Ground-Mount Buyer’s Guide 2022: Trackers, fixed tilt
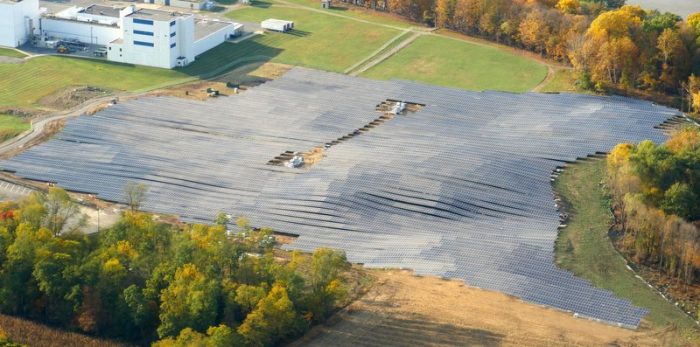
Tough terrain. Sloping sites. Supply chain challenges. Designing and constructing larger scale, ground-mounted solar projects gets more complex each year. Luckily, ground-mount systems are up to the task. In our annual Ground-Mount Buyer’s Guide, we asked manufacturers to tell us what’s new in their offering and for any updated specs in their portfolio. What you’ll see is the market continues to push tolerances and accommodate PV trends, such as larger format and bifacial modules. Many of these companies are also much more than product manufacturers, offering an array of engineering and turnkey construction services. Check out what’s new with the top providers of in the space. Click the product to expand for more info!
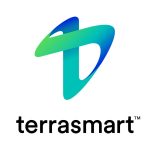
Terrasmart, the renewable energy portfolio of Gibraltar, is a leading provider of solar racking technologies, electrical balance-of-system products, installation services, and project optimization software. Harnessing the combined strengths, technical expertise, and heritage of its four brands, the new Terrasmart delivers a holistic project experience and best-in-class solutions across markets, providing leading solar technologies and smart solutions across the project lifecycle to mitigate risks and amplify returns for solar projects of any size, type, and location. Serving the commercial and utility sectors across North America, Terrasmart integrates products and solutions across the PV lifecycle to minimize risks and maximize returns. With over 19 GWs of solar deployed across 4600 PV systems, Terrasmart creates unique value for more profitable solar on any terrain, anywhere in the U.S.
What’s new in 2022?
In 2022, Terrasmart furthered its integration, harnessing the combined strengths, technical expertise, and heritage of its four legacy brands. Terrasmart now offers its driven pile and ground screw foundations across all of its ground mount products.
Specialties
- Utility-Scale ground mount: 20 – 300 MW
- Single-Axis Tracker: 20 – 100 MW
- Foundation agnostic solutions
Turnkey services
- Design & Engineering: A seasoned team of geotechnical, structural, mechanical, electrical, and civil engineers provides project-specific, value-engineered solutions that will streamline your next ground mount project experience.
- Turnkey Construction: Our full-service construction team can bring all critical aspects of solar construction in-house. One of the most experienced field teams in the industry, specializing in professional surveying, drilling, screw, racking and panel installation. With one of the most experienced field teams in the industry, we have priceless insights that allow us to overcome challenges and streamline processes to ensure projects are completed on time
- Surveying: Site topology & 3D mapping is available via High Precision Aerial Site Mapping. Also, the first of its kind – our Autonomous Precision Survey Rover (APSR) triples the survey speed and accuracy on your next site.
- Manufacturing: Our multiple manufacturing facilities result in shorter lead times and ensure quality, while also allowing for custom solutions.
Products
TerraBOS Flex
Material: Combiner box, wire harness, source circuit
Basics: Complete eBOS solution for sites leveraging the unmatched flexibility of the Home Run architecture. TerraBOS Flex is a full eBOS solution from wire to combiner boxes. All components are pre-fabricated and customized to project specs, making in-field installation faster, easier, and more reliable. Factory assembled for quality control; TerraBOS Flex is customizable at scale.
Key features: Fully integrated and customizable source circuit cabling, harnesses, and DC Combiner Boxes drive high reliability and improved installation vs field fabricated or piecemealed solutions.
- Reduce installation costs with a pre-fabricated solution that allows for fast plug-and-play connections in the field
- Flexible design to work with wire hangers, cable trays, and trenching solutions
- Factory assembled in a quality-controlled environment, ensuring long term reliability
- Diagnose issues at the box level for faster troubleshooting and less downtime
- The use of whips, jumpers, and pre-installed mounting hardware reduces time on site
- Thorough quality process and testing ensures long term reliability
- 8.5+ GW of eBOS deployed across the U.S.
- Our customer focused, value engineered designs save you time and money
Installation explained: The TerrasBOS Flex homerun system can be designed around any site configuration. Its design is adaptable to work with wire hangers, cable trays, and trenching.
GLIDE Agile
Number of pieces: 7 Superstructure Beam Members (above the vertical leg)
Certifications: UL2703, Edition 1; CPP Wind Tunnel Tested
Installation: Our adjustable and durable frame features less hardware, integrated electrical bonding, and included wire management resulting in reduced labor hours. Installation times are shortened by up to 36% through simplified connections, agile parts, and seasoned field teams. Compatible with ground screws that will eliminate refusal risk, increase install efficiency, and make projects more predictable. With one of the most experienced field teams in the industry, we have priceless insights that allow us to overcome challenges and streamline processes to ensure projects are completed on time.
Advantages: With a slope tolerance of 36%, our racking can accommodate high slopes and undulating terrain. Landscape orientation is bifacial compatible to maximize potential backside power yield. Durable mechanics can tolerate wind speeds up to 170 mph and 100 PSF ground snow loads. Our seasoned field team prioritizes accuracy, safety, and efficiency. Foundation consultation from an unbiased partner, based on your unique project site. No matter the terrain or weather, we’ll provide the right solution. Our versatile design enables numerous configurations allowing us to meet your unique needs and bring solar to more fields.
