Check for battery thermal runaway risk in the DNV Battery Scorecard (yes, even LFP batteries)
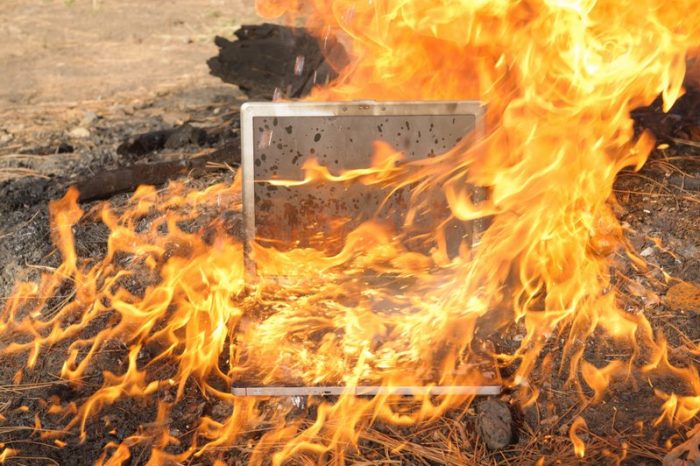
Independent energy expert and assurance provider DNV released the fourth edition of its Battery Scorecard report, to put a spotlight on the most pressing battery questions, including safety, useful life, and degradation. Our big takeaway is from the thermal runaway testing.
While batteries have been commercially available for decades, most stationary storage products are less than five years old. The Battery Scorecard provides project developers and owners data and insights that can help them select the correct technologies for the unique conditions of their projects.
“As energy storage further penetrates energy markets and infrastructure, proven safety and overall performance will become essential to projects. The best and most accurate way to ensure performance and safety is through testing,” said Richard S. Barnes, region president, Energy Systems North America at DNV. “Battery systems aren’t worth installing if they can’t be run safely and reliably.”
This edition of the Battery Scorecard incorporates independent testing results from 19 different battery cell types across the following categories:
- Cell manufacturing volume
- Cell performance: <2-hour grid support services
- Cell performance: 4-hour solar shifting
- Cell performance: high-power vehicle application
- Calendar fade
- Battery management system optimization
- Safety: off-gas and thermal runaway temperature thresholds
- Safety: off-gas composition
Key takeaway
Pay close attention to the thermal runaway testing. The commonly heard refrain is that lithium-ion batteries with NMC chemistry is at a higher risk of thermal runaway compared to LFP chemistry. Overall the risks are lower, but the DNV testing shows that where those LFP batteries come from matters. The real test is the differential between venting and thermal runaway temperatures, according to the authors.
Two temperatures are most important when considering thermal runaway. The first is the cell venting temperature, or the temperature at which the buildup of gases within the cell are released through the cell’s pressure release vent to avoid rupturing the cell’s casing. The second temperature is the onset temperature at which thermal runaway occurs.
This is the “point of no return” for the cell, where uncontrollable self-propagating reactions involved in thermal runaway begin. While cells may ultimately reach temperatures as high as 1000 °C, the temperature at which these reactions begin helps determine monitoring and control mechanisms needed to avoid thermal runaway altogether. While venting and thermal runaway of an isolated cell is concerning by itself, a key design and control mechanism within battery systems lies in preventing cascading effects of one cell’s thermal runaway causing other cells to also reach thermal runaway.
This chart from the report shows how vastly different venting and thermal runaway onset temperatures can vary from both NMC to LFP and LFP to LFP.
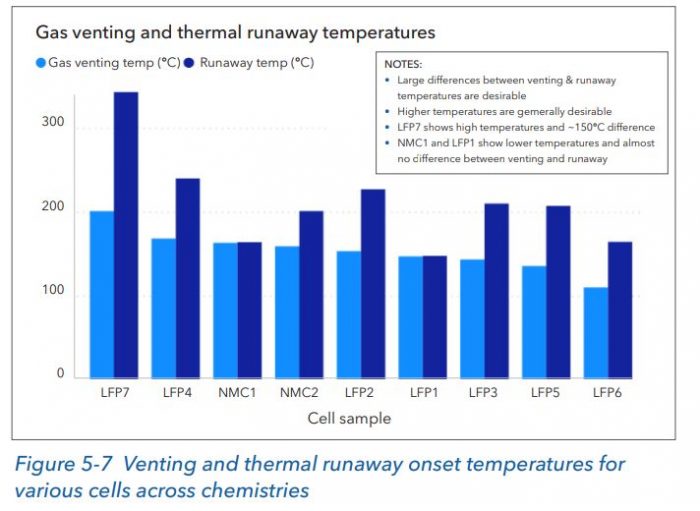
This data from UL 9540A cell-level tests had thermal runaway initiated using a standard repeatable methodology. It is generally considered favorable to have a higher degree of separation between the gas venting and thermal runaway onset temperatures, especially if gas detection is available within the energy storage system.
If gas is detected early, there is more time to catch an overheating cell and prevent thermal runaway from occurring altogether. If the venting and runaway temperatures are closer together, there is less time available to prevent thermal runaway using gas detection. In addition, higher thermal runaway temperatures are better: this means relatively more energy is needed for the cell to reach that temperature and go into runaway.
When evaluating and selecting suitable technology suppliers, DNV recommends that project developers take the following steps to ensure project success:
Start with the cell. Battery energy storage systems all have battery cells as their core component, which dictate performance, safety, and cost. Find out who manufactures the cell (if different from the system integrator), and how long that cell has been in production.
Evaluate total deployments of cells and systems. Total deployments of the underlying battery cell and the integrated system are both good indicators of how reliable the product will be. There are often many bugs to work through after product launch. More experience in the field often leads to improved products.
Request the “Bankability Report”. Independent vetting of the integrated system is critical to make an informed decision. Battery manufacturers should have Bankability Reports on their products and should be excited to share these with potential customers to prove their commitment to transparency.
Request independent test data to validate performance, warranty claims, and safety. Testing provides validation of each product’s design, operation, and safety. Independent testing verifies that the product will operate as specified without manufacturer intervention. DNV recommends requesting independent test data from all battery suppliers before making a purchasing decision to better understand the product and its impact on your energy storage project or EV application.
Comments are closed here.