Start the (re)cycle: Zero-waste solar construction and end-of-life plans
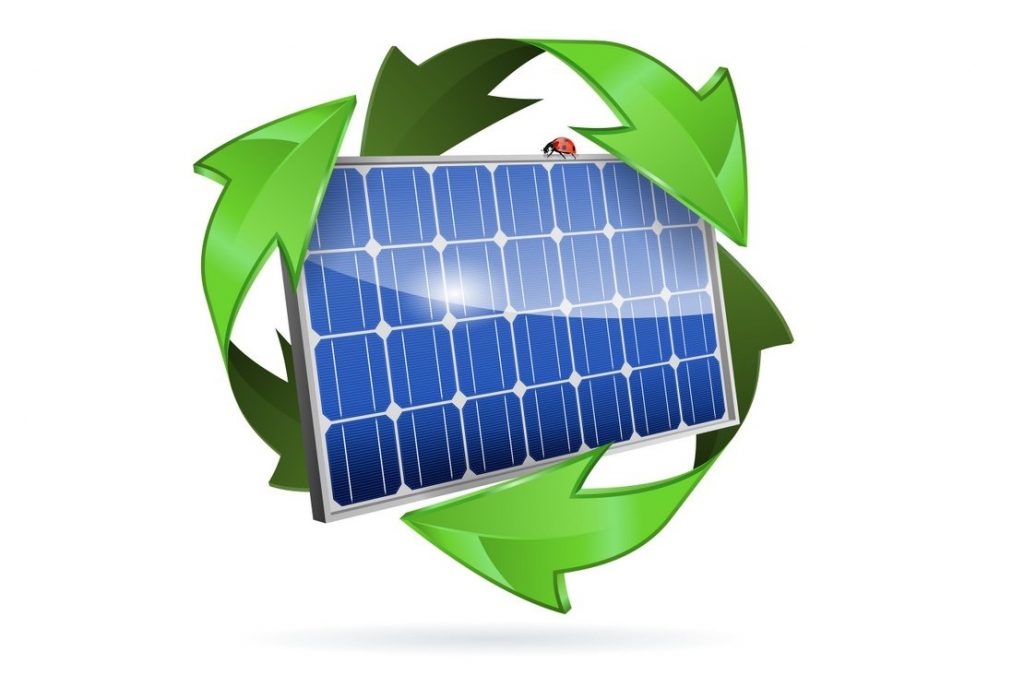
Solar projects aren’t inherently homeruns for the environment in terms of waste. Jobsites are packed with product packaging and leftover material, and, of course, decommissioned panels loom as a landfill crisis down the road. Luckily, solar contractors and developers can overcome these potential issues if they do one thing: Try.
Inovateus Solar is one developer making that effort. In a recent webinar, “Myth Busting Facts About Sustainable Solar Development & Solar Panel Recycling,” Tyler Kanczuzewski, Vice President of Marketing and Sustainability for Inovateus, explained the company’s zero-waste solar construction philosophy. The stuff on-site – wood pallets, cardboard and paper, metal branding, conduit, wire – it is all very recyclable.
“We can sort and separate the waste on site, working with local and regional recycling companies on logistics and recycling over 90 percent of it at no added costs,” he says. “We are learning this adds value to the stakeholders and let’s be honest it’s the right thing to do.”
New solutions are emerging too, like PV Pallet, a reusable pallet made of HDPE plastic that is recyclable over and over.
End of life planning
Having a solid end of life plan in place is just as important as the pre-construction plan. Handling the logistics of removing the equipment and shipping to a recycler is key. Inovateus works with Cascade Eco Minerals, a division of Dlubak Glass, on plans to remove and ship the materials. They also work with the system owner and stakeholder to know if they want new solar or to use the equipment longer because at 25 years it still might be 80 percent efficient.
The panels themselves draw the most scrutiny in terms of recyclability, but the scrutiny has more to do with planning than the panels. Panels today are 95 percent recyclable. The United States, however, is infamously lagging behind Europe, which holds industry accountable for closing the loop. We are in need of a similar federal plan that forces a solution.
Until that fictional day, though, options exist. First Solar is one U.S. manufacturer that recycles its own panels (and we are hosting a webinar with them on April 21 concerning C&I solar design). The PV Cycle Association has tailor-made waste management solutions for solar energy equipment, batteries and e-waste. SEIA continues to build its National Recycling Program with Preferred Recycling Partners. Cascade is one of those partners.
“Solar modules are a great fit for us to develop the process to separate the complex assembly of a PV panel and recycle it,” says Chris Stearns, national sales director, Cascade Eco Minerals, during the webinar. “We get in pallets of modules and evaluate each batch. If there’s a chance of reuse – like a repanelization project where they are upgrading, we can work with those. Those marked for recycling get turned into raw minerals.”
They combine those with other glass waste streams and sell them to manufacturers. An example is glass road beads that are used to make highway lines.
Cascade’s parent company has 500,000 tons of material processing capacity and only 5 percent right now is solar modules. So, they have the capacity and ability to ramp this up when that volume comes.
Recycling does carry a cost. Today, by pound, it costs about $14 to $18 per module, Stearns says. The recycling process is labor intensive and requires a great deal of equipment and expertise. The commodities that the processes yield do have financial value but this value does not exceed the cost of processing. When the volume comes, those prices will come down.
The solar industry can do itself a favor to drive down those costs by committing to recycling as a collective right now, instead of waiting for some federal plan.
“Our business is in volume. We need tons and tons. So if the delineation point is 2006, we still have time before those hit their warranty,” Stearns notes.
Comments are closed here.