Non-lithium R&D leads recent U.S. battery supply chain announcements
The U.S. battery energy storage system (BESS) supply chain continues to grow slowly but surely — both lithium-ion battery production and next-generation, non-lithium battery innovation. Here’s all of the latest intel on new manufacturing lines, R&D labs, and recycling facilities in some phase of development headed into 2025.
Eos Energy and FlexGen partner on zinc-based LDES
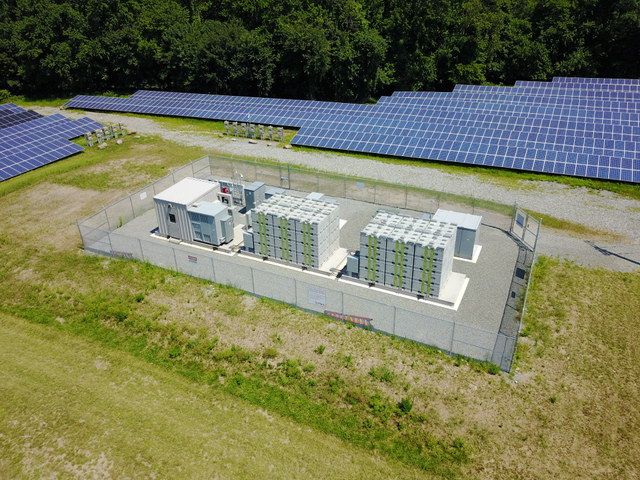
Eos Energy Enterprises is set to manufacturer zinc-based long duration energy storage (LDES) systems in the United States, and FlexGen Power Systems has signed a joint development agreement to commercialize a fully integrated BESS solution for the U.S. market.
Eos’ Z3 batteries will be combined with a domestic inverter and transformer package as well as FlexGen’s HybridOSEnergy Management System (EMS). Eos’ Znyth aqueous zinc battery was designed to overcome the limitations of conventional lithium-ion technology in 3 to 12-hour applications. Via its EMS and Lifecycle service team, FlexGen manages a rapidly growing fleet of energy storage assets for investor-owned utilities, municipal and cooperative utilities, and Independent Power Producers.
“This partnership not only strengthens our go-to-market strategy, but also positions us to deliver an American-made battery storage solution critical to securing America’s energy independence and national security,” said Justin Vagnozzi, Senior Vice President of Global Sales at Eos Energy.
EnerVenue metal-hydrogen batteries in action
Dispatches from the Energy Transition focused on long-duration energy storage (LDES) in December, looking at a use case for EnerVenue’s Energy Storage Vessels, which enable installations in areas never considered before for C&I energy storage projects — including building-integrated storage. Watch the full episode here, or skip to a section below.
- 01:54 – Guest Introductions
- 04:12 – Storlytics Overview
- 13:00 – EnerVenue Overview
- 16:20 – About LDES
- 19:50 – Metal-Hydrogen Overview
- 22:22 – Project Development
- 25:12 – Vessel Characteristics and Modeling
- 28:25 – EnerVenue Markets
- 30:09 – Battery Fire Safety for Hydrogen Batteries
- 40:00 – Applications
- 46:30 – Data Centers / C&I scale applications
- 53:40 – Flexible / LDES Application – Industrial Microgrids
- 57:06 – Key Takeaways
- 59:25 – Guest Information
Argonne leads sodium-ion battery push
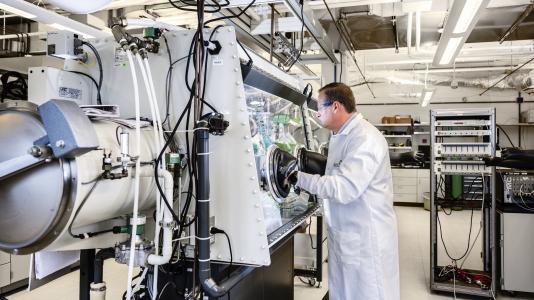
The U.S. Department of Energy (DOE) has awarded $50 million over the next five years to establish the Low-cost Earth-abundant Na-ion Storage (LENS) Consortium. Led by DOE’s Argonne National Laboratory, the LENS Consortium aims to develop sodium-ion batteries in part to reduce the country’s dependence on lithium-ion batteries (and the need for lithium, cobalt and nickel) in the coming decades.
Sodium, in contrast to lithium, cobalt and nickel, is an abundant element, and the U.S. is particularly well-suited to supply both the raw materials and innovation for sodium-ion technology. However, sodium-ion batteries store less energy per unit weight and volume, which results in a lower driving range — a stumbling block to such batteries competing with lithium-ion batteries.
