Ground-Mount Solar Buyer’s Guide 2021: Fixed Tilt and Trackers
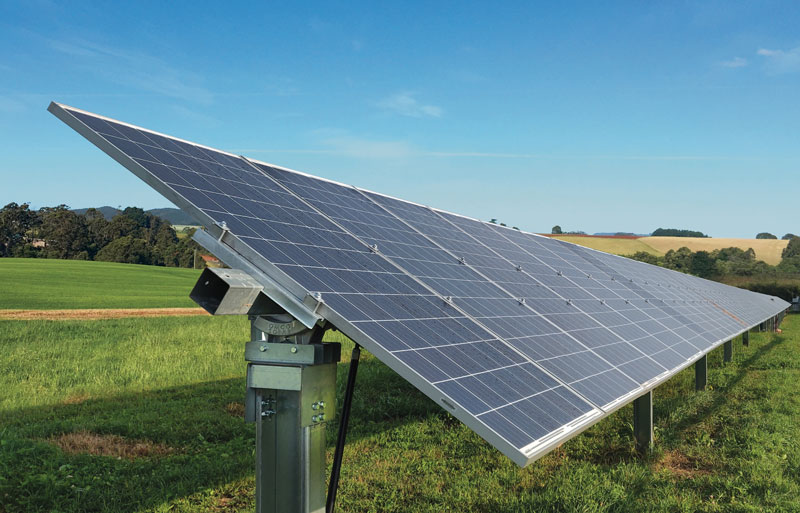
Ground-mount systems are the literal foundation of solar projects, so choosing not just the right product, but the best manufacturer for each site or portfolio is crucial. In our Ground-Mount Buyer’s Guide this year, EPCs and developers building C&I and utility-scale sites can get a snapshot of the fixed tilt products, tracker systems and turnkey services offered by 14 of the top providers. Click on products listed under each company to read more about their design, installation methods and advantages.
OMCO Solar
OMCO Solar is a premier manufacturer of solar racking and tracker solutions for community, commercial & industrial, and utility scale projects. Their expertise in fixed tilt and single-axis tracker systems stems from decades of steel manufacturing, beginning in 1955 when OMCO Holdings was founded. OMCO developed the first American steel fabrication and assembly facility specific to the utility-scale solar market. As a major manufacturer, OMCO has been driving innovation for solar structures and construction for over 20 years.
Origin 2L Bifacial Factory-Direct Tracker
Posts per row: Dependent on soil conditions, type of posts and row length — average is 11 to 13 per row.
Row lengths: While 96 modules per row is most common, OMCO Solar can customize to accommodate up to 112. Unique bearing technology allows long straight rows — 4 strings when others can only mount 3 — fewer motors and controllers per MW.
Slope Tolerances: Up to 15% for a North-South Slope
Design: OMCO Origin 2L (2-in-Landscape) Bifacial Trackers are primarily constructed of galvanized steel and cast aluminum. Bearings include a wear surface composed of a unique long-life, low-friction, self-lubricating acetal blend. A balanced design allows for more accurate targeting and reduced energy consumption. Some subassemblies are factory preassembled and shipped as single units for labor, time and cost savings. The unique bearing adjusts to accommodate post misalignment. OMCO Origin 2L Bifacial Trackers are open on the back — no torque tube blocking the cells — for highest energy production. The height of the tracker is low — like 1-in-portrait trackers — to minimize installation labor. Foundation options include OMCO-produced driven C posts (preferred) and driven I or W posts, and ground screw foundations.
Advantages:
• Factory Preassembled: Some subassemblies are supplied as single, preassembled units for installation labor savings.
• Balanced Design: Axis of rotation at the center of mass of the table — improves targeting accuracy, increases energy production and minimizes energy consumption.
• Long Wear Life: Bearings tested to more than 40 years equivalent life.
• 7 Dimensions of Adjustment: Bearings adjust to accommodate post misalignment, avoiding project delays.
• Over 20% Higher Back Side Production: The open back allows uniform backside irradiance, which is critical for long cell and module life.
• Shortest Lead Times: Partners benefit from expedited delivery due to OMCO Solar’s four strategically located U.S. manufacturing plants. Lead times are typically 8 to 12 weeks.
Domestic Content: OMCO makes all structural components with domestic steel and is well positioned for IRA ITC benefits.
CHOICE Factory-Direct Fixed-Tilt
Number of pieces: 8 Typical Components + Hardware
Certifications: ISO 9001:2015 Standard, UL 2703 Ed. 1, CPP Wind Tunnel-Tested, NEC Compliant
Terrain Articulation: Accommodates up to a 20% grade change
Installation:
- For a pile-driven foundation, posts are driven into the ground.
- Pre-assembled tilt bracket assemblies are bolted onto the piles.
- Lateral beams are then connected by fasteners to the tilt assemblies.
