Solar Tracker Bearings 101: What they do, how they fail and how to avoid it
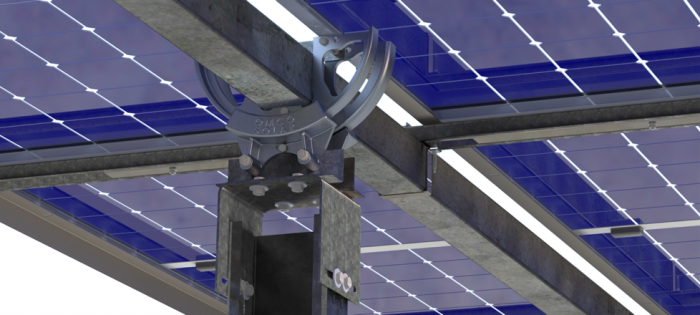
Wide adoption of solar photovoltaic technology for utility-scale energy production, in the US and worldwide, is driven largely by the low cost to produce solar energy, now often less than $0.03 per kWh in the U.S. Utility-scale solar power plants usually require trackers to maximize energy production and minimize the cost of energy. A core solar tracker component is the system’s bearings.
Bearings are key to a tracker’s ability to follow the sun smoothly and accurately, producing the most energy with the least possible maintenance. An excellent bearing will be cost-effective, quick and easy to install, operate smoothly for many years and cost little or nothing to maintain.
Here are some bearing basics to know to help you identify quality tracker bearings and to keep your existing arrays moving smoothly for many years.
What is a tracker bearing?
Bearings are the devices that connect the moving parts of a tracker – including the modules – with the stationary posts or piles. The lower part of the bearing is attached to a galvanized steel post, and the upper part moves along with the “table” – the modules and the structure which holds them – as the table is driven from east to west by a motor or another type of actuator.
Between the lower and upper part of the bearing, there is some wear surface or roller – a material which experiences friction and which may wear over time – the key to the bearing’s function and reliability.
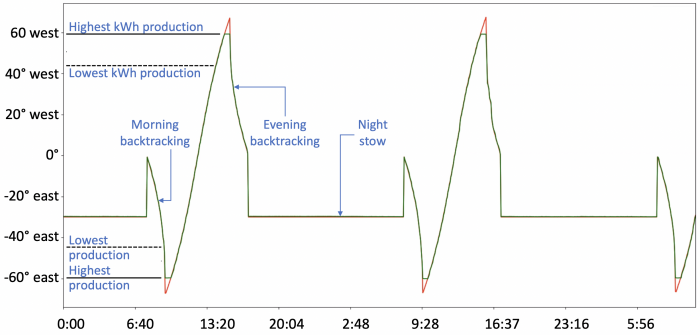
What does the bearing do?
The bearing allows the tracker’s table to move smoothly and with minimal friction. The bearing also defines the motion – exactly how the table moves – typically in a semicircular arc, from some angle facing east in the morning, to some angle facing west in the late afternoon.
For example, a tracker may move from 45° facing east in the morning to 45° facing west late in the day, but the modules will produce more energy if the tracker has a greater range of motion, such as 60° east to 60° west.
Essential functions of the bearing include:
- Quick and simple installation. Ideally the bearing is supplied as a single subassembly, with just a few fasteners to connect it to the post, not as several pieces which must be assembled at the site.
- Adjustment. If the posts are installed without problems, no adjustment to the bearings should be needed. But if the posts are installed imperfectly – for example, if rocks under the surface cause a post to be too high, too low, or tilted in some direction – the bearings should allow for some adjustments, so the posts do not have to be removed and replaced. Some bearings enable adjustments up or down; east or west; and in various ways to compensate for a tilted or twisted post.
- Simple alignment, or no alignment. Ideally no complex alignment of the bearings will be needed for the tracker to function well.
- Motion. Bearings should let the tracker move smoothly, with minimal friction, when the motor, slew drive, or actuator pushes it.
- Range of motion. The bearings should let the tracker move as far as possible in each direction – east and west – so it can follow the sun and produce as much energy as possible. Older bearing designs may be limited to 45° east and west, with newer bearings enabling travel from 60° east to 60° west.
Vertical balance
A bearing’s design establishes both 1) the axis of rotation, which may be “real” like the axle of a wheel or “virtual,” and 2) the center of mass of the moving table – the horizontal line at the center of the table’s weight. If the axis of rotation and the center of mass are at the same height, the tracker is “vertically balanced.”
