” Patel says. “With technology progressing at such a rapid pace and with supply chain limitations, it’s possible and potentially problematic that some projects will be inclined to take risks with technologies that have not been adequately tested. This could ultimately have a negative impact on the industry.”
Testing hurdles. “More and more jurisdiction authorities are requiring full-scale system testing [UL 9540A] on lithium-ion battery systems, and this can be challenging to accommodate because of the added costs and extensive amount of time needed to schedule, complete and summarize the testing,” Bilotta says. “This could be a major challenge for developers and system owners because many manufacturers or integrators do not have full-scale system testing on their products. Even if they do, any tweaks or changes they make to the system typically would require new testing, which would result in a significant amount of additional costs and time.
Interconnection and domestic supply chain still lacking. “We would like to see interconnection queue reform, as inefficient interconnection processes often cause major delays for projects, particularly in the Northeast,” Zetterstrom says. “Supply chain complexities are also responsible for a large amount of delays. It would be ideal if there were more U.S.-based energy storage production sites and if manufacturers utilized materials that were more abundant. We would also like for there to be greater factory integration of the newer safety technologies on the market and more attention paid to designing systems with NFPA 855 standards in mind. All of these factors would help to reduce costs for our customers.”
Policy has to keep leading. “Looking forward, consistent policy and regional market frameworks are critical to support growth of the technology by enabling predictable returns for investors and project owners,” Brandt says. “As the energy transition accelerates, storage is the key to driving the speed and success of that transition.”
Comments are closed here.