LONGi’s HJT solar cell achieves 26.5 percent conversion efficiency
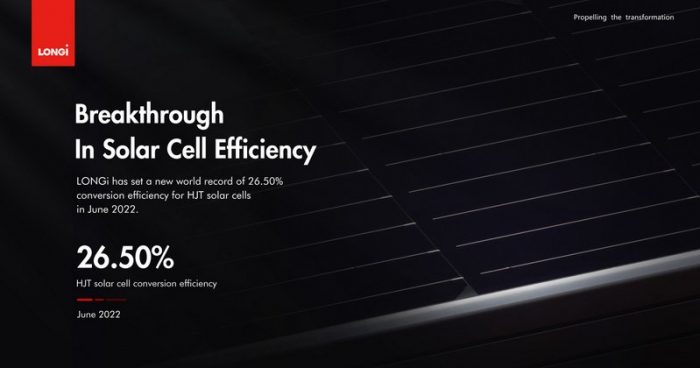
LONGi has announced a new world record conversion efficiency of 26.5% for its silicon heterojunction (HJT) photovoltaic cells. The new record, validated in testing carried out by the Institute for Solar Energy Research (ISFH) in Hamelin, Germany, was achieved on M6 (274.4cm2) full-size monocrystalline silicon wafers, marking a new breakthrough in efficiency for large-size monocrystalline silicon photovoltaic cells.
LONGi has achieved continual breakthroughs in PV conversion efficiencies the last several months, breaking the world record for HJT cell efficiency twice in one week in October 2021:
Only days after setting a new record of 25.82% for the efficiency of its HJT cells, LONGi has announced a new world record of 26.30%. It also represents the world’s highest efficiency for a Front-Back Contact (FBC) solar cell. The new record, as with the previous benchmark, was validated in testing carried out at the German Institut für Solarenergieforschung (ISFH).
The fill factor (FF) of the certified cells breached the threshold of 86%, reaching 86.59% and achieving the world’s highest level for silicon cells. A new process developed by LONGi’s R&D team can effectively reduce the contact resistance of the interface, so as to improve the FF and increase a cell’s current density. The current density presently reaches 40.49mA/cm² on an M6 9BB cell.
We also recently discusses what makes a quality solar module, in general, with LONGi and PVEL on a recent episode of The Pitch:
Crowell: CJ, essentially every year that LONGi has manufactured a module it has been graded a PVEL Top Performer. In terms of production process and quality control assessments, what is LONGi doing behind the scenes to achieve this consistent result?
Fu: We have implemented a lifecycle quality system that covers product design, new material qualification, manufacturing process, third party testing and after-sale service. We invest heavily in R&D to make sure our products and technology is best in class. In the last 10 years, LONGi has invested more than $1.5 billion R&D. We establish the testing capability in-house and conduct extensive testing to verify the quality of our products. Collaboration with third-party labs such as PVEL is a key component of our lifecycle quality system.
Crowell: The LONGi Hi-MO 4, 72-cell bifacial model specifically the LR4-72HBD, was one of only six models out of 121 to be a Top Performer in every single category PVEL measured to give a sense of how hard this is to do. What are some of the variables within that bill of materials (BOM) for instance that if you changed or altered something, how it might affect the final performance of that product?
Fu: The Hi-MO 4 72-cell bifacial double-glass module is a great example of how our lifecycle quality system works. We put many thoughts into product design, material selection and production process to ensure the reliability of our final product. So, one example I’d like to mention is that the module BOM decision between double glass structure and the transparent back sheet. They conducted many rounds of reliability testing for different kinds of transparent back sheets, and test results showed some concerning failures such as yellowing, cracking or delamination. On the other hand, the double glass module showed consistently better performance in the stress tests such as the damp heat and UV test. This data helped us decide to go with the double glass structure, and the decision has been also verified by the excellent results from the PVEL reports.
Comments are closed here.