Adapting solar ground mounts to meet stricter environmental regs, climate challenges
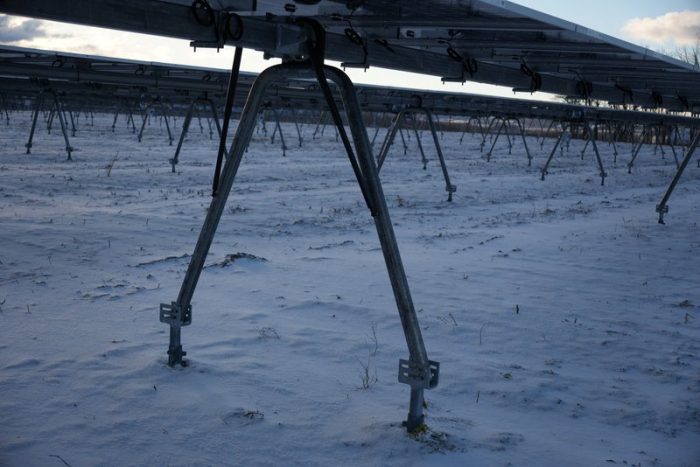
Ground conditions have always been a top challenge for solar engineering, procurement and construction (EPC) teams, but more stringent environmental rules have upped the difficulty levels. Luckily, a variety of solar mounting, racking, and tracker systems are up to solving these site challenges.
Mounting ground challenges
Challenging ground conditions – undulating terrain, rocky or soft soils, etc. – are pretty much a given. With rocky or really hard soils, H pile refusals and remediation are a constant risk. “The remediation options for driven piles can be quite expensive, and they can really impact your schedule quite a bit because the velocity of install is slow,” says Chase Anderson with Terrasmart on an episode of The Pitch.
For the often-overlooked issue of frost heave, ground screws are often a great choice. In Maine, for example, Terrasmart installs a lot of projects with ground screws, which can better handle frost heave forces over time.
“If we were to do those with driven piles, projects probably wouldn’t pencil out,” Anderson says. “The reason ground screws are so successful in handling frost heave is that the surface area is much smaller. I think it’s three or four times less surface area. So, the force itself is already reduced, but the threads always sit below the frost portion of the soil. All of our tension capacity comes from the threaded section, and we’re able to resist those frost heave forces pretty easily.”
Climate considerations for steel
For other sites with material and construction standards, some EPCs are eschewing the typical H-pile or ground screw system altogether with Sollega’s one-piece, injection-molded FR510-6° buckets.Sollega’s FR510-6° is made from BASF Ultramid Nylon 6, which is a non-conductive, UV-resistant material that is durability and inert, meaning it doesn’t leach chemicals or minerals into the ground.
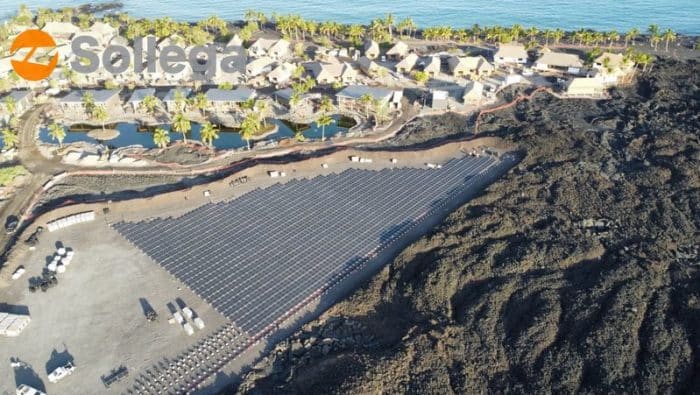
“This ensures compliance with even the most stringent environmental regulations, making Sollega an ideal choice for sensitive or regulated sites,” says Elie Rothschild with Sollega. A lot of Sollega’s traction in ground-mount projects come in areas with high salinity air, which is less kind to steel structures over time than Sollega’s injection-molded plastic.
“We are working on sites that require higher ground cover ratio, ours is twice a conventional pile driven fixed tilt. (35 vrs 72 for our 10dg). We are also working on ground mounts in areas with extreme weather such as Hawaii and the Caribbean.”
Follow the terrain (and stricter environmental rules)
The “reveal window” of an H pile- of ground screw-mounted solar system is important on sites with topographic challenges – that is the range of heights a torque tube is able to sit above the ground on an H pile. Narrow reveal windows can cause problems.
With a ground screw solution, reveal windows aren’t as big of a consideration. Charles Almy from Nextracker explained on an episode of The Pitch.
“We have a much bigger reveal window, which allows us to go over things that we previously couldn’t,” Almy says, specifically of this Ojjo foundations, which Nextracker acquired in June.
A terrain-following tracker design combined with a foundation that leaves a bigger reveal window, is a multiplier. “You can bend the torque tube up to a degree and a half, and you have this 5 foot reveal window,” Almy explains. “It really makes it so you can go over very significant topography without doing any grading at all.”
A big reason ‘terrain-following- is trending is less about the topography and more on project requirements to reduce site grading.
“A lot of BLM [Bureau of Land Management] jobs, it’s starting to be a zero-grading requirement. That’s a really tough thing for an EPC,” Almy says.
A terrain-following tracker may not be sufficient on its own to manage that steep, narrow obstacle. “You may have only a five-foot-wide section that is a wash, and you need to place a pile there in order to maintain your tracker row. To build on BLM land, there are oftentimes requirements to not cut and fill and to leave those washes.”
Some site rules only allow equipment to track over the land a certain amount of times to avoid disturbing the top soil. Here it helps to procure solar mounting solutions that go in the ground without needing pre-drill equipment, or to avoid foundations that are more at risk for remediation.
“Being light on the land and reducing the number of passes across the site alleviates compaction of the topsoil,” says Sol Hutson at Nextracker. “If you’re able to avoid disturbing the topsoil, and able to reduce the compaction impact of having multiple passes, you can a lot of times leave native vegetation ground cover in place know.”
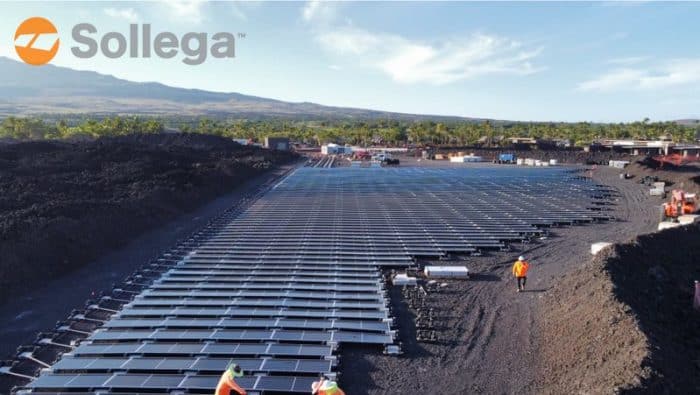
Another constant environmental consideration is dealing with land that is already contaminated in some way. “We are well suited for any brownfield or landfill sites that cannot have ground penetration or heavy equipment driven over it,” Rothschild says.
The modularity of Sollega’s FR510-6° makes it highly adaptable, offering fully ballasted or hybrid configurations that minimize soil penetration while maintaining structural integrity. Deployment is rapid, involves lower cost labor, and can be installed with less heavy equipment tracking over the site.
Comments are closed here.