GLIDE Wave
Number of pieces: 7 (1 foundation, 6 racking components & bracket assemblies)
Certifications: UL2703, Wind Tunnel Tested
Installation: Engineered with flexibility in mind, the design incorporates continuous rows to mitigate topographic changes and minimize the number of foundations required. The system can be altered to multiple foundation options, with the base option being driven piers. Proprietary electrical bonding is integrated into the racking system, as well as other solutions for wire management. Pre-assembled parts reduce the number of connections required to be made in the field, minimizing Installation time.
Advantages: The standard engineering of the system is designed to accommodate slopes up to 15%. With several GW deployed across all 50 states, the system is durable and robust enough to accommodate the heavy snow loads in the Northeast, along with the high wind speeds of Hawaii. Our team of professional designers, licensed engineers, and dedicated project management collaborates to ensure projects are delivered in an effective manner and able to operate efficiently. We design each system to site specific environments, helping our partners to maximize the return value on each opportunity.
GLIDE Fuse
Number of pieces: 7 (2 foundations, 5 racking components & bracket assemblies)
Certifications: UL2703, Wind Tunnel Tested
Installation: Designed with a low tilt and clearance, the dual foundation design supports a higher number of PV modules per foundation than standard fixed-tilt systems. The low clearance makes for easier access to assemble components, all of which contain one bolt size. Components are shipped to site pre-assembled, requiring less hours for assembly in the field.
Advantages: For flat sites with low wind and snow loads, this system helps to maximize the PV output with a high ground coverage ratio (GCR). The low tilt and low clearance of the structure reduces row spacing, allowing for more PV modules to be deployed in a given area. The number of racking components is also reduced, reducing the installation time required to assemble the structure. A proprietary design in the components bonds the system, helping make wire management less intrusive.
Carports
Surface lot canopy, Garage canopy
Product description: Terrasmart offers a variety of canopy structures to accommodate any parking surface including longspan, inverted, perimeter and aisle structures. Our structures and foundations are engineered for environmental loading and any subsurface/soil conditions. Accessory options such as water management, snow guards, facia trim, and multiple coating options are available. A big part of our value is our ability to work with our customers on the conceptual design phase to ensure the best possible system is designed for each project and budget.
Construction process: Pre-construction design identifies risk up front for smooth project planning. Smart scheduling and through bolt connections result in less disruptions on site and faster installation time. We’ll work with you to ensure installation is phased in the most efficient way possible.
Differentiator: Terrasmart provides a single source for design, engineering, manufacturing, and installation. With projects covering most of the U.S., we’ve completed projects from Massachusetts to Hawaii. Terrasmart has deployed over 270 MW of canopy systems ranging from 100 kW up to 14.8 MW. With over a decade of projects on the books, we have a long track record of delivering projects at every scale — on time and on budget.
www.terrasmart.com | info@terrasmart.com

AEROCOMPACT – founded in 2014 – designs, engineers, and manufactures flat roof, ground mount, and metal roof solar mounting solutions. Its racking systems are compact, aerodynamic, and easy to install. The company prides itself on its ability to provide intelligent racking solutions for the most challenging site conditions, e.g., with high wind/snow loads, or if required, a highly distributed ballasted ground mount solution for landfill or brownfield projects. Close to 2 GW of power installed with mounting systems from AEROCOMPACT.
What’s new in 2022?
AEROCOMPACT’s proprietary design tool for all of its systems, AeroTOOL, was updated to reflect the latest wind tunnel tests and meets the latest code requirements for many modules. The turnaround time for projects is within 48 hours. AEROCOMPACT supports customers in their permitting efforts to minimize the soft project costs and continue to update our products to meet customer demand.
Products
CompactGROUND G15/G20
Number of pieces: 5 (alternatively with a ballast tray or 18” ground screw)
Tools needed: Universal drill bit & torque wrench (optional impact drill for ground screws)
Certifications: UL2703 (no geotechnical service required)
How does it install: Three Easy Steps: Following our detailed plan, preinstall the clamps, measure the installation area and place brackets and connector brackets. Lay the modules and the ballast for the ground or the ground screws to the recommended sequence. (Optionally cable management).
Advantages:
- No ramming and no heavy machinery
- Ground screws can be installed with a hand drill
- No geotechnical service
- Best ground cover ratio in the market
- Fastest ground mount installation
- 1 MW per truckload
CompactGROUND G10 Plus
Average Row Construction time: Up to 7.5 modules/man-hour (two guys, 4 minutes per module)
Slope Tolerances: Up to 10 degrees without anchors, over 10 degrees possible with earth anchors.
Number of pieces: 5 (alternatively with a ballast tray or 18” ground screw)
Tools needed: Universal drill bit & torque wrench (optional impact drill for ground screws)
Certifications: UL2703 (no geotechnical service required)
How does it install: Three Easy Steps: Following our detailed plan, preinstall the clamps, measure the installation area and place brackets and connector brackets. Lay the modules and the ballast for the ground or the ground screws to the recommended sequence. (Optionally cable management.)
Advantages:
- No ramming and no heavy machinery
- Ground screws can be installed with a hand drill
- No geotechnical service
- Best ground cover ratio in the market
- Fastest Ground mount installation
- 1 MW per truckload
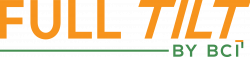
Backed by decades of manufacturing and engineering experience, BCI Engineering’s Full Tilt fixed-tilt system have fewer parts, versatile module loading and fastening methods, and manufacturer-direct pricing. All of Full Tilt’s components are pre-galvanized, roll-formed shapes that bolt together.
