Automating solar project construction with pile driver technology
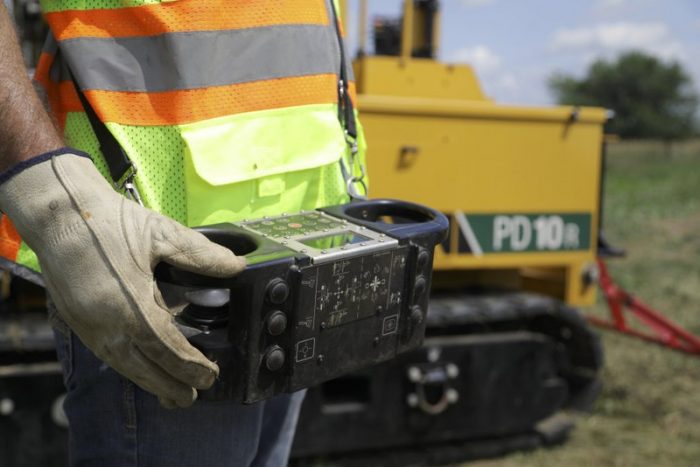
Demand for new solar projects is high, and skilled labor availability is low. So, adding automation to the solar construction process is critical. Enlisting equipment that requires less operator input and support labor can help crews maintain high production rates throughout the construction process.
Vermeer has developed new onboard technology to help make the time-consuming and labor-intensive application of driving piles more automated.
“The Vermeer PTP system helps minimize the number of manual steps involved with positioning and aligning the pile driver on solar projects,” said Bo Howell, product specialist at Vermeer. “Throughout the course of a normal day, where many rows of piles are being installed, PTP technology can help operators maintain precise accuracy and work more efficiently.”
The point-to-point system allows PD10R pile drivers to reposition themselves automatically using onboard GPS. After one pile is driven, the operator presses a button on the remote control, and the pile driver travels to the next coordinate and aligns to go to the next pile. This technology helps minimize the number of steps required from the operator during the pile driving process on solar construction projects.
How it works
A GPS-equipped Vermeer pile driver helps crews work more efficiently on solar projects and maximize accuracy. Operators are required to manually position the pile driver near the location where the pile needs to be installed. But then the onboard GPS takes over the process of precisely aligning the pile vertically and horizontally using auto plumb and auto-target integration between the GPS and Vermeer pile driver technology. From there, the crew loads the post into the guides, and then manually engages the hammer. Once the pile is at the desired height, the hammer automatically disengages, and the GPS logs the data.
After that, the operator lifts the hammer, retracts the mast from the post and navigates the machine to the next target. “All this can be done using joysticks and a few button pushes,” said Howell. “It’s not time consuming or labor intensive, but it does demand a lot of operator input and attention to do this type of work for several hours a day.”
A Vermeer PD10R using PTP technology minimizes the number of operator input steps from 11 to 4 per cycle. “The pile driver can automatically perform seven machine functions that used to require manual input,” said Howell. “This helps keep operators and crews working efficiently and minimizes the number of laborers required to load piles throughout the process.”
With the point-to-point system, the machine automatically navigates to the next pile location, aligns the mast vertically and horizontally, then lowers the hammer so the next pile can be lifted and loaded. The operator then raises the hammer with the push of a button and places the pile in the machine’s guide. From there, the push of a button engages the hammer floats. When the pile is at the desired height, the PD10R automatically starts and stops the hammer.
Once a pile is driven, a single button push raises the hammer, slides the mast away from the pile, moves the pile driver to the next pile site and lowers the hammer so the next pile can be loaded and lifted. “During this repositioning time, operators still need to monitor the pile driver’s functionality, but they can also help get the next pile ready to be lifted. This can help minimize the number of people needed to support pile driving operations,” Howell explained.
Amy Olsen is product marketing lead at Vermeer. Contact your local Vermeer dealer for more information on machine specifications.
Comments are closed here.