- Modules are secured with fasteners directly onto the beams to provide a secure bond.
Advantages: Pre-Assembled tilt assembly optimizes packaging & shipping, reduces on-site labor requirements, accelerates total build time, and eliminates loose hardware along with third party grounding devices. This in turn accelerates the assembly process. All structural components are manufactured in OMCO Solar’s six U.S. manufacturing plant facilities. With the company’s factory-direct model and domestically sourced supply chain, OMCO Solar consistently delivers quality solar mounting solutions with the shortest lead times in the industry.
Turnkey services:
- On-Site Pile Testing. OMCO can provide customers with pile testing for their solar projects across the United States. This includes a 3rd party stamped report that can be used for foundation design and is a cost-effective alternative to geotechnical reports.
- Engineering Design & Site Optimization. OMCO has an experienced engineering team that can provide customers with stamped construction drawings and calculation packages. We also have the ability to optimize a project design to maximize the benefits of OMCO products.
- Single Point of Contact Contracting Model. OMCO provides fast and efficient delivery of a completed racking solution while minimizing transaction costs and construction delays that are typically associated with the conventional multiple-contract method. Our single point of contact contracting model streamlines the process significantly for customers.
- Buy Direct from the Manufacturer. OMCO has four manufacturing facilities that provide superior customer support from a knowledgeable and experienced team. This also means that OMCO can offer highly competitive pricing and reduced lead-times, which can be challenging for other suppliers.
www.omcosolar.com | Sales: info@omcosolar.com
AP Alternatives
Specialty: 300 kW-30 MW
APA has been in the fixed-tilt solar space since 2008. For the past 13 years, APA has built its reputation on providing the right foundation and racking system for project sites with extreme topography and unfavorable soil conditions. To prove it, APA has completed almost 2GW worth of projects throughout every region in the United States, including islands such as Hawaii and Puerto Rico.
TITAN Series - Driven Pile or Dual Screws
Number of pieces: Titan: 1,154 per MW; Titan Duo 1,130 per MW
Certifications: ASCE 7-10 & CPP Wind Tunnel Tested
Installation: A pile driver installs the pile foundations for TITAN racking. APA screw machines are attached to skid steers to drive the ground screws. With the TITAN Duo, 100 percent pre-drilling is offered to ensure any bedrock or hard obstructions do not cause significant delays during installation. The racking attaches to the foundations and can be adjusted in the field to maintain the proper array height and design.
Advantages: The TITAN’s unique asymmetrical design and innovative features allow for flexibility in the field while streamlining the install process. It has the lowest part count per MW and integrated wire management. The patented Gravity Clip reduces module install time by 35 percent. The 3-rail design is an excellent solution for bifacial modules, providing low backside shading. The TITAN has the industry’s strongest C-pile with opportunities for adjustment. The screws are telescoping providing 18” of adjustability for topography.
Ready Rack Pre-Engineered Kit
Number of pieces: varies for each project – avg. 548 pieces for a 12KW project
Installation: The Ready Rack Pre-Engineered Kit is great for smaller projects and comes in two module increments. The kit has multiple foundation types and provides a solution for all subsurface conditions. It comes with everything needed to install the racking and is delivered on a 4’x12’ pallet. Additionally, there is no need to source any pipes or concrete with this product. The layout and dimensions are site specific and can be easily referenced in the provided plans. The helical and ground screw foundations are simply installed by using a skid steer and auger attachment.
Advantages: Designed specifically for smaller residential and commercial solar installations, it comes with all required components and has approved engineering documentation already completed and included; just pick your parameters and go. The design is a simple configuration that allows contractors to install the system fast. A 10 kW system, for example, can be installed in one day. Integrated features allow for onsite adjustment and anchors paired with quick-install bracing make this simple system extremely robust.
A-Frame Tracker Interface
Three pieces: Ground screw or helical, leveling flange, A-Frame.
Design: The helical piles or ground screws are driven with a rotary head. Then the A-Frame is attached to the piles with four bolts. The A-Frame uses a standard I-beam section to the solar tracker system. This allows seamless transition from driven I-beams to the A-Frames, leaving connection hardware the same. The leveling flanges allow for up to 20 in. of height adjustment to keep the A-Frame plum and level. The dual post design allows for ground screws or micro helicals for the foundation and are driven using a rock drill.
Advantages: The A-Frame advantage is its dual post design, allowing developers to substitute the traditional pile-driven foundation for a dual ground screw or dual helical foundation to accommodate rocky or softer subsurface conditions. The adjustability in the A-Frame also aids in dealing with topography and managing in-field adjustments to maintain the design of the array. Helicals are designed for softer soils, while ground screws are best suited for rocky or harder subsurfaces that have cobbles or other obstructions.
Turnkey specialties:
- APA provides a full turnkey service from installing the foundation to the module installation. Anchor testing is also provided.
