Solar module glass is ‘spontaneously breaking’ in the field
Solar module market news is coming fast and furious these days. PV prices have possibly it a floor. A record-setting 11 GW of that new solar module manufacturing capacity came online during Q1 2024. PVEL has a record number of high performing modules this year. What else, what else … Oh, and solar module glass is “spontaneously breaking” in the field.
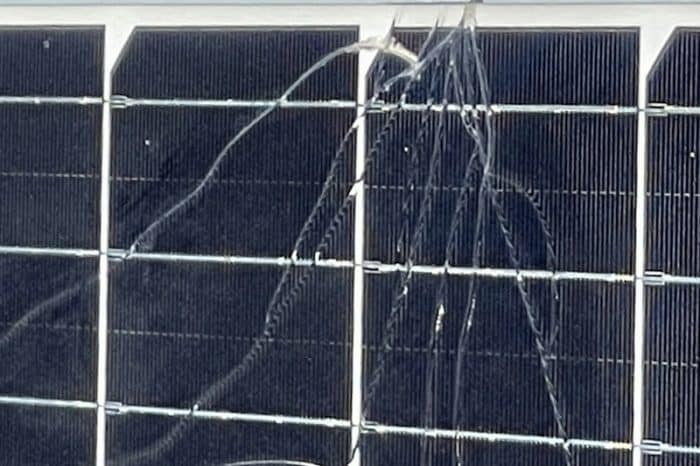
Yes, the sixth annual PV Module Index Report from RETC had some troubling findings, headlined by reports that spontaneous module glass breakage in fielded projects is increasing. That is glass breakage — for no apparent reason — often before commissioning.
“While I have not seen that many impacted sites, a lot of people within the broader community are seeing similar problems,” states Ralf Schulze, who manages field forensics services for RETC. “We know this because NREL and DuraMAT share information regarding field failures relatively quickly. For the few sites I have investigated—which are large utility projects on the order of 100 MW–300 MW in capacity—we are seeing spontaneous glass breakage rates of 2%–5%.”
Doing the most charitable calculation based on that quote, a 2% breakage rate for a 300 MW project would be 6 MWs worth solar panels with glass breakage.
RETC (Renewable Energy Test Center), a member of the VDE Group, is a provider of engineering services and certification testing for renewable energy products. RETC also recently acquired SolarPTL, a photovoltaic testing laboratory based in Tempe, Arizona, with a dedicated outdoor testing facility. This sixth annual report is very good, and the authors interviewed several experts to ascertain why solar glass is breaking so much more in the field.
How rare is module glass breakage?
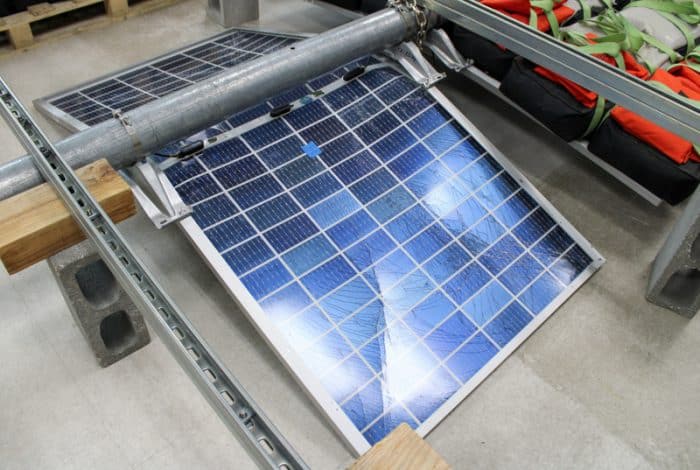
Spontaneous glass breakage is a PV failure that “we didn’t used to see,” according to Teresa Barnes, who manages the Photovoltaic Reliability and System Performance Group at NREL. Glass breakage of this type was historically the result of shoddy O&M work or bad luck (mowers shooting out rocks) or thin-film PV that was not tempered.
Now, “we are regularly hearing about glass breakage in silicon modules.” Barnes acknowledges these reports are anecdotal, but there is also “a definite pattern.”
“It used to be the case that modules would pass the IEC 61215 static load test with a big safety factor. Today, modules are either barely passing the base static load test or they are not passing with higher safety factors. Some new module designs are simply not passing the minimum static load test.”
Module market context
Large-format modules, and concerns about how to support them, are not new. The cover article of our Spring 2020 edition, “Mounting and Cracking” examined the structural durability issues inherent with large-format solar modules. But, as RETC notes in the intro of this report, we all might have understated or misunderstood all of the impacts:
“The early warning efforts documented in our article, ‘Evaluating Large-Format PV Modules,’ are simultaneously prescient and naïve. While we had clearly identified a signal in our laboratory testing and field forensics—namely, structural vulnerabilities associated with newer module designs—we did not necessarily understand the root cause of the issue.”
