The case for metal wire management in large-scale solar systems
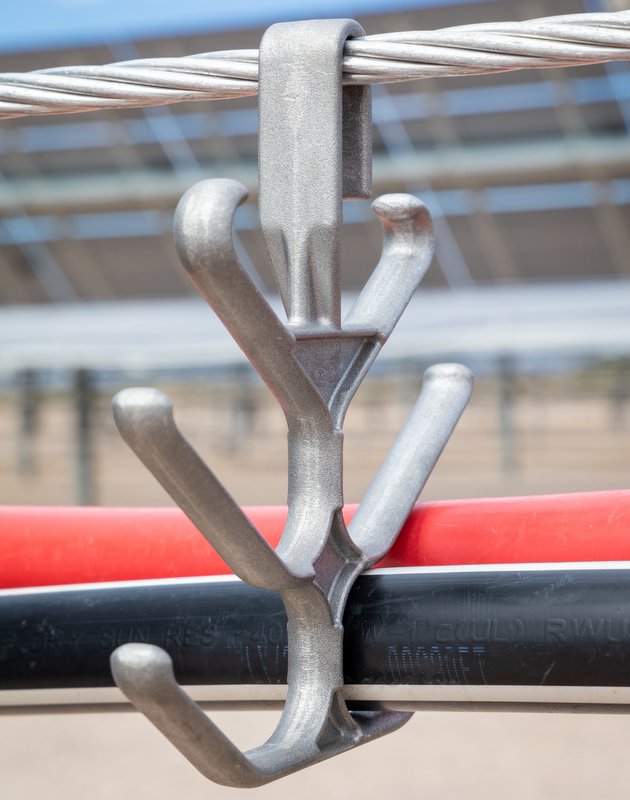
For as long as large-scale solar has existed, polymetric (plastic) materials have predominately been used in the wire management sector. Whether off-the-shelf zip ties or plastic-coated hangers, these products are problematic for a number of reasons.
The biggest issue is that high UV and heat exposure, the main environmental conditions on a solar site, degrades plastics at a rapid pace. Have you seen plastic zip ties lying on the ground of a solar project? How about a plastic-coated hanger where the color has entirely deteriorated within a few months? These are visual indicators of failing components.
Within the lifetime of the project, these plastic components will fail. Plant owners are inevitably forced to invest time and money replacing them – another unfortunate consequence of using plastic.
The move to metal
Given the rapid demise of these materials, the industry is transitioning to metal solutions – but not all metal, and often times not enough metal. Many designers gravitate toward a plastic-coated metal product because they feel they have the safety net of the metal’s durability, fused with the softness of a plastic coating. This false sense of security has given rise to products such as the plastic-coated metal cable tie (aka “the cable saw”).
Looking at this more closely, it’s worth considering the cause and effect of deteriorating materials. With plastic, it is not a question of “if” but “when.”
- When the plastic degrades around metal, how can the product ensure resistance to corrosion?
- When the plastic degrades, how can the product ensure safety to the conductor insulation?
- When the plastic degrades and is ultimately bare metal, how can the product ensure a reliable bond path?
Buyers, beware of products that advertise zinc-coated metal. These are often coated with a few microns of zinc, which is the bare minimum to pass any environmental conditioning. As project lifetimes increase, the zinc thickness requirements should also increase. 15-25 microns of zinc is more appropriate for the life of the solar project, which is proven by long-duration salt spray tests.
What’s the remedy here? All-metal products with engineered surfaces. Examples of all-metal products with engineered surfaces include an aluminum hanger designed with a large radius at every cable contact surface. Another example is a round wire formed into a product that can hold and manage cable.
These are reliable, result in a reduced LCOE, and have a lower carbon footprint. In fact, metal wire management components – if engineered appropriately – will last the lifetime of the plant, even in the most extreme weather conditions.
And, the environmental impact of metal fabrications is much lower compared to other polymeric material manufacturing. According to the Aluminum Association, a 12-oz aluminum can have nearly 50% lower associated emissions compared to a 20-oz plastic bottle.
Although it’s not yet a widespread practice, the industry is trending toward all-metal products that have engineered surfaces. With the reliability and long-term benefits, plus the lower carbon emission profile, many successful owners and their engineers are restricting the use of plastic wire management components in their contracts. In the near-term future, we anticipate wider adoption of all-metallic solutions because they provide benefits to every project stakeholder (including the earth).
Scott Rand is CEO and Founder of Affordable Wire Management (AWM).
Comments are closed here.