Products
FULL TILT by BCI
Number of pieces: 6
Certifications: UL 2703
Average 20-module table construction time: 22 minutes (two-person crew)
Slope Tolerance: Can accommodate up to 21% E-W slope
Installation: The pre-galvanized roll formed sections are lightweight and can be handled by two installers. The rafter features a pivot point near the center of gravity, allowing the structure and loading of the modules in the flat position. Piles are driven with a pile driver, preferably a vibratory type. The balance of the system can be installed by hand with a 2-to-4-person crew using simple hand tools, battery powered tools speed up the assembly. Once the piles are driven and the components are properly staged, a 20-module table can be fully assembled in less-than one man-hour.
Advantages: The Full Tilt system has many cost and labor saving features, and one the installers gravitate towards is the “Longhorn” panel rails that keep the modules perfectly aligned for quick fastening. The assemblers need not waste time adjusting the modules, alignment is automatically perfect. Another big advantage of the Full Tilt system is that it is designed to be built in the flat position. This means that all components can be assembled at a safe working height without need for ladders or workers climbing the structure. After the structure is assembled and panels fastened, the complete structure is easily and safely rotated to final position.
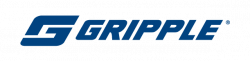
Gripple, a manufacturer of time-saving products for the civil and seismic markets, entered the solar market in 2021 with a few tried and tested solutions to secure new and existing ground-mounted solar arrays. All components are made specifically for outdoor use with a life expectancy of 30+ years in the harshest conditions. Gripple’s Solar Bracing Solutions can be easily retrofitted to any existing system for any remedial work caused by external forces, such as realigning misshapen posts or to stop tables tilting and structures leaning.
What’s new in 2022?
Gripple debuted The CR-System range that includes lightweight above ground cable routing devices that are able to hold 1170 6mm2 of cables and have the potential to be stacked to increase capacity. Manufactured from polycarbonate UV Stabilized corrosion-resistant material, their free-air position can assist at design stage to de-rate and reduce the CSA on cabling used, providing further savings on project costs opposed to traditional trenching.
Products
Power-Tie
Basics: Power-Tie is Gripple's wire cable tie. Engineered for lasting performance, Power-Tie combines the robust strength and endurance of steel banding with the ease of install and versatility of cable ties.
Material: Power-Tie’s wire joiner is manufactured from Zink Alloy and includes corrosion resistant Sintox Ceramic wedges. The wire rope is 316 stainless steel and the cable protection strap is made from HDPE with UV and FR additives. It is tested for -40 to +194 Degrees Fahrenheit (-40 to +90 Celsius) and has been designed to last 20+ years).
Installation: Place the strap over the cables then insert wire rope into the entry channel while holding the cables in place. Pull the wire rope tight until cables are secure and use the retention clips to secure any excess tail wire. Use the Flag Key to release the GripTie allowing for adjustment or re-installation.
Key features
- Simple Install – As easy and fast as a traditional zip tie
- Reduced Replacement Costs – Designed to last 20y+
- Use Anywhere – with 3 size options you can use on any type of structure
- High Strength – Comparable with steel banding and ties giving you confidence to use anywhere
- No Waste – 3 size options with no need to cut excess wire on site
- Safe To Install – Tool free with no RSI risks
CableSmart: Above Ground Cable Management
Gripple’s CableSmart above ground cable routing system is super quick to install, designed to last the lifetime of your site, and helps protect your cables from abrasion and wear. Gripple’s Messenger Kit is the fastest and easiest to install on the market thanks to the Dynamic wire joiner/tensioner. Alongside this, Gripple also supply messenger brackets and a range of hangers featuring side cable loading for easy installation and access. Gripple’s hangers have been specifically designed to protect cables, with a wide surface area to prevent pinch points and abrasion over time. The snap on locking mechanism which attaches hangers to the messenger wire also prevents movement, ensuring hangers and weight remains evenly spaced long term.
Materials: All materials are designed to last 30 years +, and are tested between -40 and +90 degrees Celsius. Hangers are made from UV stabilized Polycarbonate, with the messenger wire made from corrosion-resistant Zinc Aluminum.
Installation: Installation is quick and simple, requiring just hand tools and minimal training. First contractors install the Messenger Kit which can be attached to end posts using eyelet fixings or intermediate ground mount frames using the Messenger Brackets. The Messenger Kit is quick to tension using the Gripple Dynamic tensioner, making the system so much faster than traditional turnbuckles. Once the Messenger Kit is secure, contractors can attach the Hangers at regular intervals along the messenger wire. The Hangers feature a locking side loading gate which makes loading cables easy and O&M access simple.
Solar Ground Anchoring Kits
Material:
- Anchor head: Zinc-Aluminum alloy or Aluminum Alloy
- Wire Rope: Steel (zinc-aluminum coating)
- Dynamic tensioner: Zinc alloy (ZA2)
Basics: Gripple’s game-changing ground anchoring products overcome real world on-site challenges and are ideal for supporting existing foundations and rectifying misaligned structures.
Quick and easy to install using just hand tools, Gripple Ground Anchoring Kits are strong and lightweight, delivering impressive performance up to 2,750 kg | 6,060 lbs. Available in convenient kits for easy handling, Gripple Ground Anchoring Kits deliver savings in terms of on-site logistics and off-site haulage.
