Solar Stress Test: Reliability gaps widen in latest PV module testing
Solar modules are cranking out more Watts than ever, but reliability is decreasing. New data from Kiwa PVEL and RETC / VDE Americas show alarming upticks in test failures — not from extreme weather, but from everyday materials and design flaws. As PV manufacturers race to cut costs and push performance, solar pros are grappling with a tough new reality: Today’s PV modules are more powerful, but more fragile.
Here are the good and bad takeaways that jumped out at me in these mid-year module and solar risk reports.
Good: Hail-hardened modules are working
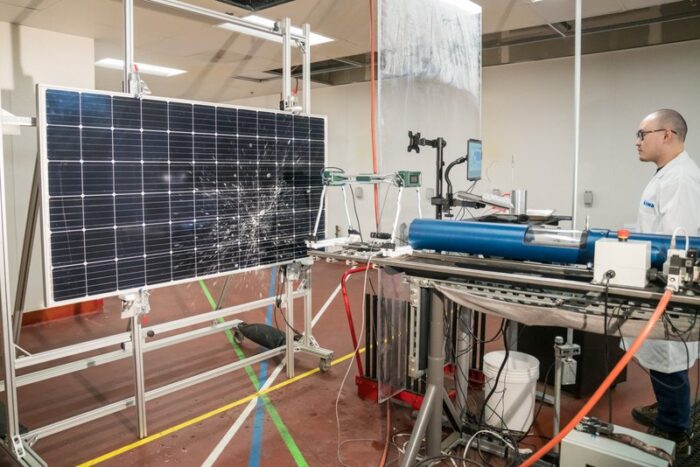
Hail damage has spooked the solar industry. In a review of claims data, climate insurance provider kWh Analytics has estimated that hail accounts for 6% of solar project insurance claims but more than 72% of losses by dollar amount. Moreover, hail-related solar project losses incurred since 2018 have exceeded $600 million—in the state of Texas alone.
But there is good news here: In its 11th annual PV Module Reliability Scorecard, independent solar module testing lab Kiwa PVEL noted that hail-hardened modules tested great. The Scorecard relays key information from the Kiwa PVEL Product Qualification Program (PQP) reliability and performance tests. Some stats regarding hail-hardened module testing:
- The past year of testing continued to prove that 3.2 mm glass//backsheet modules and hail-hardened designs are significantly less susceptible to glass breakage than 2.0 mm glass//2.0 mm glass modules.
- The first BOMs of hail-hardened modules made with either 2.5 mm glass//2.5 mm glass or 3.2 mm glass//2.0 mm glass have achieved lower glass breakage rates than both 3.2 mm glass//backsheet and 2.0 mm glass//2.0 mm glass.
- The Top Performers in this category highlights modules resistant to glass breakage for 40 mm hail and greater.
- There was no post-hail impact power degradation > 2% in the 2025 Scorecard dataset. Current module designs suffer relatively little hail-induced power loss due to the use of half-cut, multi-bus bar (MBB) cells.
Further, solar tracker hail stow strategies are also proving to mitigate risks of hail. Here is Jon Previtali, Senior Principal Engineer – VDE Americas, explaining a recent study, sourced from kWh Analytics’ 2025 Risk Report:
VDE Americas interviewed project operators to understand the outcomes. Site A stowed to the nearest extreme angle (likely west) and defended against radar-estimated 40–50 mm hailstones without damage. Site B, under construction and already in hail stow (likely east), was hit by radar estimated 50–75 mm hailstones with no damage. Site C went into hail stow and was hit by radar-estimated 75-100 mm hailstones, suffering only minor damage due to flying debris and a known tracker motor issue that prevented one set of rows from stowing properly. The hail damage at Site C helps prove that hail stow worked—unstowed modules sustained hail damage, while stowed modules did not. All hail stow angles were 52° and all projects have 2.0-mm/2.0-mm dual glass panels.
Bad: Risks abound everywhere else
The number that jumps off the page in the Kiwa PVEL 2025 Scorecard: 83% of module manufacturers had at least one test failure, up from 66% reported in the 2024 Scorecard, which at the time was the highest percentage ever reported. Module breakage during mechanical stress testing and hail stress sequence was the leading failure type, but delamination, power loss, and junction box related issues also persist.
