How FTC Solar built the Voyager+ tracker to address large format module challenge
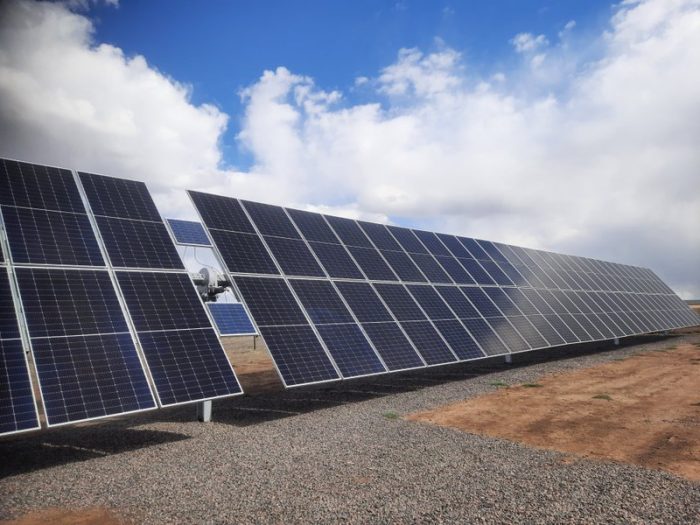
As the solar industry drives toward large format modules, FTC Solar, unveiled the Voyager+, a new 2P-design solar tracker that optimizes energy capture while reducing the manpower and equipment needed for installation. Aimed at utility-scale sites, the company says the tracker’s design enhances energy production levels with 46 percent fewer foundation piles and achieves nearly two percent higher energy density than 1P configurations. Currently, FTC has more than 1GW of Voyager+ installed or under contract.
“As the solar industry moves toward large-format modules of 550 watts or higher, traditional one module in portrait tracking systems have difficulty supporting these new large ‘sails’ while two in portrait designs have already had this experience of scaling to larger surface areas. Because the static and dynamic wind loads are much greater on the structures, with these large formats, there is an ongoing need for improved tracking designs,” said Nagendra Cherukupalli, Chief Technology Officer of FTC Solar. “To answer this call, our team developed Voyager+ to tap into the benefits of 2P designs with proper management of wind loads and the seamless integration of large, complex solar modules – resulting in a zero-stow design.”
Even low wind speeds can be a problem with some 2P tracker designs due to vortex shedding and torsional galloping. To address this, FTC Solar conducted extensive wind tunnel testing and modeling to develop a unique dampener design to deliver a dampening ratio three times higher than traditional systems. Validated by RWDI Tunnel Testing, the tracker utilizes a robust design of wind mitigation long-term reliability.
FTC Solar collaborated with RWDI and Engineered Power Solutions (EPS) on data analysis and wind tunnel testing to independently validate the product’s structural stability. FTC Solar first conducted code-base methods used commonly in engineering to understand static wind forces based on design parameters at the site, wind speed, exposure, and similar factors. Initial sensor-based testing was performed with models of the Voyager 2P system to measure static wind loads and how they affected the structures.
“Utilizing our baseline understanding from the RWDI model test, FTC developed a highly damped system design,” said Matthew Gilliss, CEO, and President of EPS. “By undergoing these tests, their engineering team developed an understanding of common system flaws in design and what preventive measures were necessary to eliminate the risk of aeroelastic instability.”
Currently, FTC Solar has deployed more than 2.5 GW of solar trackers, supported by a global footprint with 31 manufacturing partners in 12 countries.
Comments are closed here.