Smarter coatings needed to protect smart energy meters from failures in harsh environments
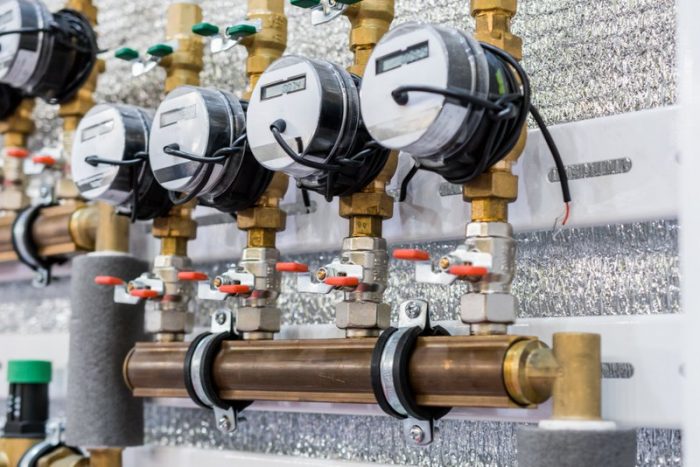
Since the Wrestlemania-like standoff between Pacific Gas & Electric and a fired up crowd of naysayers and conspiracy theorists in 2010, smart meters have been embraced by consumers and widely deployed by utility companies.
Driven by government incentives, cost savings, and a growing need for visibility at the grid edge, almost every energy supplier worldwide is installing them as part of a global upgrade to the energy system. Just as low-power, wide-area networking solutions changed the game for water and gas utilities, electric utilities and consumers are capitalizing on conservation, safety, and data. Analyst firm Research and Markets reported the global smart meters market will reach $12 billion by 2024, backed by continued upgrades of utility infrastructures and increased investments in smart grid projects.
However, despite their technical maturity and value, there is potential for component failures, which are most commonly battery, clock, display, burning, or communication faults.
Smart meters explained
Smart meters can provide accurate, detailed analytics on utility usage in real-time or at predetermined intervals without a technician. Advanced Metering Infrastructure (AMI), the integrated system of smart meters, communications networks, and data management systems, are a mass of sensors, hardware, software, communications, consumption displays and controllers, customer systems, data mining software, meter data management software, and business systems that provides the means for two-way communications with the meter. AMI enables the ability to send commands from the utility to the smart meter for monitoring real-time values and changing the frequency of readings. The network between the smart meters and the utility center allows the collection and distribution of information to customers, suppliers, utility companies, and service providers. The layered architecture facilitates the classification of components and interfaces into different categories according to merits and objectives.
Billions of dollars have been invested in AMI, which provides functions not previously possible or was once performed manually. Combined with the Internet of Things (IoT) and customers’ connected technologies, AMI enables utilities to offer new time-based rate programs and incentives that encourage customers to reduce peak demand and manage energy consumption and costs. As more large-scale smart meter programs are rolled out, utilities realize the value of detailed information on leaks, service quality, violations, and security alerts.
Smart meters have a simple yet sophisticated architecture.
- A current transformer increases or decreases alternating currents from the utility into the home or building.
- A power converter that transforms analog power to digital to drive components on the meter.
- Processors provide instructions and programming logic.
- A modem for wireless communication with the utility.
- An internal battery allows the meter to communicate with the utility through the modem if the power to the meter is disrupted.
- An operator interfaces for customer or service technician point of contact for interaction with the meter to extract data.
- A cover snap and detect switch determines if the meter’s exterior has been tampered with.
- A hall effect sensor determines if someone uses a high-power magnet to saturate the current transformers to prevent correct power readings.
But smart meters are not installed in utopian locations.
They replace manual meters that were located in cobwebby basements or a box attached to the outside of the home. Regardless of location, they must endure harsh environmental conditions, such as varied temperature ranges, rain, snow, salt, and humidity, that can corrode the contacts. The switches specified for use on smart meters must also be ruggedized and reliable enough to withstand adverse conditions for the meter’s life. Because smart meters draw power from the electrical grid, they are also subject to high energy transients resulting from lightning, inductive load switching, or capacitor bank switching.
When smart meters fail, currents can flow unimpeded across the circuit board and into the building or home along with the electrical wiring. It can result in burned wiring, burned outlets, damaged appliances, electronics, and other devices, and fires.
Smart meter failures can run as much as 3% per annum with issues that range from installation, damages due to theft, and environmental challenges caused by extreme heat, cold, and humidity. When damages occur, they typically happen very quickly – in a matter of seconds. If the meter is not completely fried, damage can cause a reduction in the smart meter product lifespan, which should be 15 years if manufactured per the Department of Energy (DOE) National Institute of Standards and Technology’s protocols and standards.
Smart meter failures are expensive. There are more than 775 million meters installed annually. The 3% per annum failure rate equates to the potential of 38 million meters that may need service each year. Field failures result in warranty claims, unnecessary logistics, failure analysis costs, and brand damage. Repairs, including truck rolls and parts, can cost a minimum of $300 per meter.