- Was the physical size of these new modules a problem?
- Was solar market proliferation to blame for subjecting modules to previously unaccounted for environmental stresses?
- Were our testing protocols and sequences inadequate to identify potential new failure modes and wear-out mechanisms?
The question now, in 2024: Is a decline in the compressive strength of solar module glass partly to blame for some of the unique field failure modes associated with new ultra-large-format module designs?
Why is module glass spontaneously breaking?
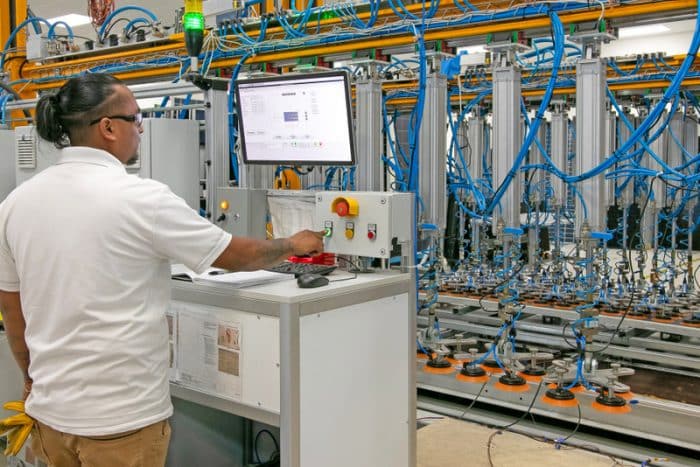
Module manufacturers are using thinner glass, in part, to lessen the load and costs of ultra-large-format PV modules. Thinner glass is more likely to be heat-strengthened instead of tempered, which provides less compressive strength.
This matches up with RETC reports noting a decline in the compressive strength of solar module glass over the years: “In our laboratory testing, RETC has consistently observed that heat-strengthened solar glass is more prone to breakage than fully tempered solar glass. Unfortunately, we now suspect this vulnerability may also apply to field deployments.”
These ultra large-format modules also have thinner frames. As a result, this thinner module glass is likely bearing even more load than it would have previously. Not a great combination!
Any other theories?
Short rails also play a part in module glass breakage. Too short for the wind load and modules can bend in the wind, causing the glass to crack.
“Another theory is that glass is breaking due to manufacturing defects, which could be inclusions, particles of pollutants in the glass, or other manufacturing process problems,” says Jon Previtali, a technical due diligence specialist at advisory firm VDE Americas. “Glass breakage could also be a construction issue, such as module clamps being torqued down with too much force during installation.”
Who is most impacted by spontaneous glass breakage?
Whatever the reason, fairly or unfairly, this module glass breakage issues impact the EPC or project owner most — whoever builds the project and then wants to transfer it to a final owner.
“If glass breakage is documented during the commissioning and handover process, it leads to bigger questions,” Schulze notes. “People will ask, ‘If spontaneous glass breakage is happening to some modules now, won’t it happen to the other modules, too?’”
Solutions?
If heat-strengthened solar glass is the new normal, the good news is it can be chemically tempered, according to James Webb, a senior research manager for reliability sciences at Corning, a glass manufacturer. The bad news, is it sounds more expensive:
“While this is an effective process for producing glass with an impressive strength profile, a cost-benefit analysis is required to determine its suitability for solar applications. Thermal tempering provides a good equilibrium between cost and strength.”
Another option to add strength to heat strengthened glass on a solar module, is “for manufacturers to maximize glass strength by considering panel, process, and system design strategies that lower glass stress, improve handling, and reduce strength-limiting damage,” Webb says.
RETC says “the pendulum in that balancing act may already be swinging back toward the integrity of the frame and the mounting rail.”
To protect your project, Previtali recommends asking the engineer of record and an independent engineer to check the length of the rails necessary to support the procured PV modules.
“We often see letters from PV module manufacturers confirming that rails are long enough, but without providing any supporting calculations,” Previtali says.
Other takeaways in the RETC report:
- Some new PV cell technologies are susceptible to ultraviolet-induced degradation (UVID). Alarmingly, 40% of test samples returned red-flag results in the UVID test sequence, indicating that these products may not be able to meet manufacturer warranty terms. We observed 10%–16% degradation in some mass-produced, commercially available PV modules. Without immediate and collective action, UVID has the potential to become a major reliability issue for solar industry stakeholders.
- 75% more test samples returned a red-flag result (14% of models) compared to overall highest achiever results (8% of models). 8% of models tested met RETC’s rigorous standard for recognition as an “Overall Highest Achiever,” whereas 14% of models tested showed some sort of red flag. Without beyond-certification test data, buyers are more likely to procure modules that test poorly in one or more reliability or performance sequences than modules that excel across multiple disciplines.
Comments are closed here.