Key features:
- High performance - Up to 2,750 kg | 6,060 lbs anchor performance (depending on anchor and soil type)
- Fast and easy - Install in minutes using just hand tools with minimal training
- Versatile - Acts as both primary foundation or as a support to existing piles or ballasts
- Reduced materials - Our products can have a positive impact on your bill of materials vs traditional solar foundations
- Strong and dependable - Developed using corrosion resistant materials to last over 30 years
- Undisruptive - Minimal ground and soil disturbance during and after installation
Installation: Gripple Ground Anchoring Kits are designed to be quickly and easily installed by hand in minutes, ensuring safe and secure installation of solar sites on previously unusable land. Simply drive the anchor into the ground at the desired depth. Next, tighten the wire to apply tension and rotate the anchor head, so the load bearing surface is parallel to the ground surface. The wire is further tightened to compress the soil above the anchor’s bearing surface. This compression transfers towards the surface to form a cone of soil which prevents further anchor movement – adding additional stability and peace of mind.
Solar Bracing Kits
Gripple engineers have developed a lightweight solar frame bracing kit which provides comparable structural performance to heavy traditional steel bracing, at a fraction of the cost. By replacing heavy steel cross sections with strong but lightweight wire rope bracing, you can significantly reduce material, transportation, and logistics costs, as well as embodied CO2. In addition, Gripple bracing kits are fast and simple to install using just hand tools, and are delivered in small boxes making on-site material handling easy compared with lengths of steel and powered machinery.
Material: All components are made specifically for outdoor use with a life expectancy of 30+ years in the harshest conditions. Gripple’s wire rope is coated with corrosion-resistant Zinc Aluminum and can be integrated as part of the frame with custom hot dipped brackets, or looped around existing fixing points. The internal gripping mechanism consists of a sintered ceramic roller offering a superior strength to alternative tension-only bracing systems, with a load rating of up to 3,860 lbs.
Install: The two-way locking device known as a PV Dynamic Tensioner allows you to install a brace quickly and easily between two piles. Applying pre-tension using a fast and unique tensioning tool, the PV Bracing Kit will ensure the frame stays rigid, eliminating misalignment that might occur due to external forces and environmental loads. The ready-to-use kits are fast and lightweight, drastically improving health and safety on-site.
Key feature: Kits come in oversized lengths to allow for greater flexibility in the tolerance of frame installation and to support a greater variety of mounting systems. To aid the installer, the Dynamic Tensioner component is releasable, allowing the product to be adjusted prior to tensioning.
Solar Cable Bridge
Material: DX51D mild steel
Basics: Safely and securely manage string cables over tracker bearings or motors using our easy to install Solar Cable Bridge. Designed for simple, tool-free installation with minimal training, the Gripple Solar Cable Bridge prevents damage to string cables from moving tracker motors or bearings, eliminating costly cable damage and reducing downtime. Offering the ultimate versatility, the Solar Cable Bridge can be used in conjunction with Gripple Power-Tie, which comes with an unrivalled 20-year warranty, or any other standard cable tie.
Key features: Made from durable, corrosion-resistant steel, the Solar Cable Bridge is engineered to last more than 30 years, even in harsh outdoor conditions. Where downtime and site failures due to poor cable management can cost developers hundreds of thousands of dollars every year, this is an invaluable solution.
- Array Technologies Approved fixing strap
- Malleable hand install torque tube fixing strap
- 9.5 in bridge length
- Designed to prevent cable damage and wear
- Hex nut fastening
- Designed for use with Gripple Power-Tie
- 30+ Year design life
- 4.4 lbs working load
- -40°F to +392°F working temperature
Installation explained: Are there racking/tracker partner integrations or brand-specific versions available? If yes, list them: The Solar Cable Bridge can be quickly and easily installed by hand, with the strap being bent around the perimeter of the torque tube and secured with the supplied nut and bolt. The small face of the Solar Cable Bridge is then slid under the strap, positioned over the bearing housing and secured in place by tightening the supplied nut. You can then secure cables as normal using Power-Tie or traditional zip ties, through the helpful slots on the Bridge face, providing an additional layer of cable protection at this key pinch point. Gripple Solar Cable Bridge is approved for integration with Array Technologies tracker systems.
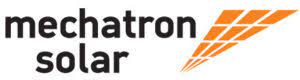
Stockton, Calif.-based Mechatron Solar is an international commercial and industrial solar project developer that manufactures unique, patented dual-axis photovoltaic trackers, each supporting 90 solar panels. The company’s unusually high-yield trackers have the highest energy density and the lowest ground footprint in the industry. Mechatron solar trackers include gearless azimuth trackers and gearless dual-axis trackers, which are designed to maximize performance with a lower operations and maintenance cost than other commercially available tracking systems. They have been successfully tested under different climate conditions rate structures constitute the best available solution for photovoltaic plant installation.
What’s new in 2022?
Mechatron was certified under UL 3703 this year and has a top-tier bankability analysis nearly complete. The flagship tracker also features a new digital guidance system, along with a new optional design with eight columns to accommodate large format modules. The new M16KD agriculture model features extra spacing between vertical panel stacks to permit more light to reach crops beneath the tracker, along with a new table-supported reflector option to enhance bifacial performance. The new M10KD residential model features a reduced table size to support 49 panels, to accommodate limited space requirements.