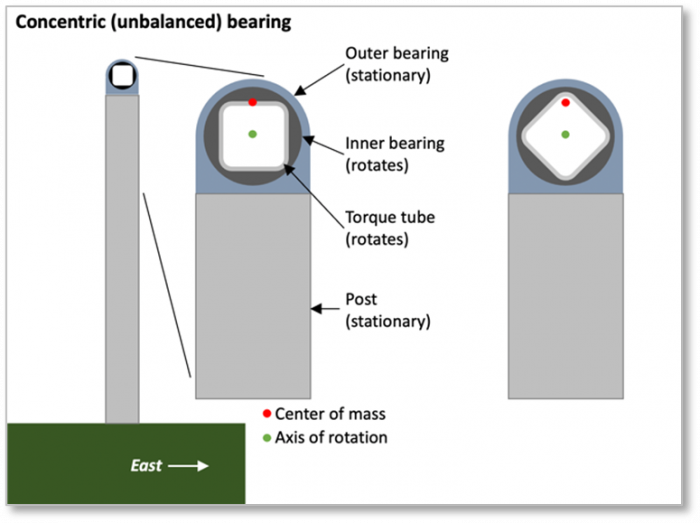
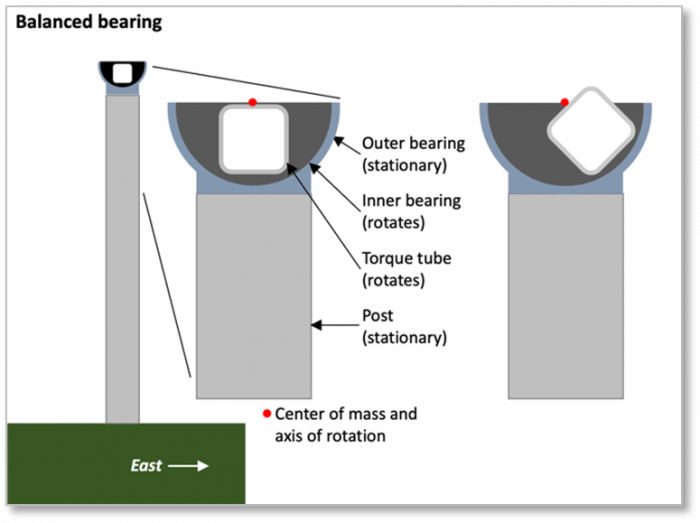
If the tracker is not vertically balanced, the weight of the table – including the heavy glass in the modules – will pull the table toward a more vertical position, which may make it track the sun less accurately.
An unbalanced tracker also consumes more energy when it moves, because the weight of the table must be lifted at least twice each day, as the tracker moves from its most vertical position toward a horizontal position.
How bearings fail
Leading tracker suppliers now design their products to work for up to 35 years, with little or no maintenance. So, it is critical that bearings work well over that design life. Bearings can fail because:
They are too weak structurally to hold up to strong wind gusts and snow. This can be prevented in the design process, by using Finite Element Analysis to simulate the bearing’s performance under high wind and snow, and by careful testing at loads higher than the bearings will be subjected to in the field.
The bearings are installed incorrectly. This is less likely when the manufacturer provides a clear, detailed installation manual.
The bearings are not properly aligned. But some bearings are designed so they do not need to be aligned, eliminating this failure mode altogether.
The wear surface is inadequate. This can be prevented by careful selection of the material, and accelerated life testing.
Bearing maintenance
Many bearings now supplied by leading tracker suppliers require no routine maintenance. The key is the wear surface – is it made of a material which enables smooth movement without periodic maintenance such as oil or grease? And will it wear slowly, so it will function well for the life of the tracker?
In any case, a periodic check of the bearings – typically every year or two – is worthwhile. Check for loose fasteners, broken or distorted metal components, or a visible change to the wear surface or rollers. Notice if all the bearings look the same.
And listen to the bearings as the trackers move – they should be nearly silent.
Questions for your tracker supplier:
- Do they have evidence the bearing is structurally adequate for the wind and snow loads at your site?
- Do they provide a clear and detailed installation manual?
- Do their bearings require time-consuming alignment at the site to work well?
- Does the supplier have data showing the wear surface will survive through the design life of the project?
You or your customer will be living with your solar tracker bearings longer than you own your car or maybe even your home, so choose your bearings – and your tracker supplier – carefully.
Matt Kesler is the Director of Solar Technology for OMCO Solar. Matt is a physicist with more than 20 years of experience in solar technology, including cells, modules, racks and trackers. OMCO Solar is a premier one-source, OEM manufacturer of solar tracker and mounting solutions for the community, commercial, and utility-scale markets. With a manufacturing footprint spanning coast-to-coast, the company engineers and delivers their solar structures to developer and EPC partners nationwide.
Comments are closed here.