Commercial lithium battery recycling is finally economic
The long-sought solution for economically recycling lithium batteries at commercial scale finally is being built out in Chester, South Carolina, by Princeton NuEnergy (PNE), heralding the latest technology for the task: low-temperature plasma. The $11 million plant will be the first in the nation capable of so-called “direct” recycling of lithium-ion batteries from electric vehicles (EVs), consumer electronics, energy storage batteries and manufacturing scrap.
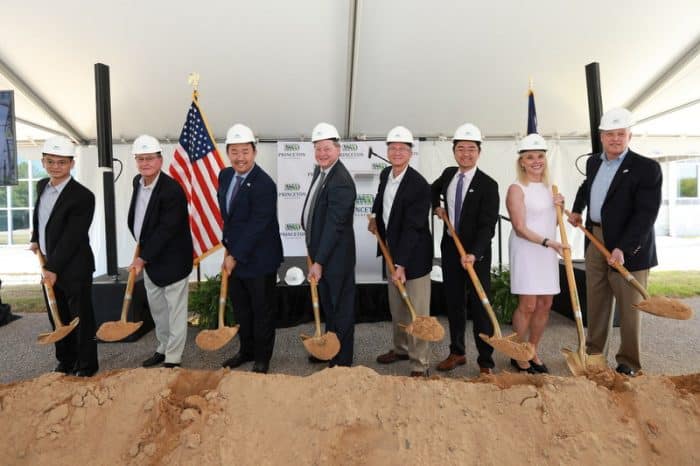
Upon completion, estimated production will be more than 10,000 tons per annum (TPA) of battery-grade cathode material, the equivalent volume necessary to produce about 100,000 EV batteries per year.
Compared to the existing commercial pyro- and hydro- metallurgical recycling processes — which has not been economic for lithium until now — the PNE process is about 40% less expensive, said Chao Yan, the company founder and CEO, in a recent interview with SB. “Hopefully, by the middle of 2028 we can generate a large volume of high-quality cathode materials out of these waste batteries.”
The solar industry, from large commercial solar + storage players to utility companies, also will play an important role in battery recycling soon enough.
“We are working with the U.S. bundled solar + storage providers to understand their strategies and timelines for batteries to reach end of life. We also are working with utilities company to understand their timelines as they build battery storage systems,” Yan said. “The solar the market is growing very fast right now and very soon, perhaps in five years, they’re going to have a lot greater need for battery direct recycling.”
How it works
The PNE low-temperature, plasma-assisted separation process (LPASTM) essentially burns off impurities in the battery metals under vacuum, yielding advanced blackmass — powdered metal mixtures — and rejuvenated cathode-active material. This improves on the standard commercial recycling process, which involves crushing and shredding the metals into blackmass through high heat or acid washing, prior to re-refining each metal.
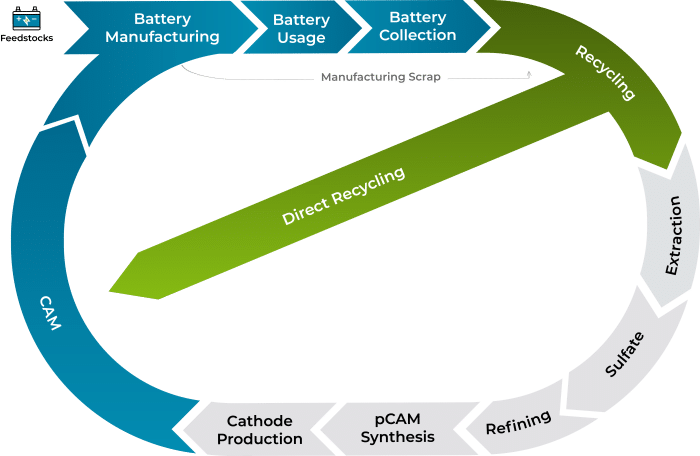
Different types of lithium-ion battery chemistries may contain metals such as copper, manganese, cobalt, and nickel. Blackmass is the active powder composed of the commingled metals used in the cathode and anode. The black color of blackmass comes from high concentrations of graphite in the anodes.