The LENS Consortium is part of a growing portfolio within DOE to innovate sodium-ion batteries, including research into the use of this emerging chemistry in electric vehicle and grid storage applications.
Peak Energy engineering sodium-ion battery cells at new center
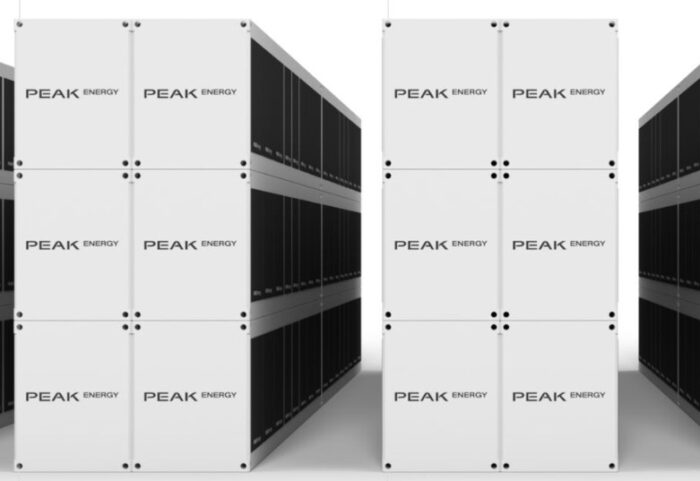
Speaking of sodium-ion, Peak Energy has plans to bring sodium-ion batteries to scale. The company announced the opening of a battery cell engineering center in Broomfield, Colo. – a step toward the company’s goal of creating a domestic battery supply chain by 2030. At present, the U.S. does not manufacture sodium-ion battery components domestically, and this investment is a key step in creating that industry.
Partnering with suppliers across the ecosystem, Peak will begin domestic sodium-ion battery cell manufacturing by 2027 and plans for a domestic supply chain by 2030. The facility is expected to be fully functional this month and will bring nearly two dozen high-paying clean energy jobs to the Denver area by the end of 2025.
This news comes on the heels of Peak Energy’s $55M Series A round, announced in July 2024. In 2025, Peak is planning to deploy its full-scale, grid attached sodium-ion battery systems for evaluation by top utility and Independent Power Producers as part of the Peak Pilot Program.
Lion Energy eyes high-volume battery production in 2026
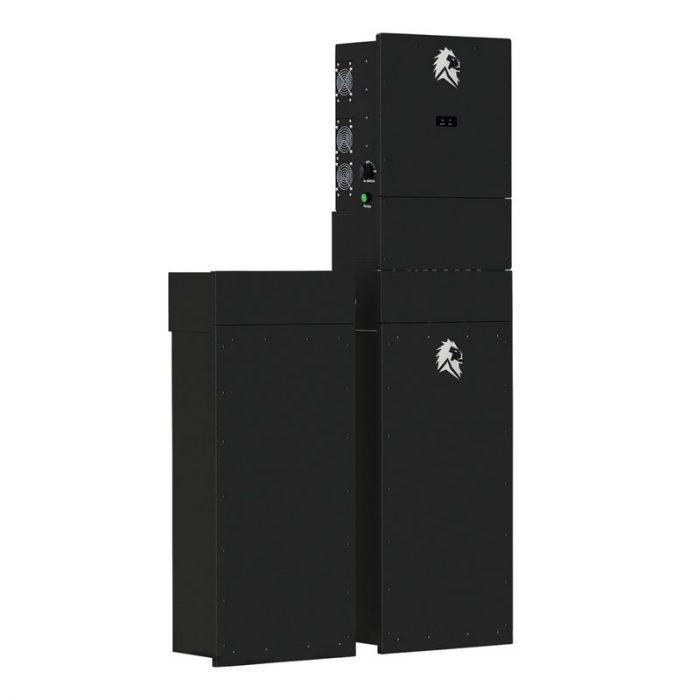
Lion Energy is developing a cutting-edge manufacturing line at its Utah facility for battery rack modules (BRM) and large energy storage cabinet assembly. The manual line will be built first at Lion Energy’s headquarters in American Fork, Utah and will take up approximately 1300 square feet and produce around 200 BRM units per year.
The manual line will be used as a proof of concept for a high-volume production line estimated to produce 2,000 MWh of monthly energy storage by 2026, with additional lines planned for American Battery Factory’s (ABF) Tucson, AZ facility.