Products
M16KD Dual-Axis AgriTracker
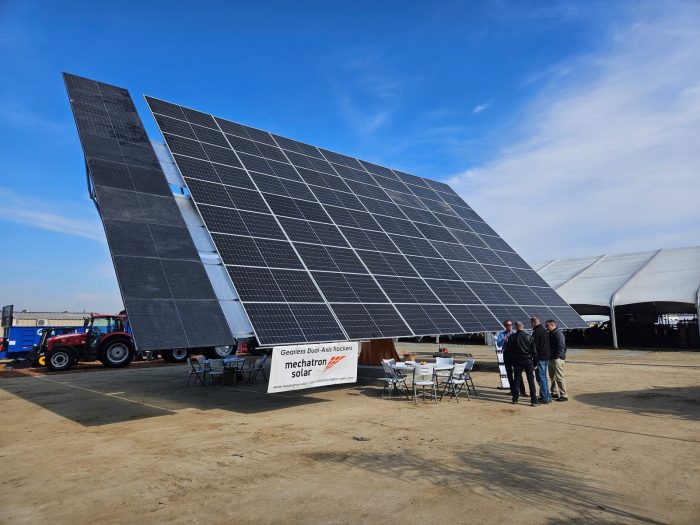
Mechatron Solar’s M16KD at World Ag Expo 24; Credit Chris Weber
The M16KD AgriTracker is manufactured in Stockton, California by Mechatron Solar, that manufactures unique, patented dual-axis photovoltaic trackers. With a ground coverage ratio of 28% to 50% (depending on panel type), the M16KD solution requires only 4 acres per MW of array. The gearless, hydraulic design drives more through 360 degrees of Azimuth rotation and 60 degrees of Zenith inclination.
Highly weather-resistant, the M16KD tracker withstands wind gusts of up to 115 mph; a version with heavier purlins is available for wind speeds up to 135 mph. The M16KD also withstands snow loads of nearly 35 psf, although snow loads have been demonstrated to shed readily in Canadian latitudes.
The flagship M18KD tracker supports 90 solar panels. The company’s unusually high-yield trackers have the highest energy density and the lowest ground footprint in the industry. Mechatron solar trackers include gearless azimuth trackers and gearless dual-axis trackers, which are designed to maximize performance with a lower operations and maintenance cost than other commercially available tracking systems. They have been successfully tested under different climate conditions rate structures constitute the best available solution for photovoltaic plant installations.
Mechatron was certified under UL 3703 in 2022 and completed a bankability analysis by Black & Veatch. The flagship tracker also features a new digital guidance system, along with a new optional design with eight columns to accommodate large format modules. The M10KD residential model features a reduced table size to support 49 panels, to accommodate limited space requirements.
MK18D Carport Tracker
The M18KD-20 carport tracker yields 40kW of power, is capable of 360 azimuth rotation and 0-25 degrees of elevation tilt.
Best suited for: Carports where available land space is limited or constrained.
Advantages of design: The M18KD-20 offers dual-land use. The single mast allows deployment with minimum parking area usage and provides uniform shade to vehicles while harvesting the highest possible energy from the space, yielding over 2,200 kWh/kW annually.
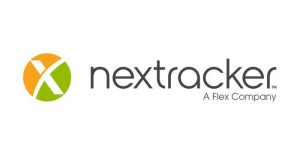
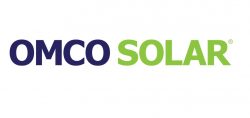
What’s new in 2022
OMCO Solar has launched its revolutionary Origin Bifacial Tracker. The open backside design delivers high energy yield with uniform irradiance, ensuring excellent long-term production. The foldable, pre-assembled module frame and bearing provide quick, easy installation. Combining design innovation with factory direct production capabilities, this versatile 2-in-landscape tracker delivers performance and economic value for customers.
Turnkey services
- On-Site Pile Testing. OMCO can provide customers with pile testing for their solar projects across the United States. This includes a 3rd party stamped report that can be used for foundation design and is a cost-effective alternative to geotechnical reports.
- Engineering Design & Site Optimization. OMCO has an experienced engineering team that can provide customers with stamped construction drawings and calculation packages. We also have the ability to optimize a project design to maximize the benefits of OMCO products.
- Single Point of Contact Contracting Model. OMCO provides fast and efficient delivery of a completed racking solution while minimizing transaction costs and construction delays that are typically associated with the conventional multiple-contract method. Our single point of contact contracting model streamlines the process significantly for customers.
- Buy Direct from the Manufacturer. OMCO has four manufacturing facilities that provide superior customer support from a knowledgeable and experienced team. This also means that OMCO can offer highly competitive pricing and reduced lead-times, which can be challenging for other suppliers.
Products
Origin 2L Bifacial Factory-Direct Tracker
Posts per row: Dependent on soil conditions, type of posts and row length — average is 11 to 13 per row.
Row lengths: While 96 modules per row is most common, OMCO Solar can customize to accommodate up to 112. Unique bearing technology allows long straight rows — 4 strings when others can only mount 3 — fewer motors and controllers per MW.
Slope Tolerances: Up to 15% for a North-South Slope
Design: OMCO Origin 2L (2-in-Landscape) Bifacial Trackers are primarily constructed of galvanized steel and cast aluminum. Bearings include a wear surface composed of a unique long-life, low-friction, self-lubricating acetal blend. A balanced design allows for more accurate targeting and reduced energy consumption. Some subassemblies are factory preassembled and shipped as single units for labor, time and cost savings. The unique bearing adjusts to accommodate post misalignment. OMCO Origin 2L Bifacial Trackers are open on the back — no torque tube blocking the cells — for highest energy production. The height of the tracker is low — like 1-in-portrait trackers — to minimize installation labor. Foundation options include OMCO-produced driven C posts (preferred) and driven I or W posts, and ground screw foundations.
Advantages:
• Factory Preassembled: Some subassemblies are supplied as single, preassembled units for installation labor savings.
• Balanced Design: Axis of rotation at the center of mass of the table — improves targeting accuracy, increases energy production and minimizes energy consumption.
• Long Wear Life: Bearings tested to more than 40 years equivalent life.
• 7 Dimensions of Adjustment: Bearings adjust to accommodate post misalignment, avoiding project delays.
