Waterproof review: Is 2703A a step in the right direction?
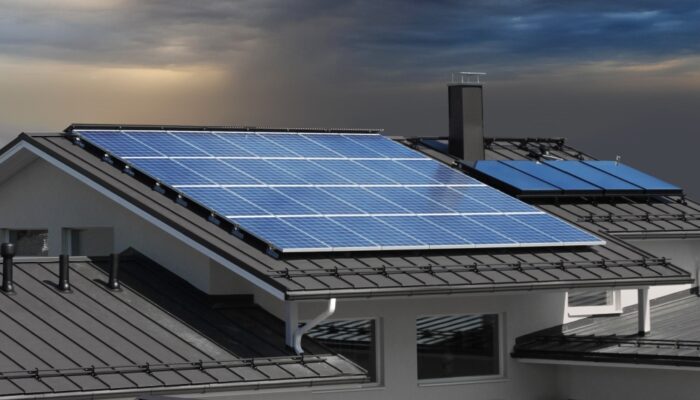
UL 2703A is a certification standard for both polymeric and metallic attachments used in solar racking systems. It sets testing criteria to ensure that flashing products prevent water penetration, protecting the roof and structure from potential damage.
“As modules grow in size and complexity, and solar installations increase, it is crucial that flashing systems provide durable, reliable protection, and UL 2703A helps address this by standardizing the performance of these products,” says Nico Martinez, residential category manager, Unirac.
This certification process involves rigorous tests, including aging, UV resistance, tear resistance, and water penetration, to ensure that products meet high standards for durability and waterproofing.
Additionally, this standard streamlines the permitting process by offering greater assurance to local authorities and finance companies.
“As a game-changer for the solar industry, we expect widespread adoption of UL 2703A by building codes and AHJs in the near future,” Martinez continues. “It offers a unified testing and approval protocol for PV flashing devices, providing clarity and confidence in protecting the roofs of residential and commercial installations.”
“While I am typically cautious about the introduction of new standards, I believe UL 2703A is essential for our industry,” says Mark Gies, director of product management with S-5!, who served on the committee, spearheaded by UL, responsible for developing the initial version of UL 2703A. “It fills a critical gap in evaluating the interface between racking and the roof, which historically has led to inconsistent assessment methods and uncertainty among AHJs during project permitting.”
As with nearly all codes and standards, not everyone is convinced the language and testing is sufficient.
“In its current draft form, the standard limits new and improved waterproofing technologies currently available and in development. However, the standard has insufficient testing protocols for long-term use,” says Kai Stephan, CEO and founder of Pegasus Solar. “For example, what may happen after thermal and loading cycles on curing sealants? What happens after a season of extreme temperatures and applied lateral loads from snow? 2703A doesn’t address this, yet 100% of solar flashings and sealants will be subject to daily thermal cycling. Additionally, the tests are conducted on brand new comp shingles that have not been subject to heating from the sun.”
Stephan points out that many roof leaks today are caused by a tear in the shingle, often from ripping up the front lip of a shingle to slide in a flashing.
“Traditional comp flashings worked with older comp roofs, but in the last decade shingle manufacturers have increased the adhesive properties of the lower edge of the shingle, increasing the likelihood to tear when being pried up by a traditional flashing. 2703A doesn’t address this, and actually allows an easy path for traditional comp flashings to be approved through test standards that use new shingles where the front lip has not yet fully adhered.
“There is value in having 2703A as it should help improve the quality of products used for roof penetrations. However, the draft standard should be updated to address long-duration testing, installing on new shingles that have fully adhered after a few temperature cycles, and to allow for advances in waterproofing technology, such as non-hardening sealants.”
Adjusting for large format modules
Large format PV modules are typically more than 2 meters long and are causing significant issues for traditional mounting and clamping strategies for racking manufacturers. As module sizes increase, existing engineering documents, which are based on smaller module dimensions, often become obsolete.
“Existing documents fail to account for the increased mechanical stresses and different load distributions introduced by the larger modules, necessitating a complete overhaul of mounting guidelines and practices,” says Peter Abou Chacra with SunModo.
In regions with high wind loads, traditional module clamps become critical points of failure. The larger surface area of large format modules exerts greater force on each module clamp, which makes the clamps the weakest link in the system. “This situation often forces installers to incorporate a third rail to better distribute the load and enhance the overall stability of the installation,” Abou Chacra says. “Without such modifications, the risk of module clamp failure under high wind conditions increases, potentially leading to module damage or even system collapse.”
A greater surface area means increased wind uplift pressure, which can create limitations on the allowable design pressure when clamping in certain areas, particularly near the corners of the modules.
“Traditional ballasted commercial mounting systems often use corner clamping, which can exacerbate these issues,” says Ryan Estrada, technical program outreach manager, Unirac. They adapted to these challenges by leveraging Bessel points, named after mathematician and physicist Friedrich Wilhelm Bessel. “This principle helps minimize the bending of horizontal beams by supporting them at specific, optimal locations.”
Additionally, the higher module width of larger panels creates cut length issues and results in additional rail waste. “Traditional rail lengths are optimized for smaller modules, leading to inefficiencies and increased material costs when adapted for larger panels,” Abou Chacra says. This mismatch drives up installation costs and environmental waste.
“Be sure to consider the total costed [bill of materials], rather than just the panel cost, to ensure using larger panels saves money,” Stephan adds.
Comments are closed here.