- Hardware-only orders, giving customers the exact amount of hardware and foundation pieces they need to complete a project at a competitive price.
- On-site supervisor to assist in the initial stages of construction if the onsite crew is unfamiliar with the installation process or racking system.
apalternatives.com | Sales: melanieg@apalternatives.com
Cantsink
Specialty: 1 to 100 MW
Cantsink offers a variety of products and services for your ground-mounted solar project. In the early stages of your solar project, Cantsink performs pull testing services and w-beam procurement. Their machines drive piles for the site or install helical piles to prevent any foundation failures onsite from heavy solar equipment. Once your project is complete, they can help improve your project’s efficiency with panel cleaning services. Contact us today to help with your next project.
Brilliant Rack
Certifications: UL 2703 Certified
Installation:
- Quickly install up to 14 panels at once with Xpress MountTM technology
- Reduce labor time and costs with preassembled tilt beams and built-in wire management
- Integrated electrical bonding method using serrated nuts and bolts (no WEEBs required)
Advantages:
- Fewer system components and only two standard bolt sizes
- Customizable, three-axis tolerance conforms to site topography
- Seamless installation with any foundation type
Turnkey services:
- Pull Testing
- Providing W Beam Material and Driving Piles
- Helical Pile Installation for Pad Support and other Heavy Equipment Onsite to Prevent Foundation Failures
- Centric Inverter Rack
- Panel Cleaning
www.brilliantrack.com | www.cantsink.com | Sales: dara@cantsink.com
Full Tilt by BCI
Specialty: C&I, DG, utility scale, and community solar in any size range
With over 20GW of solar racking delivered as a contract manufacturer and backed by decades of engineering and global supply chain experience, Full Tilt represents an optimal fixed tilt racking solution. The system boasts an innovative yet straightforward design with fewer parts and rapid installation features along with manufacturer direct pricing.
FULL TILT by BCI
Number of pieces: 6
Certifications: UL 2703
Average 20-module table construction time: 22 minutes (two-person crew)
Slope Tolerance: Can accommodate up to 21% E-W slope
Installation: The pre-galvanized roll formed sections are lightweight and can be handled by two installers. The rafter features a pivot point near the center of gravity, allowing the structure and loading of the modules in the flat position. Piles are driven with a pile driver, preferably a vibratory type. The balance of the system can be installed by hand with a 2-to-4-person crew using simple hand tools, battery powered tools speed up the assembly. Once the piles are driven and the components are properly staged, a 20-module table can be fully assembled in less-than one man-hour.
Advantages: The Full Tilt system has many cost and labor saving features, and one the installers gravitate towards is the “Longhorn” panel rails that keep the modules perfectly aligned for quick fastening. The assemblers need not waste time adjusting the modules, alignment is automatically perfect. Another big advantage of the Full Tilt system is that it is designed to be built in the flat position. This means that all components can be assembled at a safe working height without need for ladders or workers climbing the structure. After the structure is assembled and panels fastened, the complete structure is easily and safely rotated to final position.
Turnkey specialties:
- Design & Engineering – From layouts and site design specifications to member size optimization, Full Tilt’s team is ready to adapt its racking solution to meet the unique challenges of any site.
- Manufacturing and Supply Chain – BCI provides customers with a complete and comprehensive support network that they can rely on when it comes to ensuring material is delivered to site on time.
- Installation support – Field support as well as an extensive network of trusted installers and industry partners to ensure a successful installation.
www.full-tilt.com | Sales: tim.fish@bci-engineering.com
IronRidge
IronRidge, an Esdec company, designs and manufactures structural hardware for residential and commercial solar systems. For nearly a quarter of a century, we have worked closely with solar professionals to build strong, streamlined, and cost-effective products. IronRidge is NSF Certified to ISO 9001, maintaining the highest of quality management standards.
XR Ground Mount System
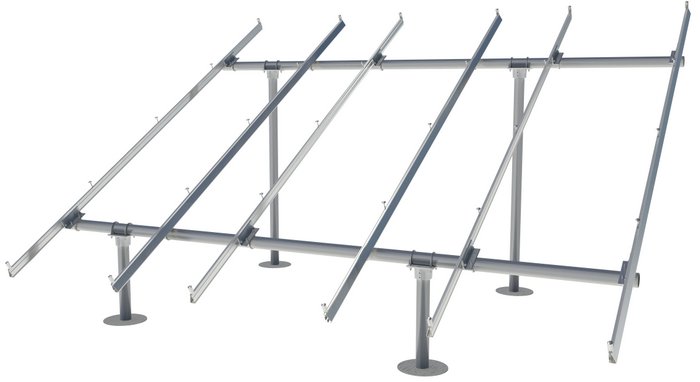
Number of pieces: Variable
Tools needed: Post Hole Digger or Powered Auger; Socket Drive (7/16”, 9/16”, and 1/2” Sockets); Torque Wrenches (0-240 in-lbs and 10-40 ft-lbs); Transit, String Line, or Laser Level; 3/16” Allen Head
Certifications: UL 2703 Listed, Designed and Certified for Compliance with the International Building Code & ASCE/SEI-7
Installation: 1. Build the base 2. Connect the substructure 3. Place rails 4. Secure lugs 5. Secure modules
Advantages: The IronRidge Ground Mount System combines our XR100 or XR1000 rails with locally-sourced steel pipes or mechanical tubing, to create a cost-effective structure capable of handling any site or terrain challenge. Installation is simple with only a few structural components and no drilling, welding, or heavy machinery required. In addition, the system works with a variety of foundation options, including concrete piers and driven piles. Compatible with soil classes 2-4.