• Over 20% Higher Back Side Production: The open back allows uniform backside irradiance, which is critical for long cell and module life.
• Shortest Lead Times: Partners benefit from expedited delivery due to OMCO Solar’s four strategically located U.S. manufacturing plants. Lead times are typically 8 to 12 weeks.
Domestic Content: OMCO makes all structural components with domestic steel and is well positioned for IRA ITC benefits.
CHOICE Factory-Direct Fixed-Tilt
Number of pieces: 8 Typical Components + Hardware
Certifications: ISO 9001:2015 Standard, UL 2703 Ed. 1, CPP Wind Tunnel-Tested, NEC Compliant
Terrain Articulation: Accommodates up to a 20% grade change
Installation:
- For a pile-driven foundation, posts are driven into the ground.
- Pre-assembled tilt bracket assemblies are bolted onto the piles.
- Lateral beams are then connected by fasteners to the tilt assemblies.
- Modules are secured with fasteners directly onto the beams to provide a secure bond.
Advantages: Pre-Assembled tilt assembly optimizes packaging & shipping, reduces on-site labor requirements, accelerates total build time, and eliminates loose hardware along with third party grounding devices. This in turn accelerates the assembly process. All structural components are manufactured in OMCO Solar’s six U.S. manufacturing plant facilities. With the company’s factory-direct model and domestically sourced supply chain, OMCO Solar consistently delivers quality solar mounting solutions with the shortest lead times in the industry.
www.omcosolar.com | Sales: info@omcosolar.com
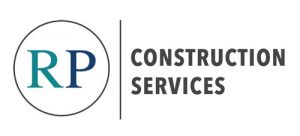
RP Construction Services, Inc. (RPCS) provides turnkey design, structural engineering, procurement/supply, mechanical installation, and specialty services to EPCs, developers, and municipal utilities. As the nation’s leading contractor and Array Technologies single-axis tracker expert, RPCS has completed more than 900 projects, totaling over 3GW, and helps customers meet their renewable energy goals with simple, seamless project execution. RPCS has approximately 300 employees and is headquartered in Monterey, California, and maintains facilities in California, Mississippi, and Kansas.
Specialty
Projects of all sizes, 20-100 MW sweet spot
What’s new in 2022?
RPCS has invested a lot of resources in material warehousing and expanded its tracker row kits. RPCS has the ability to stock all the key components and ensure that they are not only ready when needed, but also packaged and delivered to the site in a way that speeds up the installation of the trackers. They’ve also developed an in-house software program that is designed around the tracker they deploy and allows customers to see their portfolios of projects moving through each step of the way.
Product
eBOS solutions
Solutions: DC collection, wire management, and MV cable and accessories.
Basics: We streamline the eBOS procurement process with a “one-stop-shop” approach to electrical supply.
Key features: Our partnerships with the industry’s leading brands gives us the ability to extend our focus on design, constructability, and customer success to the electrical balance of plant. Our end-to-end solutions allow you to work with one passionate supply chain partner instead of a patchwork of generalist distributors.
Installation explained: With high volumes of on-hand inventory, our solutions reduce lead times and provide certainty to customers with tight construction schedules.
Are there racking/tracker partner integrations or brand-specific versions available? If yes, list them: Our solutions support both Array Technologies and Nextracker systems.
Array Technologies DuraTrack
Row lengths: 100+ module row lengths, up to 126 meters long (varies based on module size and weight)
Slope tolerances: 15 degrees N/S; 37 degrees E/W
Certifications: UL 2703, 3703 and IEC 62817
Design: The Array tracker can be custom designed, supplied, and installed by Ampacity Renewables, Array’s trusted partner and leading Array tracker installer. Ampacity Renewables is dedicated to offering customers the best overall experience, with a team of over 300 tracker experts to offer support. Linked rows are powered by an AC motor, an articulating driveline, and a rotating gear drive. Up to 32 rows can be controlled by just one motor.
Advantages: The DuraTrack boasts up to 25% energy gain over fixed-tilt systems and has an unparalleled track record of high uptime (99.996%), 7% lower LCOE, and 31% lower lifetime O&M with zero scheduled maintenance. The Array tracker utilizes the fewest motors per MW, with 167 times fewer components, and is the most adaptable tracker in terms of terrain, with low grading and the ability to be readily deployed on the most challenging parcels. In addition, the tracker is designed to mitigate high wind loads, snow loads, and inclement weather like hail.
NX Horizon by Nextracker
Row length range: Configurable per module type, string length and site layout.
Slope tolerances: Up to 15% N-S and 15% E-W
Certifications: UL 2703, UL 3703, IEC 62817, CSA
How does it install? With pre-assembled components, no drive linkages, no AC wiring, self-aligning rails, and available XTR terrain following upgrades, NX Horizon is fundamentally faster to install, requiring less construction labor, less grading, and less total project capital cost.
Advantages: NX Horizon’s patented independent row, self-powered tracking system provides reliable performance across the widest possible range of site conditions. Simple, robust hardware, including self-aligning module rails and vibration-proof fasteners, enables rapid installation and long life without maintenance. Mechanically balanced rows minimize tracking power requirements and pair with a time-proven, rugged drive and control system for maximum durability and uptime. NX Horizon’s decentralized architecture with intelligent communications supports maximum layout adaptability, flexible construction and commissioning sequencing, advanced tracker functionality, and over-the-air updates.
Unique software capabilities? TrueCapture combines advanced sensors, weather forecasting, and machine-learning technologies to maximize energy generation for new and existing solar power plants. The software’s intelligent, self-adjusting tracker control and yield optimization system boosts solar power plant production by continuously optimizing the tracking algorithm of each individual row in response to site features and changing weather conditions.
