What’s the most preventable ESS installation error?
As part of our 2025 ESS Buyer’s Guide, we asked ESS manufacturers “what is the No. 1 most preventable ‘installer error’ when installing and commissioning ESS?” Here is what they had to say.
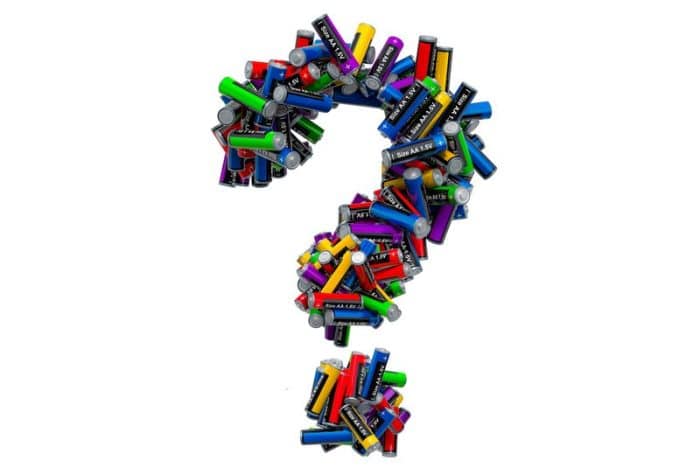
Wiring!
“Specifically, with closed-loop ESS, the primary error is with communication wiring. In addition to selecting the correct wire and communication port, the systems that use CAN protocol also need a terminal resistor. Terminal resistors are often small and easily misplaced, making it one of the two calls to technical services. I advise saving all accessories included with the ESS, as most will be needed during installation.” Sandra Herrera, Technical Sales Manager, GoodWe
“Incorrect wiring of measurement and communication components. This misstep can cause incorrect data collection, which can further cascade into issues in remote monitoring, sub-optimal battery charging and discharging cycles, reduced system efficiency, and missed cost-saving opportunities. By carefully following the manufacturer’s wiring diagrams and completing each configuration step, installers can ensure a smooth setup and avoid troubleshooting calls.” — Utsav Ghosh, Senior Director, Product Line Management, Enphase Energy
“Improper selection of wire gauge. Using undersized wires which are inadequate for the maximum current of a given circuit is a common, but preventable installation error. This is especially important when batteries are connected in parallel, as the potential current increases with each parallel connection. Installers may not realize this and can sometimes miscalculate the correct wire gauge required for a safe installation. Undersized cables may cause overheating, voltage drop and potential equipment failure. This affects the safety and efficiency of the entire system.” — Eli Chu, Product Manager, Pytes Energy
Being casual with manuals and plan checks!
“Not reading the install manual and confirming that the components are all meant to work together and carry the proper ratings. As requirements change and firmware is updated on many components, it is important to read through how the product should be installed, in what order components should be commissioned and how to correctly set up and monitor the system. Additionally, having a strong understanding of the codes and standards for their local AHJ. Take plan check seriously and realize that your local AHJ may be less familiar with battery storage, the system that is being installed, or the requirements. As installers, an important part of our job is education. An expectation that your AHJ is an expert on battery storage and is not susceptible to the same concerns as the homeowner that you are working with around safety is too often not common.” Sequoya Cross, VP Energy Storage, Briggs & Stratton Energy Solutions
Mismatching!
“Mismatching the battery capacity with the load or solar array size is a common issue. If the system is undersized, it can lead to frequent deep discharges, reducing the battery’s lifespan. Conversely, oversizing can lead to unnecessary costs and inefficiency.” — Zachary Kirin, Product Manager Residential Systems, Fronius USA.
Don’t Miss the Latest Fronius Webinar: Enhancing Energy Independence with Fronius.
Learn about Fronius’ innovative technology that ensures energy needs are met at all times of the day, even during power outages. You’ll also get an exciting sneak peek at our new Essential Backup Load Unit, designed to enable the Fronius GEN24 Plus to maximize energy storage potential. Watch on-demand here.
Communication and pre-planning!
“Communication and scheduling play a huge role in the ability to successfully deliver a project. Often commission folks are given short notice, which causes scheduling conflicts, and when available, the remaining team cannot be on site. It is vitally important to have all stakeholders available at commissioning, so issues can be addressed quickly without return visits to the facility. Additionally, I would highly recommend installers take good-quality photos of the equipment when it arrives, before it is offloaded from the trucking service, after setting on the pad, and throughout the installation process. Though issues may be rare, sharing photos with the manufacturer can help identify potential problems before the commissioning team arrives on site.” — Rich Law, Sr. Engineer, ESS Technical Solutions (CCI), Sungrow
“Not having a networking plan or strategy prior to arriving to site. For many ESS, the ability to access the system for commissioning, FW updates and troubleshooting is achieved through an internet connection. Residential WiFi networks are often at their weakest in the locations where ESS are being installed. Installers can significantly decrease the commissioning time of systems and later in troubleshooting by ensuring a reliable permanent or temporary network connection is in place day of install.” — Ian Roberts, VP of Product Marketing, Savant
Comments are closed here.