www.ironridge.com | Sales contact | Distribution list
RBI Solar
RBI Solar Inc, a Gibraltar Industries Company, is a market leading provider of solar mounting systems. RBI designs, engineers, manufactures and installs solar mounting systems for commercial and utility scale projects, specializing in fixed-tilt ground mount, carport, ballasted landfill, roof mount and garage canopy solar systems. As part of Gibraltar’s Renewable Energy group, RBI is joined to empower results. In merging strengths from market leaders like TerraSmart, RBI Solar, and SolarBOS; combined with smart new project design software from Sunfig, we are able to serve all sectors in the growing utility, community, and C&I solar market, helping make solar energy readily available anywhere.
RP Construction Services, Inc. (RPCS)
Specialty: Projects of all sizes, 20-50 MW sweet spot
RP Construction Services, Inc. (RPCS) provides turnkey design, structural engineering, procurement/supply, mechanical installation, and specialty services to EPCs, developers, and municipal utilities. As the nation’s leading contractor and Array Technologies single-axis tracker expert, RPCS has completed more than 700 projects, totaling over 2GW, and helps customers meet their renewable energy goals with simple, seamless project execution. RPCS has approximately 300 employees and is headquartered in Monterey, California, and maintains facilities in California, Mississippi, and Kansas.
Turnkey services:
- Design/Engineering – RPCS optimizes the full potential of your project with foundation design and layout, geotechnical site assessment support, tracker and foundation post supply and logistics, and solar tracker technical expertise.
- Supply/Procurement – RPCS offers in-house stocking services with facilities in California, Mississippi, and Kansas with more than 1GW in annual supply. This allows RPCS to control the delivery schedule and material accuracy, quote engineer, and deliver orders quickly.
- Mechanical Installation – RPCS is a fully-licensed mechanical and electrical contractor, self-performing work across the country.
- Kitting – RPCS is the first contractor in the utility space to pre-kit the Array tracker, allowing work that would otherwise be done onsite to be done in a controlled environment at an RPCS facility.
- Additional Construction Services –RPCS offers on-site project management, commissioning, QA/QC, and O&M services.
Solar FlexRack
Specialty: Commercial and utility-scale / 1-100+ MW
Solar FlexRack, a division of Northern States Metals, is an integrated solar company that offers custom-designed, fixed tilt ground mount and single-axis solar tracking systems in the commercial and utility-scale solar mounting industries. Solar FlexRack also offers project support services, including engineering, geotechnical, load testing, field, layout, and installation services to address the actual site conditions of an installation and provide integrated services from design to delivery and installation. Solar FlexRack has completed over 2.5 GW of solar racking installations in 40 states across America and five countries globally.
Fixed Tilt Series G3-X
Installation: Solar FlexRack Series G3-X Ground Mount Rack installs quickly, features similar-sized hardware and requires only standard tools and equipment for assembly. The system is easily staged on job sites and can be assembled in a logical, step-by-step manner in the field by crews of any skill level. With best-in-class engineering, the G3-X has unique design attributes that ensure ease of installation. The system’s lateral bracing stabilizes and perfectly squares the racking system, so modules easily slide into place for fast, safe, and easy module installation. While mostly pre-assembled, the horizontal rail bracket allows racking to be held in place while aligning rows with terrain. The G3-X can be easily assembled on site or can be delivered partially pre-assembled.
Advantages: Solar FlexRack prioritizes module structural integrity with its racking design, and keeps modules in prime condition through construction and beyond. The G3-X Series is a robust, efficient and low component design that installs quickly and easily. It is compatible with all foundation solutions and comes with automatic system squaring, lateral bracing, horizontal rail brackets, and slotted connections for ease of installation. It also allows for safe and quick module mounting with a direct bolt bonded connection. The G3-X leverages the company’s field-proven install base of over 3 GW to deliver the highest quality, pre- or field-assembled ground mount systems that accommodate up to 20% slopes for reduced civil costs.