The Utah-based line will enable Lion Energy to produce BRM, a 50V lithium iron phosphate (LFP) battery pack that will be sold by the company and can be used in a wide range of energy storage systems, such as the Lion Sanctuary and Lion POWERsave units for residential and commercial applications. Once the infrastructure is established, the company anticipates producing more than 18,000 BRM units by 2026.
“Our partnerships with Lyric and ABF give us access to the battery cells and equipment needed to be successful in the seamless production of our energy storage systems as we strive to make energy independence a reality for everyone,” said Tyler Hortin, president and CEO of Lion Energy.
Nth Cycle first in U.S. to produce premium nickel cobalt MPH
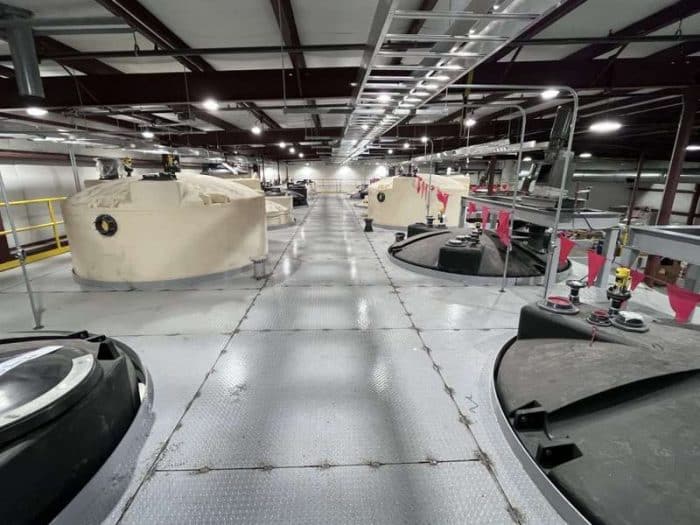
Critical metal refining company Nth Cycle became the first company in the United States to produce premium nickel cobalt MHP – a mandatory component for multiple clean-energy, consumer and defense markets. Nth Cycle has headquarters in Burlington, Mass.
In less than 12 months, the company installed and operationalized its Oyster system at an existing 20,000-sq-ft facility in Ohio to process black-mass and other nickel scrap, commemorating the launch in September 2024.
Unlike other refining methods – both overseas and domestic – Nth Cycle’s Oyster can co-locate with recyclers, manufacturers, and miners on-site, eliminating the years of permitting and billions of dollars needed to build a stand-alone refining plant, while dramatically reducing transportation, time-to-market, cost, emissions and waste. With Nth Cycle’s patented electro-extraction technology, the Oyster, converts recyclable industrial waste and mined ore into the full spectrum of critical metals using electricity – not fossil fuels.
Commercial lithium battery recycling in South Carolina
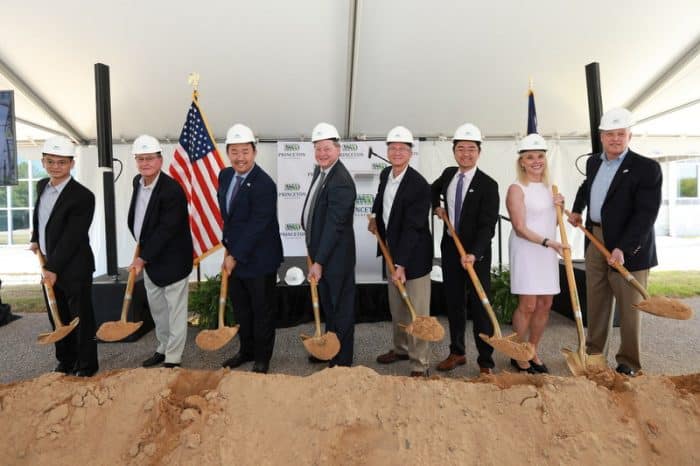
The long-sought solution for economically recycling lithium batteries at commercial scale finally is being built out in Chester, South Carolina, by Princeton NuEnergy (PNE), heralding the latest technology for the task: low-temperature plasma. The $11 million plant will be the first in the nation capable of so-called “direct” recycling of lithium-ion batteries from electric vehicles (EVs), consumer electronics, energy storage batteries and manufacturing scrap.
Upon completion, estimated production will be more than 10,000 tons per annum (TPA) of battery-grade cathode material, the equivalent volume necessary to produce about 100,000 EV batteries per year.
Compared to the existing commercial pyro- and hydro- metallurgical recycling processes — which has not been economic for lithium until now — the PNE process is about 40% less expensive, said Chao Yan, the company founder and CEO, in a recent interview with SB. “Hopefully, by the middle of 2028 we can generate a large volume of high-quality cathode materials out of these waste batteries.”
Comments are closed here.