Mounting with butyl rubber: How Roof Tech gets a leak-proof seal
Butyl rubber was first developed in the early 1930s, and its traditional applications are pool linings, flexible flashing for construction and lining tubeless tires. It has a unique combination of barrier properties, such as high damping, resistance to ozone, weatherproofing and heat aging that make it an ideal choice for many construction applications.
For instance, butyl rubber is commonly added to asphalt compositions in the manufacturing of roofing materials to improve the weatherproofing and low-temperature properties of the asphalt.
Butyl rubber is the secret sauce Roof Tech uses to seal each attachment point in the rooftop mounting system that the company is now bringing to the United States after perfecting the system on more than 400,000 residences in Japan the past 18 years.
The weather test
No matter how the attachment of a PV array is achieved, the ultimate sealing point is exactly at the penetration in the roofing paper where a lag or fastener gets attached to the frame or roof sheathing, typically with sealants. Sealants usually have a maximum service temperature in the 160- to 200-degree F range, whereas RT butyl performs at 248 degrees F, providing more protection under heat distress.
Milton Nogueira Jr., senior business development manager for Roof Tech, says its RT butyl flashing provides tested impermeability and elasticity; it is easy to mold yet is highly resistant to punctures. Butyl tape allows for expansion and contraction, even with extreme fluctuations in temperature, while preventing moisture from passing through. It has a minimum effective life of 20 years and is resistant to aging from weather, mildew, acids, alkalis and salts.
At the laboratory, Roof Tech tested complete roofing sets under extreme conditions of constant UV light, 145.4-degree F temperature, 50 percent humidity and a water spray every two hours. The specimens were monitored throughout the testing time and were evaluated at 7,500 hours (almost one year later). RT butyl tape was still flexible and performing its job.
Roof Tech has just one of many great systems featured in our 2015 Mounting Showcase
The full system
The code states that roof-mounted PV system flashings must be installed in a manner that prevents moisture from entering penetrations through the roof plane. The current suggested guideline by the National Roofing Contractor Association for the installation of a PV system on a steep slope asphalt shingle roof — in terms of the flashing of the PV system stanchions — is that the metal flange should be applied underneath the roofing paper (under the upper underlayment) to achieve the proper water shedding. Nogueira says such a step can only be accomplished along with the installation of a new roofing system, and this can’t be done on a retrofit of a PV system installed above an existing roof, which is the majority of installations in the United States.
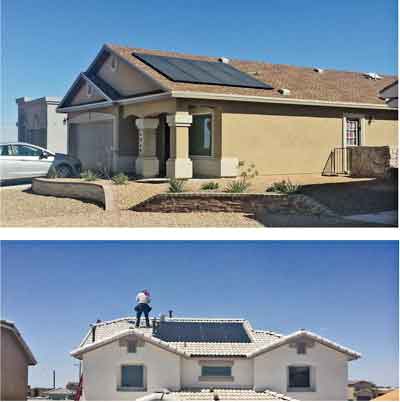
Top photo: This array installation could normally take two hours with a rail-based system, but with RT-[E] Mount, the time dropped to 40 minutes. (Photos courtesy Border Solar)
Bottom photo: A recent Border Solar installation in Southern Texas where RT-[E] Mount is placed on a Tile Roof with an asphalt roofing system installed underneath the array.
The Center for Environmental Innovation in Roofing does not recommend water shedding flashings on the roof where there is potential ice damming, such as eaves or overhangs and all around the PV array. Waterproof flashings are recommended in areas where ice damming may occur.
The other issue with installing metal flashing between roofing shingles that needs further examination, according to Nogueira: the effect on the warranty of the roofing material itself. The separation of the shingles can be treated as a failure to seal the roof (blow-offs), which could drastically reduce the warranty from the roofing manufacturer. For instance, the warranty for a GAF roofing product was reduced from a 50-year down to a 15-year because of the failure to seal. Nogueira says the roofing manufacturer will become more involved as far as recommendation for the installation of PV systems on top of their roofing products based on future codes yet to be adopted.
The RT-[E] Mount is supplied with the RT butyl tape flashing, and the company claims 100 percent waterproofing on low and steep slope asphalt roofing applications while still fully complying with code requirements.
In fact, Roof Tech says it has the only rail-less PV mounting system with integrated flexible flashing certified by the ICC. It is fastened with 5-mm stainless steel screws, so there is no need for a pilot hole and, by code, the area for attaching to the rafter is wider than when compared to the usual 8-mm lag bolt. This allows the installer to easily meet code without the risk of splitting a rafter.
In addition to the butyl tape, each PV module is secured with multiple fasteners to spread the mechanical load evenly throughout the roof surface and, more important, to alleviate the torsion applied to a roofing system due to thermal stresses. Nogueira says the thermal contraction and expansion of an array that is built mostly with aluminum with a high coefficient of thermal expansion will have the most movement on top of a roof.
The Roof Tech design, with a module frame, has mitigated the effects with a minimum distance between adjacent rows that can be as low as 3 mm (1/8 in.). Mid and end clamps are 4-in. wide for the purpose of distributing the clamping pressure on a larger surface of the PV panel frame.
Be sure to scroll the rest of our mounting article archives
I have personally been using Butyl rubberfor all my exterior sealing solutions, especially around the roof area, and gutter areas. The brand I prefer is OSI, comes in many colors, sold here in the States for many years.