Certifications: UL 2703 (Issue 2)
Fixed Tilt B Series Ballasted (Cast In Place or Pre-Cast)
Installation: SolarFlexRack’s Ground Mount Fixed Tilt B Series (Ballasted) solution is available with blocks pre-cast offsite or cast-in-place (CIP) on site utilizing Solar FlexRack’s unique, easy to assemble form system. The CIP solution requires only six screws for form assembly, which can be complete in under three minutes with two people. Watch the video of how easy CIP is assembled.
Advantages: Conveniently available with blocks pre-cast or cast-in-place to meet each project’s unique needs, Solar FlexRack’s Ground Mount Fixed Tilt B Series (Ballasted) solutions are well-suited for landfills and challenging terrain sites. The FlexRack Series B pre-cast solution makes use of a two-support system that transfers loads into the block through double the supports for reduced block thickness, as well as enables the use of a split block system, which requires lighter lifting machinery to accommodate sites with low bearing pressure requirements. The cast-in system allows for quick assembly and adjustability, reducing overall labor costs.
Certifications: UL 2703 (Issue 2), ISO 9001
TDP 2.0 Solar Tracker with BalanceTrac
- Row lengths: Up to 90 modules per independent table
- Slope tolerances: Up to 10% North-South slope tolerance
- Certifications: UL 2703
Construction: Independently driven; single-axis horizontal, distributed drive. Drive type: Slew. No special tools required. Any tools needed could be acquired at your local hardware store.
Advantages: Solar FlexRack’s reliable TDP 2.0 Solar Tracker with BalanceTrac bundles an advanced tracker design with top-tier engineering and project support services to safeguard solar projects from unexpected costs. One of the easiest trackers to install, TDP 2.0 features smart backtracking to reduce row shading & maximize energy yield. The TDP 2.0 has an increased table size to provide optimal module density as well as compatibility with 1,000V and 1,500V modules. In order to enable greater adjustability to maximize system performance, the TDP 2.0 features a rotational range of 110° (± 55°) and ground clearance that allows for shorter piles.
TDP 1.0 Solar Tracker
- Row lengths: Up to 60 modules per independent table
- Slope tolerances: Up to 10% North-South slope tolerances
- Certifications: UL 2703
- Design: Single-axis, horizontal, distributed drive
- Drive type: linear actuator
Advantages: Field-proven with over 75 projects installed in North America, Solar FlexRack’s TDP 1.0 Solar Tracker leverages a simple, efficient design for highly reliable and easy installations. Ideal for smaller or highly irregular layouts, the TDP 1.0’s small drive block enables up to 40% reduction in land use. The TDP 1.0 also utilizes a distributed drive and has no mechanical components between rows, allowing for easy and cost effective access for mowers, cleaning services and other project maintenance. Complete with Solar FlexRack’s full spectrum engineering and project support services, the TDP 1.0 features smart backtracking to reduce shading across rows and maximize energy yield.
solarflexrack.com | Sales: sdaniel@solarflexrack.com
Soltec Power Holdings
Soltec Power Holdings specialized in integrated solar photovoltaic solutions, whose business is focused on solar tracking systems with a strong commitment to innovation. Soltec is positioned as the world’s third leading company in the market among solar tracker suppliers, and the first worldwide excluding the American market, as well as in Mexico and Argentina. With headquarters in Spain, Soltec Power Holdings has been operating since 2004 and has a diversified geographic presence focused on Spain, North America and Latin America. It has presence in 16 countries with more than 1,300 employees.
SF7 USA
Mounting tolerances: Range from 20 to 40 inches. Can be installed on slopes of up to 17%.
Installation: Soltec pre-assembles most components, so the installation includes few steps. Locating the parts and pieces needed at each step is quick. All of this results in substantial savings in both time and financial resources.
Design: The tracker features an electronic system that incorporates wireless communication designed to withstand low temperatures.
Software: TeamTrack system delivers up to 6.8% more yield, a function that minimizes shading losses between rows, especially on uneven terrain. Diffuse Booster technology allows for optimal energy generation, even on cloudy days, by capturing diffuse radiation. Dy-WIND methodology, solar tracker response to wind is ensured, preventing damage to the plant during heavy precipitation.
soltec.com | Sales: sales@soltec.com
Sollega
Unique compared to the rest in this section, Sollega provides one racking system that can go from the commercial rooftop to the ground. The universal design, manufactured from UV rated glass reinforced Nylon 6, enables the installation of all framed modules and stands up especially well in highly corrosive conditions near the ocean. Injection molded in California, 100 percent made in the USA.
www.sollega.com | Sales: Info@sollega.com
Sunfolding
Specialty: Projects above 5 MW, especially those that can benefit from earthwork savings
Sunfolding maximizes profitability with innovative solar tracking technology. Powered by air, the Sunfolding T29 Single-Axis Tracker deploys on land previously off limits to utility-scale solar. The Sunfolding T29 also makes solar plants faster to install and easier to operate. Sunfolding has won recognition as a 2020 Global Cleantech 100 Company and a 2019 Bloomberg New Energy Pioneer. Headquartered in Alameda, CA, Sunfolding ships US-manufactured trackers throughout North America.
