Snake Tray focused on avoiding cable deration and adding American jobs
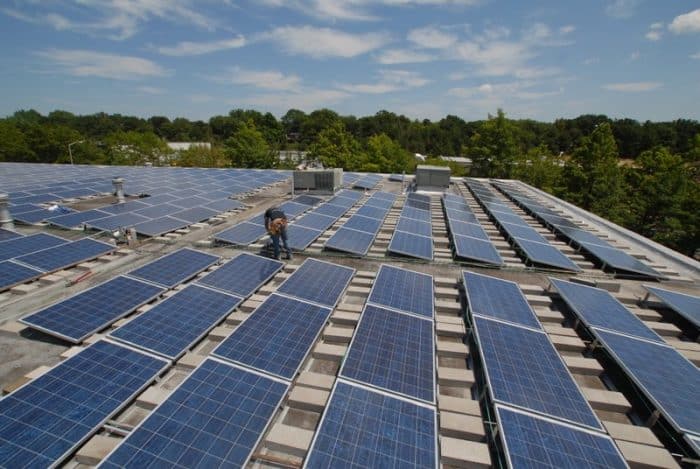
“Domestic content” is all the rage in the U.S. solar industry right now, but solar cable management supplier Snake Tray has been manufacturing in the United States since its inception in 1996.
“We did it for different reasons. I just like the jobs to stay here,” says founder and president Roger Jette. “We believe in making our products in our factory.”
Snake Tray, which now holds more than 35 patents, uses its cable management know-how to avoid cable deration and supply products in four industries, all making up roughly a quarter of its business:
- Transit industry (rail)
- Base building
- IT disciplines (think data centers)
- Solar, battery, EV charging
“We like having the diversification,” Jette says, noting that Snake Tray is “screaming as a factory making this stuff” in 2024.
In this article, we’ll shout out the finer points of Snake Tray’s solar + storage cable management products and Jette’s engineering philosophy, such as avoiding cable deration.
Snake Tray magnifique
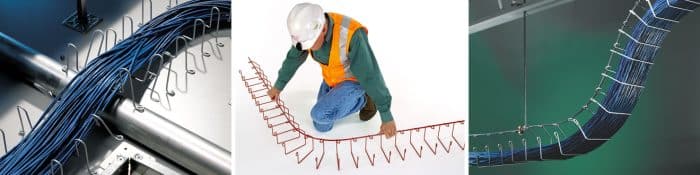
One look at that first Hand-Bendable Cable Tray product, and you understand the company name – ah-ha! Looks like a snake! – but the “tray” is really the key. Consider that:
- Heat buildup in a cable loses electrons.
- Long cables will lose more electrons.
- Larger cables lose fewer electrons.
- Buried or bundled cables will build resistance, create heat and lose electrons.
- DC collection is sensitive to heat.
- AC is subject to the same things but “there are other physical realities in AC that makes it important to keep those cables separated from each other.”
Avoiding closed conduit and keeping cables cool in an open-air design is the core engineering philosophy of Snake Tray. “We have an incredible amount of dielectric strength in our system,” Jette says.
Snake Tray got its start in solar in 2010 when Jette and the team installed a 100 kW rooftop solar system at their headquarters – a project prompted by a New York State rebate available at the time.
“Since we’re an engineering-natured manufacturing company, we engaged this project to engineer and build the solar plant ourselves,” Jette says. “We designed a racking system to hold the panels, we designed the inverter room, and I designed a cable system. Instantly, we knew that it was going to be a product.”
That first tray was aligned with solar PV norms at the time and was rated for 350 circular Mil. In the ensuing decade, everything in solar got bigger: the industry, the solar plants and the cables.
“I designed that 350 model and all of a sudden I’m designing a 750 model,” Jette recalls. “And now we’re shipping jobs at 1,000 circular Mil and our tooling is ready in the event the industry needs at 1,250 circular Mil cables.”
Avoiding cable deration
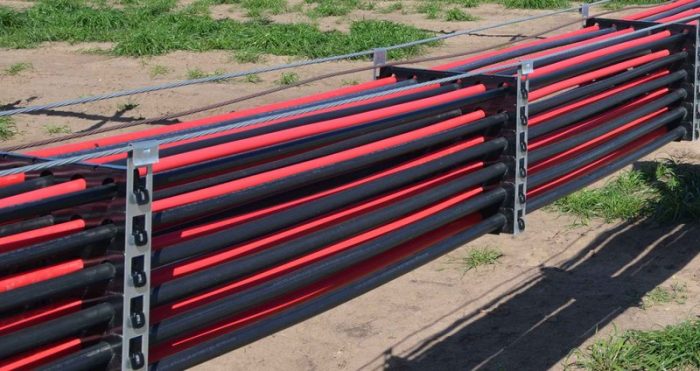
Cable derating is an adjustment made to the current-carrying capacity of electrical cables under specific conditions. These conditions primarily include factors like ambient temperature, cable bundling, and the method of cable installation. The U.S. National Electric Code (NEC), which is focused on fire prevention and heat reduction, includes cable deration to safely keep electrons moving through cool cables.
Snake Tray adds value to projects by avoiding cable deration.
“The investors in these giant programs want to make sure to get a yield, and the best way to get a yield is to keep anything from degrading the yield,” Jette says. “If the cable’s not derated, it will carry more energy, and you can use smaller conductors.”
With Snake Tray, solar contractors can avoid cable deration. They can take a 500 Mil and carry the same energy on a 350. A 750 could be carried on a 500. They do this by keeping cables separate, equally spaced, and above ground (more on that in a second).
The developers or EPCs present a situation that needs a solution, and Snake Tray provides cable management options and the power capabilities based on the reality of the physics and NEC deration table, and then “sends the realities to the people crunching the numbers.”
“Solar plants don’t always produce what the tag says it’s going to produce,” Jette says. “Our research indicates we get 30 Watt hours of additional energy per meter of cable in a plant. Total that up to the size of these projects nearing 1 GW in some cases and Mr. investor is going to be pleased.”
Rise above
Solar plants are moving away from trenching and burying cables, and gravitating toward above-ground cable management systems for a few reasons.
For one, as mentioned earlier, burying a cable traps heat. Keeping cables above ground loses fewer electrons. Secondly, trenching can be expensive, so above-ground cable management can save on costs. There are also safety issues associated with digging and with soil contamination on some sites.
Some sites can’t be trenched at all. “I have customers that say six inches below the top soil is limestone, and trenching can’t be done at all,” Limestone is a very low value piece of real estate. If that low-grade real estate, exposed to the sun, can be converted to yield that’s one reason it instantly goes aboveground.”
Lastly, above ground cables will have fewer issues and allow for easier O&M over the life of a project.
“The trend is there just because the economics are dictating it should be, but it also means all of the connections and hookups are in plain sight,” Jette says. “Failures can happen underground. Above, it can be looked after, maintained. If the plant is compromised it could be rapidly repaired and fixed. A hailstorm in Texas took out a whole lot of panels, but not the cable. Hail versus cable is not a big deal.”
Watt’s next?
The Snake Tray facility is located on Long Island. This is where Jette grew up, where he originally opened Snake Tray in an unused store front (and lived above it). This is where Snake Tray will keep on expanding, but always true to its core principles of:
- Free-air cable management, and
- U.S. manufacturing.
And not necessarily in that order. “We’re just short of 100,000 square feet, and still need more space,” Jette says. ”If we expand, it’ll have to just keep on making the factory bigger. We can do that because we’re a private company. I’m the only stockholder and if I’m happy, I can make it in the United States.”
Comments are closed here.