Q: How can I best prepare for solar wire management supply chain issues?
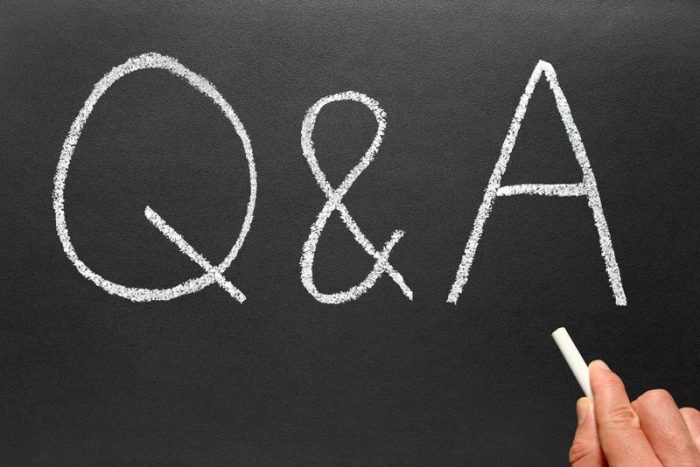
As part of our 2022 eBOS Buyer’s Guide, we asked manufacturers, given the recent supply chain issues, what should solar contractors and EPCs being doing now with their procurement planning to best prepare for and overcome future obstacles?
Planning ahead
Nick Korth, market development manager, HellermannTyton: “Plan ahead as much as possible. Forecasting details, delivery schedules, and flexibility are all key to moving through the unprecedented issues that we as an industry and manufacturers have been seeing the last 12 months. Having a domestic supply chain has helped HellermannTyton weather a lot of issues, but we are still dependent on vendors for raw materials and shipping partners to get those parts to our customers. In today’s supply chain, there are just so many more variables that can lead to delays.
Sarah Parsons, Hubbell (Wiley): The best way to ensure the wire management solution you want is available when you need it is to plan ahead and order materials a minimum of four months in advance if you can. Because wire management is one of the last steps ordering it is often left to a later point in the project. This could limit your options and leave you with solutions that may not be optimal for you or your customer. Ordering early gives suppliers more lead time to secure raw materials and produce finished goods. It provides a buffer for potential delays in production and transportation – either of which could be caused by any number of factors including labor shortages, inclement weather, and other unpredictable environmental events.
Consider ‘sustainable logisitics’
Mike Wiener, marketing manager, QuickBOLT: “Our best advice to contend with today’s supply chain climate would be to remain transparent in communications. Most businesses understand how it is right now and that logistics beyond our control play a large part in any delays experienced. You’d have to be living under a rock to not know that. Aside from that we recommend looking at your systems in place, how can you improve them so that sustainable logistics exist in harmony with each other? Could you improve your product designs so that they lend to easier fulfillment? We design QuickBOLT products with that intent in mind so that there are fewer obstacles getting them from the factories to installation sites. Solar installers benefit from straightforward solutions in more than just the installation process that way.”
Standardize this!
Tom Marsden, global market manager, renewables, Heyco: “Not only is it a lot easier to procure 100,000 pieces of the same item from one supplier compared to procuring 10,000 pieces of 10 items from multiple suppliers, but a lot of times there are deep volume discounts available (even for wire management which adds up quickly). These discounts are often not realized since a distributor may only be sourcing product for 1 specific project.
If you have multiple projects in the pipeline that can utilize the same components, ask your distributor about a VMI program or Blanket Order. Not only does this open doors to volume discounts, but it also saves in overnight/2nd day freight shipments since inventory can be local to the jobsite at a distributor’s warehouse where a Ground shipment or even will-call is available versus being at a supplier’s warehouse halfway across the country (or in often cases, in another country).
May go without saying, but whenever possible, specify/source products that are made locally to you – many of the supply chain issues are related to containers being held up in customs or not enough containers being available for shipments. What you may save in piece price you’ll quickly lose in liquidated damages for late material or shipping product via air that should have shipped via Ground.”
Comments are closed here.