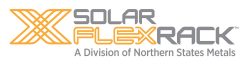
Solar FlexRack, a division of Northern States Metals, is an integrated solar company that offers reliable and time-tested custom-designed, fixed tilt ground mount and single-axis solar tracking systems in the commercial and utility-scale solar mounting industries. Solar FlexRack also offers full spectrum engineering support, including electrical, mechanical, structural, geotechnical & process, to enable your project to be completed efficiently and cost effectively. Solar FlexRack has completed over 1,000 solar racking installations in nearly all 50 U.S. states and five countries, representing a total of 3 GW of solar power projects.
What’s new in 2022?
“Each of our product lines – fixed tilt, ballasted and trackers – are now fully adaptable to the wide range of large format modules on the market,” says Mike Herman, Director of Operations. “Large format modules are increasingly being used due to their ability to increase energy yield through more watts per tracker and reduce Levelized Cost of Energy (LCOE), including through reduced hardware costs and project soft costs. However, they pose additional challenges when it comes to handling wind speeds and snow pressures. We are pleased that each of our product lines have been rigorously tested to integrate with, and have and continue to be successfully deployed with, large format modules. In fact, our products are now being integrated with large format modules in about 70 percent of our projects.”
Products
Fixed Tilt Series G3-X
Installation: Solar FlexRack Series G3-X Ground Mount Rack installs quickly, features similar-sized hardware and requires only standard tools and equipment for assembly. The system is easily staged on job sites and can be assembled in a logical, step-by-step manner in the field by crews of any skill level. With best-in-class engineering, the G3-X has unique design attributes that ensure ease of installation. The system’s lateral bracing stabilizes and perfectly squares the racking system, so modules easily slide into place for fast, safe, and easy module installation. While mostly pre-assembled, the horizontal rail bracket allows racking to be held in place while aligning rows with terrain. The G3-X can be easily assembled on site or can be delivered partially pre-assembled.
Advantages: Solar FlexRack prioritizes module structural integrity with its racking design, and keeps modules in prime condition through construction and beyond. The G3-X Series is a robust, efficient and low component design that installs quickly and easily. It is compatible with all foundation solutions and comes with automatic system squaring, lateral bracing, horizontal rail brackets, and slotted connections for ease of installation. It also allows for safe and quick module mounting with a direct bolt bonded connection. The G3-X leverages the company’s field-proven install base of over 3 GW to deliver the highest quality, pre- or field-assembled ground mount systems that accommodate up to 20% slopes for reduced civil costs.
Certifications: UL 2703 (Issue 2)
Fixed Tilt B Series Ballasted (Cast In Place or Pre-Cast)
Installation: SolarFlexRack’s Ground Mount Fixed Tilt B Series (Ballasted) solution is available with blocks pre-cast offsite or cast-in-place (CIP) on site utilizing Solar FlexRack’s unique, easy to assemble form system. The CIP solution requires only six screws for form assembly, which can be complete in under three minutes with two people. Watch the video of how easy CIP is assembled.
Advantages: Conveniently available with blocks pre-cast or cast-in-place to meet each project’s unique needs, Solar FlexRack’s Ground Mount Fixed Tilt B Series (Ballasted) solutions are well-suited for landfills and challenging terrain sites. The FlexRack Series B pre-cast solution makes use of a two-support system that transfers loads into the block through double the supports for reduced block thickness, as well as enables the use of a split block system, which requires lighter lifting machinery to accommodate sites with low bearing pressure requirements. The cast-in system allows for quick assembly and adjustability, reducing overall labor costs.
Certifications: UL 2703 (Issue 2), ISO 9001
TDP 2.0 Solar Tracker with BalanceTrac
- Row lengths: Up to 90 modules per independent table
- Slope tolerances: Up to 10% North-South slope tolerance
- Certifications: UL 2703
Construction: Independently driven; single-axis horizontal, distributed drive. Drive type: Slew. No special tools required. Any tools needed could be acquired at your local hardware store.
Advantages: Solar FlexRack’s reliable TDP 2.0 Solar Tracker with BalanceTrac bundles an advanced tracker design with top-tier engineering and project support services to safeguard solar projects from unexpected costs. One of the easiest trackers to install, TDP 2.0 features smart backtracking to reduce row shading & maximize energy yield. The TDP 2.0 has an increased table size to provide optimal module density as well as compatibility with 1,000V and 1,500V modules. In order to enable greater adjustability to maximize system performance, the TDP 2.0 features a rotational range of 110° (± 55°) and ground clearance that allows for shorter piles.
TDP 1.0 Solar Tracker
- Row lengths: Up to 60 modules per independent table
- Slope tolerances: Up to 10% North-South slope tolerances
- Certifications: UL 2703
- Design: Single-axis, horizontal, distributed drive
- Drive type: linear actuator
Advantages: Field-proven with over 75 projects installed in North America, Solar FlexRack’s TDP 1.0 Solar Tracker leverages a simple, efficient design for highly reliable and easy installations. Ideal for smaller or highly irregular layouts, the TDP 1.0’s small drive block enables up to 40% reduction in land use. The TDP 1.0 also utilizes a distributed drive and has no mechanical components between rows, allowing for easy and cost effective access for mowers, cleaning services and other project maintenance. Complete with Solar FlexRack’s full spectrum engineering and project support services, the TDP 1.0 features smart backtracking to reduce shading across rows and maximize energy yield.
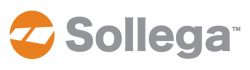
Unique compared to the rest in this section, Sollega provides one racking system that can go from the commercial rooftop to the ground. The universal design, manufactured from UV rated glass reinforced Nylon 6, enables the installation of all framed modules and stands up especially well in highly corrosive conditions near the ocean. Injection molded in California, 100 percent made in the USA.