Likewise, RETC released a preliminary version of its PV Module Index Report that echoes the same sentiment:
“Recent testing has also shown how novel technologies tend to degrade in novel ways, revealing evidence of structural deficiencies, such as PV module frame and glass failures during mechanical loading, cyclical loading, and ballistic-impact testing. These red-flag results serve as a reminder that industry stakeholders must remain vigilant regarding the technical risks inherent in an accelerated pace of change and the short time frames between innovation and mass production.”
There is no silver bullet when you scan the results. In the Kiwa PVEL Scorecard, only 21 model types achieved Top Performer status in all reliability tests, and of those, only three models were also Top Performers in PAN. So, it pays to know the most likely points of failure or typical causes of degradation for every module type, bill of materials (BOM), and PV brand you’re considering …
Breakages and degradation: The failure modes multiplying in the field
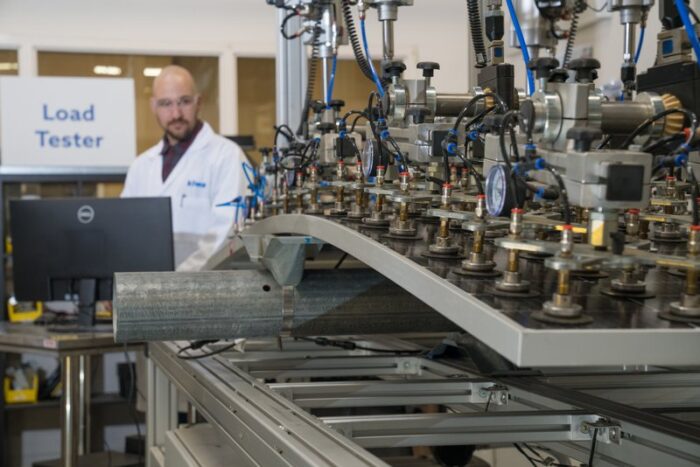
Mechanical stress test and module breakage: 20% of BOMs experienced one or more failures during MSS testing. The BOM-level failure rate increased from just 7% in the 2023 and 2024 Scorecards. 40% of manufacturers experienced at least one failure during MSS testing, all but two of which were due to glass breakage and/or frame damage.
Glass//glass modules experiencing spontaneous glass breakage is the most significant reliability issue affecting today’s PV modules. Kiwa PVEL is aware of it occurring in multiple countries, with multiple module model types, mounted to multiple tracker/racking solutions.
“There’s no single reason,” says Tristan Erion-Lorico, VP of Sales and Marketing, Kiwa PVEL. “The glass isn’t as strong. There might be flaws in the glass. There’s weaker frame designs. There are more aggressive mounting methods. There can be direct contact between the glass and the frame.”
Erion-Lorico explains a failure Kiwa PVEL is seeing more and more that is leading to breakage, involving how silicone cups the module frame:
“We’ve done cross sections of modules that broke in the field and we see the silicone isn’t cupping the glass. Now, it’s the same volume of silicone used in previous modules, but you’ll see it’s not making its way around the glass,” he says. “We’re also seeing breakage due to the walls of the frame getting thinner. Or the flange along the bottom of the frame is getting narrower.”
But even that lack of silicone in the right spots along the frame wouldn’t cause a catastrophic break. “If the module’s bigger, and the glass isn’t fully tempered safety glass, and there are flaws in the edge of the glass, add all of those things up and that’s leading to breakage.”
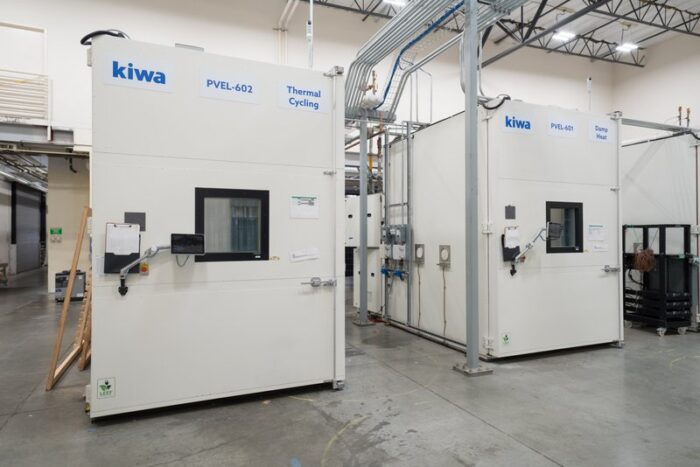
Damp heat test: Both TOPCon and HJT cells are more susceptible to moisture-related corrosion than PERC, as has been observed in some damp heat test results over the past few years. “The median power degradation for TOPCon glass//glass BOMs tested over the past year was 1.6% compared to 4.0% for TOPCon glass//backsheet BOMs. While this is encouraging for glass//glass TOPCon BOMs, 9% of manufacturers experienced delamination failures along the edges of their glass//glass modules following DH testing, emphasizing the importance of proper lamination.”