Sunfolding T29 Single Axis Tracker
Number of pieces: 3 structural components
Row lengths: 1 to 2 strings in length
Slope tolerances: Up to 12.3% grade slopes with no change to standard product
Design: With just three unique structural components, Sunfolding makes construction easier. From the post all the way to the modules, we streamline and expedite the installation process. By reducing the number of post sizes that you’re dealing with, we have reduced the possibilities of misplacing a post or misdriving a post. With a shorter post embedment depth, Sunfolding minimizes interaction and contact with subgrade rock.
Advantages: The Sunfolding T29 optimizes solar tracking and maximizes energy output. Unlike motor-driven trackers, the Sunfolding T29 makes solar infrastructure simple again. Sunfolding projects neutralize costs with flexible layouts that fit the trackers to the land. Small tracker tables enable denser DC per acre without driving up costs and reduce earthwork by more than 70%. Fewer components makes every project simpler and allows for a reduction in construction costs by more than 15%.
Turnkey services: Sunfolding provides turnkey installations for projects using the Sunfolding T29 Single-Axis Tracker through the Sunfolding Construction Network (SCN). From engineered site layouts to mechanical installations, SCN delivers optimal quality, scheduling, and cost. SCN’s network of mechanical subcontractors use extensive product knowledge for improved labor productivity and on-site logistics.
sunfolding.com | Sales: sales@sunfolding.com
SunModo
Specialty: residential and C&I <500 kW
SunModo, meaning “the way of the sun,” is a private U.S. company headquartered in Vancouver, Wash., that is focused on innovative racking and mounting solutions for professional installers in the fast-growing solar industry. Our commitment to innovation can be seen across our entire product line, which includes 20 plus industry-shaping patents. From residential rooftops to large-scale ground-mounts and everything in between, SunModo has the most comprehensive solar mounting and racking solutions.
SunTurf Ground Mount
Average row construction time: 4LX12 array 20K system installed within 1 day (10am-2pm)
Slope tolerance: Up to 27% slope east-west.
Certifications: UL 2703
Installation: No cutting, welding, or drilling. Adjust height and install posts with set screws. Pipe fittings attach quickly with set screws. Two-piece pipe caps make installation easy. Structural splice with set screws for bonding. Fast rail attachment with T-bolts. The SunTurf Ground Mount System easily integrates Helio Rails with Schedule 40 Steel Pipes. Combine SunTurf with SunModo Ground Screws or Augers and do a complete install of a 15-kW system with only one day on the job site. For a more interactive look at SunModo’s Ground Mount, check out this video.
Advantages: SunModo offers the next generation SunTurf Ground Mount System. The streamlined design combines the simplicity of a pipe-based system with next-level engineering. SurTurf Ground Mount is ideal for solar installers looking for a low cost high performance system that can accommodate a wide variety of soil conditions. No drilling is required to attach the aluminum rails to the horizontal pipe. The innovative swivel pipe cap kit can accommodate terrains up to 27% slope east-west and 120% slope north-south.
www.sunmodo.com | Sales: sales@sunmod.com
TerraSmart
Specialties:
- Utility-Scale ground mount: 20 – 300 MW
- Single-Axis Tracker: 20 – 100 MW
TerraSmart, a Gibraltar Industries company, has been a front-runner in the solar industry for 11 years by continuously evolving its turnkey business model to build over 3.5 GW’s of ground mounted, utility-scale solar projects across the U.S. As part of Gibraltar’s Renewable Energy group, we are joined to empower results. In merging strengths from market leaders like TerraSmart, RBI Solar, and SolarBOS; combined with smart new project design software from Sunfig, we are able to serve all sectors in the growing utility, community, and C&I solar market, helping make solar energy readily available anywhere.
TerraBOS Flex
Material: Combiner box, wire harness, source circuit
Basics: Complete eBOS solution for sites leveraging the unmatched flexibility of the Home Run architecture. TerraBOS Flex is a full eBOS solution from wire to combiner boxes. All components are pre-fabricated and customized to project specs, making in-field installation faster, easier, and more reliable. Factory assembled for quality control; TerraBOS Flex is customizable at scale.
Key features: Fully integrated and customizable source circuit cabling, harnesses, and DC Combiner Boxes drive high reliability and improved installation vs field fabricated or piecemealed solutions.