“The challenge for the industry has been that the quality of the blackmass after battery shredding battery is not good,” said Yan. Direct recycling can recover over 95% of lithium-ion materials found in all lithium-ion battery chemistries, without the destruction of the metal state in the battery, according to PNE.
Less waste, lower cost
The breakthrough LPASTM technology, in the works at Princeton for years by Yan and other researchers, has been patented by the university and licensed to the company. Funding for the tech has come from the U.S. Department of Energy, and commercial investors including notable EV player Honda, along with LKQ Corp., and battery recycler Wistron Corp. Among venture capital investors is Samsung Venture Investment.
The low-cost PNE process uses no acid for leaching, less water, and produces no refining emissions or other CO2 emissions, resulting in a 70% environmental waste reduction compared to pyro- and hydro- metallurgical recycling processes, said Yan.
“Think about the hydrometallurgical [acid wash] recyclers that are using thousands of tons of acid every month to leach the metals. We don’t use any acid,” Yan pointed out. “Not surprisingly, the permitting for acid recycling plants is extremely difficult.”
The new PNE process should help discourage the current global condition of an over-supply of traditional battery recycling capacity.
“The majority of the global overcapacity is coming from China, but here in the United States, we don’t have an overcapacity right now,” observed Yan. “In China, I would say, a lot of wrong decisions are being made in investing too much in conventional leach recycling technology, and most of them, are not making a making a profit.”
Strategic capture
One huge benefit of the PNE process for the U.S. battery and EV industry is the retention of the recycled metals within the United States. With no U.S. commercial solution previously available, spent lithium batteries are being shipped off to China or to Europe for recycling.
A recent report by DOE’s Offices of Small Business Innovation Research (SBIR) and Small Business Technology Transfer (STTR), entitled Redefining the Battery Recycling Supply Chain, points out the need for greater strategic use of the battery metals in EVs used in this country.
“Today, the majority of cathode and anode production is found in Asia – including China, Korea, Japan, and to a lesser degree, Europe – and requires the transshipment of materials around the globe to produce new battery feedstocks of precursors, cathode, and anode products. Because there is no guarantee that these feedstocks will return to the United States, creating a domestic U.S. supply chain to retain these critical materials and produce new product from recycled components is critical,” the report states.
Life-cycle partnerships
PNE’s strategy for growth includes developing partnerships with the players in every stage of the cradle-to-grave cycle from battery production to recycling.
“We are working with battery OEMs, EV OEMs and the recyclers who sort the batteries; basically, this is one ecosystem,” Yan said. “We basically help to close the loop that begins with the miners, then moves to the battery cell manufacturers, then the EV OEMs, and then the recyclers; we bring all the waste back to the cell manufacturer to make new batteries.”
As the EV industry matures, more attention will be focused on recycling, Yan suggested.
“The EV OEMs and the cell manufacturers should work together to think about battery life cycle, and design batteries that are easier to recycle,” he said. “Today, a lot of EV batteries are made using a lot of glue, which makes recycling more costly and difficult because of the disassembly process,” he explained.
DOE has been advocating battery life-cycle improvements for years. “During battery production, 10% to 30% of the original production materials do not become a final battery but result in manufacturing scrap. The recycling of manufacturing scrap and end-of-life batteries is increasing significantly as EV adoption and demands for the power grid storage grow,” according to the SBIR-STTR report.
The good news is technology like PNE’s is rising to the occasion. “It is anticipated that a tipping point may be reached by 2040 when as much as 50% of new batteries could be manufactured with recycled materials. This new source of battery materials is often characterized as ‘urban mining’,” the report observed.
“We are cheaper — and more environmentally friendly — than the mining process that would otherwise be needed to supply enough lithium to the industry,” Yan stated.
One way that PNE is seeking to strengthen the battery life-cycle is by providing recycling as a service. “Basically, we can provide a service for EV OEMs to recycle batteries for a fee,” Yan said. “That way whomever brings us the materials gets them back into their supply chain. We can reduce the cost of and the risk for the metal commodities, because they secure the materials themselves.”
Comments are closed here.