3 ways solar developers can get DG projects online even faster
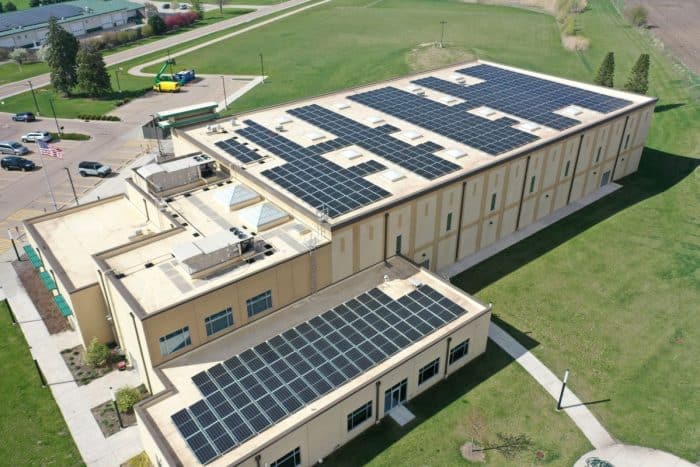
By Eric Lorenz | DSD Renewables
According to the Lawrence Berkeley National Laboratory (LBNL), nearly 2.6 terawatts (TW) of renewable energy were held up in interconnection queues at the end of last year — more than twice the United States’ total generating capacity. These bottlenecks, which have been created by the sheer number of renewable energy projects under development around the country in recent years, mean that subscribers in some regions won’t have access to the energy generated by these projects for up to five years or more for utility-scale projects.
The Federal Energy Regulatory Commission (FERC) is trying to address these delays with Order 2023, adjusting the processes utilities undertake before granting approval. In the meantime, however, developers are finding they can get additional solar power into communities and avoid delays by turning to distributed generation (DG) projects — a proven solution that is much quicker to deploy and takes advantage of the localized distribution network.
DG projects are generally fully operational within one to two years, but still interconnection and permitting hurdles are holding back projects from being deployed swiftly and on time. If you’re a developer who’s seeking ways to continue getting projects off the ground as quickly as possible, a few simple steps can streamline your efforts and ensure you receive the greenlight from utilities even faster.
1. Standardize equipment
You know the frustration of choosing the right inverters, racking, modules or other equipment for your DG project. Why have two dozen options in consideration when just a handful will suffice? With so many choices for components, balancing a standardized set of equipment with project flexibility will result in improved timelines across your portfolio.
Many factors are at play that can overcomplicate your procurement strategy, such as availability, local regulations, EPC/partner preferences or utility requirements. Narrowing your equipment selection to a smaller range of choices is likely to benefit bringing your DG projects online. By standardizing project equipment, you’re minimizing due diligence, simplifying the repeatability of your designs and streamlining the development process. This saves a lot of time in the documentation, interconnection and permitting phases, reducing the complexity and variability that often delays receiving permission to operate.
Taking this approach should involve close collaboration with utilities and manufacturers to ensure your chosen equipment meets technical and safety requirements while being compatible with existing infrastructure. When utilities are familiar with the components and configurations you’re using, they can more easily assess the project’s feasibility, leading to fewer setbacks caused by requests for additional information or clarification.
Moreover, standardizing equipment can simplify operation and maintenance for asset owners. By using a consistent set of components across multiple projects, they can streamline their maintenance processes and reduce the need for specialized training. What’s more, you’re likely to form strong relationships with your suppliers of choice, meaning that if a part fails or you need to order more equipment, there’s a better chance you have a replacement on hand or know exactly who to call to get it. All of this can lead to lower operational costs and improved system reliability over the lifetime of your DG project.
But, it’s important to remember that standardization does not mean sacrificing flexibility. While it can help speed up the processes involved in getting your project online, developers must remain openminded and committed to using the right components that best suit specific site requirements and energy needs, even if it means changing or introducing new equipment. Finding this balance of standardization and adaptability is key to ensuring successful project outcomes.
2. Lean on proven components
No developer is trying to incorporate unreliable parts in their DG projects, and some of the most significant technological innovations have come from start-ups and market disruptors.
But one of the most important things you can do during the design process is to do your due diligence on the equipment you are selecting and prioritize components from reputable manufacturers that have gone through rigorous testing. Given the amount of competition with procurement, which can depend a lot on your firm’s scale, it may be easier said than done, but doing this when feasible will go a long way. By selecting components from manufacturers that are producing high quality equipment withstanding the rigors of long-term operation, you can reduce the risk of failures, warranty issues, and other problems that lead to costly delays and repairs.
Third-party consultants such as Clean Energy Associates (CEA) or Black & Veatch can help you evaluate the quality and reliability of different components you may not have had enough experience with by providing valuable insight based on their experience and industry knowledge.
If you have the scale and time, you can consider implementing pilot periods for new equipment to assess its performance in real-world conditions. By testing new components on a limited scale before deploying them widely, you can identify potential issues and make adjustments to ensure they perform as intended.
Partners such as EPCs, local electricians or other third-party contractors to help with development may have their own preferences on system design and equipment. If a partner isn’t familiar with your choice in equipment, don’t be afraid to educate them on why it will work best for your project, how it should be implemented, and the success you’ve had with it in the past. This avoids the introduction of new components that a developer may not have experience with or the confidence in how it will perform with your designed system.
3. Optimize project designs
Ultimately, nothing you do in your DG project’s design, development or construction phases matters if the utility doesn’t grant you permission to operate. Why not make it as easy as possible to get the thumbs-up?
Tailoring your project to the utility’s requirements from the outset minimizes the need for design revisions and reduces the likelihood of delays in the approval process. Gain a thorough understanding of each utility’s specific requests, including its preferred document formats, technical specifications, and procedural quirks. By providing paperwork and diagrams that adhere precisely to these requirements, you can demonstrate attention to detail and commitment to meeting the utility’s standards.
In some cases, you can also minimize the utility’s involvement in project execution by taking on trenching, cabling and telemetry yourself, and by conducting thorough testing of your equipment, which can identify problems before you submit the project for approval.
One benefit of this approach is that it fosters a more collaborative relationship with the utility and can lead to getting additional DG projects off the ground when you return to the area.
Driving the clean energy transition
Developers play a crucial role in driving interconnection reform. By enhancing the chances of expedited approval for your project with standardized, reputable components, you’re already creating a more streamlined interconnection process, fostering valuable relationships with manufacturers and utilities, and driving solar adoption.
At the end of the day, following these best practices can help scale the much-needed deployment, bring clean energy access to more communities, and help us get closer to our net zero goals.
Eric Lorenz is VP of project engineering — direct/RFP for DSD Renewables.
Comments are closed here.