Thermal cycling test: 32% of manufacturers experienced at least one failure during the thermal cycling testing, which was up from 20% for the 2024 Scorecard. 71% of BOMs tested degraded by less than 2%, which is down from 83% in 2023. For the 2025 Scorecard dataset, 90% of all glass//glass BOMs tested had < 2% degradation following the thermal cycling test versus 0% of glass//backsheet BOMs.
New finding: Modules degrade just sitting in the dark.
Modules are susceptible to seasonal affective disorder. Or as Kiwa PVEL calls it: Dark storage degradation, an issue they’ve uncovered recently.
“After UV induced degradation testing a module had degraded by 4.5%. And then it was left in a dark room for a month. We flashed it again, and it’s had degraded to 8.9%. That is new. You’d think it would be stable sitting in a dark room.”
The good news is this mostly impacts testing. Light soak restored the module to 4.3% degradation. So, installing that module, and exposing it to the sun, reverses the dark storage effect. However, the baseline UV induced degradation effect still generally concerns Erion-Lorico.
“Sure, it’s not the 9% degradation after dark storage, but it’s also not zero. The module had already degraded 4.5%. And then we went through this month in the dark, and we did our light soaking to bring it back up close to the original degradation amount, but it’s still sensitive to UV exposure.”
Underlying issues for PV module risks in 2025
Underlying issue 1: TOPCon and HJT modules are more temperamental
Solar modules today are capable of greater power production than ever, thanks to the move to n-type solar cells — TOPCon and heterojunction (HJT) – from p-type cells (PERC). The catch is these cells really do require the other module components and production process to be dialed in.
“We’re finding the choice of materials is more critical than it was previously,” Erion-Lorico says. “Your choice of materials — the encapsulant you’re using, the metallization on the cell — all of those chemistries inside the module are becoming more critical. If you select the right material and do a proper job laminating that, you can take advantage of the increased performance and increased energy yield of these newer n-type module designs.”
Swapping out just one supplier in the BOM could dramatically change the performance of the entire module – and BOM changes are occurring more often.
Example: TOPCon and HJT cells are more susceptible to corrosion caused by moisture, which leads to power loss. Sure enough, in the last three years, Kiwa PVEL has noted more corrosion related power losses.
“Moisture goes through the backsheet into the encapsulant. The encapsulant gets saturated and then you see corrosion starting all around the perimeter of the cell,” Erion-Lorico says.
Underlying issue 2: The pennies per Watt battle
The real root cause underlying much of the increase in failures and breakage is most module manufacturers are losing money on every module they sell, particularly outside of the US and India. They need to find ways to cut costs and they are doing so with other module components, even though the choice of glass, encapsulant, cell metallization, flux and backsheet is more critical than ever.
The competitive bid-price project economics do not help matters. EPCs could pay a premium for the perfect BOM for every site – but will they win a competitive bid for that project?
Conclusion: Application is everything
Kiwa PVEL and RETC reports highlight everyday general problems, and they both highlight the importance of third-party inspections and site specific module selection. Parsing through the data shows that each module type is susceptible to something different.
“Laboratory testing data clearly show that some PV modules are more resilient to severe hail impacts, for example, whereas other products are more vulnerable. At the same time, products that test well for hail durability may be at an elevated risk of degradation when installed in a hot, humid location,” notes Cherif Kedir, RETC’s president and CEO.
PV modules are doing more with less, but they’re also being asked to last longer in more demanding environments. Some are spontaneously breaking for no immediately discernable reason. The solar industry is rightly focused on resilience on catastrophic losses—from hail hardening to tracker stow strategies—and that focus is being rewarded with products and strategies that lower risk. But while you’re defending against acts of God, don’t overlook the everyday best practices.