- Reduce installation costs with a pre-fabricated solution that allows for fast plug-and-play connections in the field
- Flexible design to work with wire hangers, cable trays, and trenching solutions
- Factory assembled in a quality-controlled environment, ensuring long term reliability
- Diagnose issues at the box level for faster troubleshooting and less downtime
- The use of whips, jumpers, and pre-installed mounting hardware reduces time on site
- Thorough quality process and testing ensures long term reliability
- 8.5+ GW of eBOS deployed across the U.S.
- Our customer focused, value engineered designs save you time and money
Installation explained: The TerrasBOS Flex homerun system can be designed around any site configuration. Its design is adaptable to work with wire hangers, cable trays, and trenching.
GLIDE Agile
Number of pieces: 7 Superstructure Beam Members (above the vertical leg)
Certifications: UL2703, Edition 1; CPP Wind Tunnel Tested
Installation: Our adjustable and durable frame features less hardware, integrated electrical bonding, and included wire management resulting in reduced labor hours. Installation times are shortened by up to 36% through simplified connections, agile parts, and seasoned field teams. Compatible with ground screws that will eliminate refusal risk, increase install efficiency, and make projects more predictable. With one of the most experienced field teams in the industry, we have priceless insights that allow us to overcome challenges and streamline processes to ensure projects are completed on time.
Advantages: With a slope tolerance of 36%, our racking can accommodate high slopes and undulating terrain. Landscape orientation is bifacial compatible to maximize potential backside power yield. Durable mechanics can tolerate wind speeds up to 170 mph and 100 PSF ground snow loads. Our seasoned field team prioritizes accuracy, safety, and efficiency. Foundation consultation from an unbiased partner, based on your unique project site. No matter the terrain or weather, we’ll provide the right solution. Our versatile design enables numerous configurations allowing us to meet your unique needs and bring solar to more fields.
GLIDE Wave
Number of pieces: 7 (1 foundation, 6 racking components & bracket assemblies)
Certifications: UL2703, Wind Tunnel Tested
Installation: Engineered with flexibility in mind, the design incorporates continuous rows to mitigate topographic changes and minimize the number of foundations required. The system can be altered to multiple foundation options, with the base option being driven piers. Proprietary electrical bonding is integrated into the racking system, as well as other solutions for wire management. Pre-assembled parts reduce the number of connections required to be made in the field, minimizing Installation time.
Advantages: The standard engineering of the system is designed to accommodate slopes up to 15%. With several GW deployed across all 50 states, the system is durable and robust enough to accommodate the heavy snow loads in the Northeast, along with the high wind speeds of Hawaii. Our team of professional designers, licensed engineers, and dedicated project management collaborates to ensure projects are delivered in an effective manner and able to operate efficiently. We design each system to site specific environments, helping our partners to maximize the return value on each opportunity.
GLIDE Fuse
Number of pieces: 7 (2 foundations, 5 racking components & bracket assemblies)
Certifications: UL2703, Wind Tunnel Tested
Installation: Designed with a low tilt and clearance, the dual foundation design supports a higher number of PV modules per foundation than standard fixed-tilt systems. The low clearance makes for easier access to assemble components, all of which contain one bolt size. Components are shipped to site pre-assembled, requiring less hours for assembly in the field.
Advantages: For flat sites with low wind and snow loads, this system helps to maximize the PV output with a high ground coverage ratio (GCR). The low tilt and low clearance of the structure reduces row spacing, allowing for more PV modules to be deployed in a given area. The number of racking components is also reduced, reducing the installation time required to assemble the structure. A proprietary design in the components bonds the system, helping make wire management less intrusive.
Carports
Surface lot canopy, Garage canopy
Product description: Terrasmart offers a variety of canopy structures to accommodate any parking surface including longspan, inverted, perimeter and aisle structures. Our structures and foundations are engineered for environmental loading and any subsurface/soil conditions. Accessory options such as water management, snow guards, facia trim, and multiple coating options are available. A big part of our value is our ability to work with our customers on the conceptual design phase to ensure the best possible system is designed for each project and budget.
Construction process: Pre-construction design identifies risk up front for smooth project planning. Smart scheduling and through bolt connections result in less disruptions on site and faster installation time. We’ll work with you to ensure installation is phased in the most efficient way possible.
Differentiator: Terrasmart provides a single source for design, engineering, manufacturing, and installation. With projects covering most of the U.S., we’ve completed projects from Massachusetts to Hawaii. Terrasmart has deployed over 270 MW of canopy systems ranging from 100 kW up to 14.8 MW. With over a decade of projects on the books, we have a long track record of delivering projects at every scale — on time and on budget.
Turnkey services
- Design & Engineering. A seasoned team of geotechnical, structural, mechanical, electrical and civil engineers provides project-specific, value-engineered solutions that will streamline your next ground mount project experience.
- Turnkey Construction. TerraSmart’s full-service construction team can bring all critical aspects of solar construction in-house. Our full-time employees specialize in professional surveying, civil construction, drilling, screw, racking and panel installation.