Product
www.sollega.com | Sales: Info@sollega.com
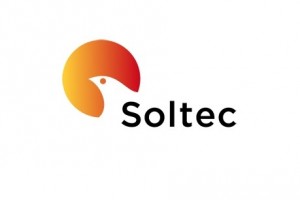
Soltec specializes in integrated solar photovoltaic solutions, whose business is focused on solar tracking systems with a strong commitment to innovation. Soltec is positioned as the world’s third leading company in the market among solar tracker suppliers, and leader supply in countries such as Brazil or Chile. With headquarters in Spain, Soltec has been operating since 2004 and has a diversified geographic presence focused on Spain, North America and Latin America. It has presence in 16 countries with more than 1,300 employees.
What’s new in 2022?
Soltec launched the Solarfighter kit last year, which includes both the product and the plant assembly service. In addition, Soltec’s Solmate after-sales service includes all maintenance and care services for solar plants.
Products
SF7 USA
Mounting tolerances: Range from 20 to 40 inches. Can be installed on slopes of up to 17%.
Installation: Soltec pre-assembles most components, so the installation includes few steps. Locating the parts and pieces needed at each step is quick. All of this results in substantial savings in both time and financial resources.
Design: The tracker features an electronic system that incorporates wireless communication designed to withstand low temperatures.
Software: TeamTrack system delivers up to 6.8% more yield, a function that minimizes shading losses between rows, especially on uneven terrain. Diffuse Booster technology allows for optimal energy generation, even on cloudy days, by capturing diffuse radiation. Dy-WIND methodology, solar tracker response to wind is ensured, preventing damage to the plant during heavy precipitation.
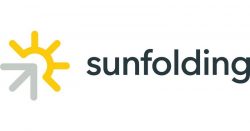
Sunfolding maximizes profitability with innovative solar tracking technology. Powered by air, the Sunfolding T29 Single-Axis Tracker deploys on land previously off limits to utility-scale solar. The Sunfolding T29 also makes solar plants faster to install and easier to operate. Sunfolding has won recognition as a 2020 Global Cleantech 100 Company and a 2019 Bloomberg New Energy Pioneer. Headquartered in Alameda, CA, Sunfolding ships US-manufactured trackers throughout North America.
Specialty
Projects above 5 MW, especially those that can benefit from earthwork savings.
What’s new in 2022?
Working closely with our customers, Sunfolding has scaled down the T29 Single-Axis Tracker to two posts so we can navigate terrain and topographic features with even more flexibility and at no added cost. To begin with, actuation on every post brings unparalleled flexibility. The ability to reset tracker tables every 25 to 30 feet vastly improves tolerances on the east-west axis and in terms of tracker height. Dips and swells at ground level no longer have any impact on system design. A tracker can go from a steep rising slope to a steep falling slope or anything in between. Instead of designing one 300-foot span at a time, take advantage of the granular ability to follow terrain undulations from one plane to another and another and reduce earthwork by more than 90%.
Products
Sunfolding T29 Single Axis Tracker
Number of pieces: 3 structural components
Row lengths: 1 to 2 strings in length
Slope tolerances: Up to 12.3% grade slopes with no change to standard product
Design: With just three unique structural components, Sunfolding makes construction easier. From the post all the way to the modules, we streamline and expedite the installation process. By reducing the number of post sizes that you’re dealing with, we have reduced the possibilities of misplacing a post or misdriving a post. With a shorter post embedment depth, Sunfolding minimizes interaction and contact with subgrade rock.
Advantages: The Sunfolding T29 optimizes solar tracking and maximizes energy output. Unlike motor-driven trackers, the Sunfolding T29 makes solar infrastructure simple again. Sunfolding projects neutralize costs with flexible layouts that fit the trackers to the land. Small tracker tables enable denser DC per acre without driving up costs and reduce earthwork by more than 70%. Fewer components makes every project simpler and allows for a reduction in construction costs by more than 15%.
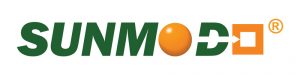
Specialty: residential and C&I <500 kW
SunModo, meaning “the way of the sun,” is a private U.S. company headquartered in Vancouver, Wash., that is focused on innovative racking and mounting solutions for professional installers in the fast-growing solar industry. Our commitment to innovation can be seen across our entire product line, which includes 20 plus industry-shaping patents. From residential rooftops to large-scale ground-mounts and everything in between, SunModo has the most comprehensive solar mounting and racking solutions.
SunTurf Ground Mount
Average row construction time: 4LX12 array 20K system installed within 1 day (10am-2pm)
Slope tolerance: Up to 27% slope east-west.
Certifications: UL 2703
Installation: No cutting, welding, or drilling. Adjust height and install posts with set screws. Pipe fittings attach quickly with set screws. Two-piece pipe caps make installation easy. Structural splice with set screws for bonding. Fast rail attachment with T-bolts. The SunTurf Ground Mount System easily integrates Helio Rails with Schedule 40 Steel Pipes. Combine SunTurf with SunModo Ground Screws or Augers and do a complete install of a 15-kW system with only one day on the job site. For a more interactive look at SunModo’s Ground Mount, check out this video.
Advantages: SunModo offers the next generation SunTurf Ground Mount System. The streamlined design combines the simplicity of a pipe-based system with next-level engineering. SurTurf Ground Mount is ideal for solar installers looking for a low cost high performance system that can accommodate a wide variety of soil conditions. No drilling is required to attach the aluminum rails to the horizontal pipe. The innovative swivel pipe cap kit can accommodate terrains up to 27% slope east-west and 120% slope north-south.
Comments are closed here.