Currently, there is no smart meter model with enough technical features to cover all possible failures in a real-world environment. The best possible scenario for ensuring the safety of end-users and the success of the smart grid is to protect smart meter components and circuitry.
The case for conformal coatings
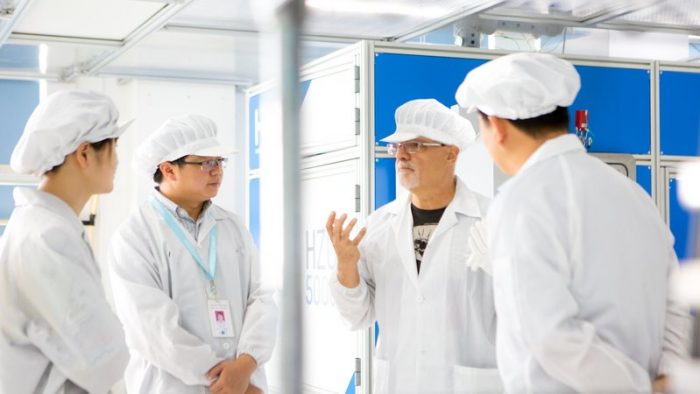
The realistic and economical approach to protecting smart meters is conformal coatings. These polymeric film-forming products protect circuit boards, components, and other electronic devices from adverse environmental conditions and mitigate circuitry breakdowns. As the name implies, they conform to the structure and environment of the items being coated, thereby providing increased dielectric resistance, operational integrity, and protection from corrosive atmospheres and contaminants, including humidity, heat and cold, mold, dirt, and dust.
The question is – which conformal coating? The chemical composition of each determines its attributes and operational function.
Acrylic Resin – Acrylic conformal coating provides fair elasticity and general protection – or what is considered basic, entry-level protection. It is recognized for high dielectric strength and adequate moisture and abrasion resistance. Acrylic is easy to apply and remove, making rework and field repair practical and economical. Still, it does not protect against solvents and vapors, making it less than ideal for many applications.
Silicone Resin – Silicone conformal coating is moisture, chemical, salt spray, and fungal resistant, making it appropriate for high-humidity environments. A soft and flexible solder-through coating has good dielectric properties that can withstand wide temperature ranges. Its flexible nature makes it unresistant to abrasion, but this property makes it resilient against vibrational stresses. This quality makes removal a challenge, requiring specialized solvents, long soak time, and agitation from a brush or an ultrasonic bath.
Urethane (Polyurethane) Resin – Urethane conformal coating is known for excellent moisture, chemical, solvent, and abrasion resistance. It is challenging to remove. They are applied as single or two-component formulas with claims of suitability for printed circuit boards.
Epoxy Resin – Epoxy resin conformal coating is usually available as a two‐part compound and creates a tough coating. It enjoys humidity resistance and is not generally permeable. It has high abrasion and chemical resistance, which makes removal very difficult once cured.
Parylene – Parylene, with its unique chemistry, and deep molecular reach, has emerged as the conformal coating of choice for various industries, including automotive, medical, aerospace, military, industrial, and consumer electronics. Parylene has all the properties and characteristics necessary to help advance technologies compared to acrylic, silicones, urethane, and epoxy coatings. There is no liquid phase with Parylene, and it is genuinely conformal. It can create a uniform controllable thickness that is entirely pinhole-free at thicknesses greater than 0.5 µm, even for the most intricate and complex shapes. This ultra-thin coating can penetrate spaces as narrow as 0.01mm.
Parylene is inert, insoluble, thermally stable between -200°C and 125°C and higher, has a dielectric strength of 7 kV/mil, and has high elasticity with an elongation break of 200%. It acts as a dry film lubricant, eliminates the need for liquid release agents, and protects from a range of contaminants, including moisture, corrosive fluids, chemicals, gases, and fungus.
Parylene is applied near room temperature, which means any object that can be exposed to a medium vacuum can be coated. Overall, its distinctive properties can be used to provide protection solutions to a wide variety of applications. Manufacturers are often amazed at the sheer number of items that can be effectively coated with Parylene.
Smart meters are important technical innovations and the data they collect are advantageous. By incorporating the advanced technology of Parylene coatings, smart meter life expectancy is improved in ways other methods cannot. Electronic failures that are often construed as inevitable can be prevented by design. Designing and implementing coatings into smart meters can help meet cost-effectiveness, sustainability and add product features that address the factors that can lead to unexpected failures and address the market with higher reliability products.
John Sandilands is HZO’s director of sales with responsibility for driving market diversification and new customer acquisition, especially in communications, computing, automotive, industrial, military, and medical markets. Before joining HZO in June 2019, Sandilands served as senior sales manager and account development for Toshiba Americas Electronics Components where he drove account acquisition and revenue growth in the Pacific NW Region and Western Canada. He created the company’s go-to-market sales strategies for both semiconductor and storage divisions that yielded more than $7M in business value. He was equally as successful in positions with Eurotech, Sharp Microelectronics, and Vishay Intertechnology. Sandilands holds a Bachelor of Business Administration from Concordia College and Strategic Sales Management and Market Development Theory certifications from Sheridan College.
Comments are closed here.