- Surveying. Site Topology & 3D Mapping is available via High Precision Aerial Site Mapping. Also, the first of its kind – TerraSmart’s Autonomous Precision Survey Rover (APSR) triples the survey speed and accuracy on your next site.
- Manufacturing. TerraSmart has a 70,000 square-foot manufacturing facility that shortens cycle times and improves production velocity to shorten lead time and service greater product demand.
- Civil. TerraCivil is TerraSmart’s civil construction division that was added recently to incorporate services such as fencing, building access roads, clearing destumping, grading, earthwork, storm drainage, site fencing and more.
www.terrasmart.com | Sales: alommano@terrasmart.com
Trina Solar
Specialty: Tracking systems 10+MW.
Trina is a world-leader in global solar module manufacturing with decades of technological expertise and bankable experience. As an all-in-one smart solar solution, TrinaPro designs an optimal system and then combines industry-leading components with intelligent O&M services to ensure utility-scale solar project value. The TrinaPro portfolio has two tracker products: Agile 1P and Vanguard 2P.
Agile 1P
- Number of pieces: Up to 120 modules per tracker
- Posts per row: 9
- Row lengths: 72 meters
- Slope tolerances: 20% N/S, 10% E/W
- Certifications: UL, IEC
Agile 1P is a one in portrait dual-row single axis tracker. There are two slewing drives on each row connected by cardan transmission bar, both rows share one motor and one controller. Agile 1P utilizes W pile as its foundation along with patented spherical bearings and highly reliable square torque tube Additionally, Agile 1P features TrinaClamp for fast reliable installation and lower BOS/CAPEX.
The construction starts with driving the piles, installing the bearing supports, bearing housing and torque tubes. Adjustments can be made prior to applying the torque and if re-adjustment is needed, it can be done. The next step is installing the joining clamps to connect the torque tubes. After that, the drive system is installed. This consists of a front support between the piles, the transmission lever, the push / pull bar, and the linear actuator. After that the purlins and modules are installed, then the TCU, self-powered panel and grounding strap.
Advantages:
- Features industry leading ±60°tracking range and higher resultant energy output
- Capable of installing up to 120 modules per tracker
- Capable of withstanding higher critical wind speed and reducing aeroelastic effect on trackers
- Capable of providing more energy gain by including SuperTrack Algorithm
- Capable of mitigating extreme weather such as wind, snow, hail and flood
Vanguard 2P
- Number of pieces: Up to 120 modules per tracker
- Posts per row: 7
- Row lengths: 68 meters
- Slope tolerances: 15% N/S
- Certifications: UL, IEC
Vanguard 2P is a two in portrait independent single axis tracker. The newly designed tracker features an innovative multidrive system comprising of three linear actuators connected by cardan transmission bar. Vanguard 2P utilizes W pile as its foundation along with patented spherical bearings and highly reliable square torque tube. Additionally, Vanguard 2P uses reinforced purlins to optimize layouts with the new Trina Solar 600W+ large format modules.
The construction starts with driving the piles, installing the bearing supports, linear actuator supports, bearing housing/ lever /torque tube pre-assembly. Pre-assembly is an assembly of several components pre-assembled on the ground and installed on the structure for a more efficient installation process. Each project site will have different pre-assemblies for different sections of the tracker. The install manual and construction sequence documents will be project specific and optimized for an easier installation process. Adjustments can be made prior to applying the torque and if re-adjustment is needed, it can be done.
The next step is installing the linear actuator in the specified positions, and then the joining clamps to connect the torque tubes. After that, the transmission system supports are installed on the torque tubes. Following that, the transmission bar and cardon are installed. After that the purlins pre-assembly is prepared and installed before installing the modules. Then the TCU, self-powered panel and grounding strap.
Advantages:
- Features 2P tracker industry leading ±55°tracking range and higher resultant energy output
- Capable of installing up to 120 modules per tracker
- Capable of adapting to more challenging terrain with fewer pile design
- Capable of withstanding higher critical wind speed and reducing aeroelastic effect on trackers by multidrive system
- Capable of providing more energy gain by including SuperTrack Algorithm
- Capable of mitigating extreme weather such as wind, hail and flood
- Easier for O&M vehicle’s accessibility
Turnkey services:
- TrinaPro features single-point-of-contact and vendor for major component supplies (foundation, fixed racking or tracker, inverters, modules)
- Support during the entire lifecycle of the project (design engineering, delivery, construction, commissioning, and O&M). Highest bankability rating in the global PV industry for long-term commitment to partnerships
- Component compatibility and design optimization focused on increasing power production and reducing LCOE
- Global supply chain to improve component delivery schedule and meet project deadlines
- Specific custom design engineering meeting each project’s exacting requirements
www.trinasolar.com/us/contact-us | Sales: sales@trinasolar.com
Comments are closed here.