Roofs of Hazard: PV connector risks continue to plague solar portfolios according to HelioVolta findings
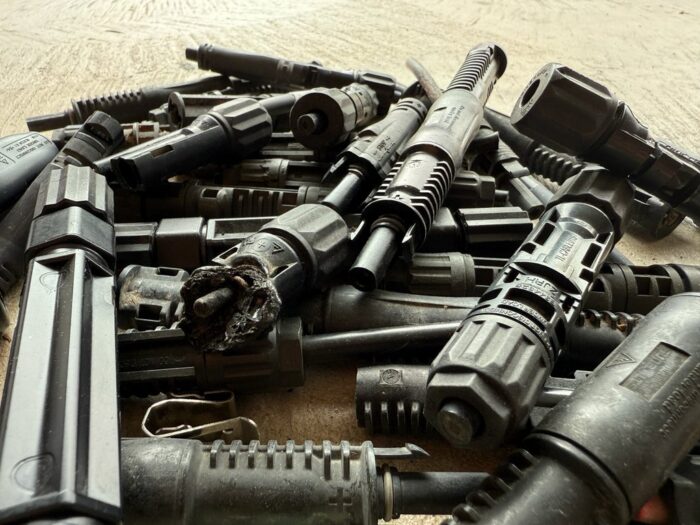
Who is ready for some more bad news this week? Field inspection and analytics firm HelioVolta reports the solar industry is still struggling to address the big – costly! – risks associated with PV connectors in the field.
Despite years of attention, PV connectors remain one of the most common sources of system failure across commercial and utility-scale solar. In its new report, PV Connectors: The State of the Field, HelioVolta shares insights from independent inspections at hundreds of projects totaling more than 5 GW of capacity.
Among the findings:
- 83% of projects inspected had at least one connector-related issue
- 45% of sites had major connector problems that required urgent maintenance
- 4.3% of systems faced critical connector failures that required partial or full shutdown
- Most of these issues stem from improper installation
“It’s absurd that one of the cheapest components in a PV system is responsible for the industry’s most notorious failures,” said David Penalva, CEO of HelioVolta. “We’re talking about a dollar’s worth of plastic and metal putting multimillion-dollar assets—and people—at risk. It’s unacceptable.”
HelioVolta’s white paper presents anonymized case studies of connector-related failures and outlines risk mitigation strategies for asset owners, EPCs, and O&M providers. It also includes financial modeling that shows just how expensive these failures can be.
Want one example? Connectors cause 58% loss of annual revenues
- Project: 1 MW Retail Rooftop Project
- Problem: A fire caused by an overheated arcing connector severely damaged PV system equipment and the roof of a retail store.
- Cause: The root cause was systemic bad crimps during installation on all homeruns
- Impact: Store closes for one day. System de-energized for inspection and remediation. And another 1-month PORTFIO-WIDE de-energization to complete inspections and rework of that EPC’s nine other sites (a 100 MW portfolio).
- Total cost: $558,450, which equates to 58% of annual revenues lost. You should download the report to see the full cost breakdown.
“Proper connector installation is clearly important, but assessing these components at every preventive maintenance visit is just as vital,” commented Jesse Waters, CEO of Servist Energy, an O&M provider. “Since connector problems become riskier as systems operate, finding and fixing issues before disaster strikes is the best way to avoid high-cost remediation campaigns.”
Quantifying PV connector risks in design
The HelioVolta report does a good job of outlining 15 potential system configurations, and quantifying the connector-based risk for those configurations, connector types, and installation methods during the design phase.
“The number and type of connectors in a PV system can increase the risk of safety events by nearly 20x,” the authors note.
The path to the least risky starting score? A UL 3741 compliant system with no MLPE and factory machine-made module connectors. Anything field-made is going to “jumper” up the score, if you will.
MLPE will inherently increase the risks by having more points of connection – a fact we’ve been pointing out for a decade now. Plus, a 1:1 MLPE to module ratio often requires jumpers to prevent cross-mating.
But HelioVolta also highlights the compounding impact of supply issues. It’s not uncommon for MLPE and solar modules, both with factory-made connectors, to arrive on site with connectors that are not compatible. As HelioVolta notes, this leaves two choices that add significantly more risk based on their findings in the field:
- Cut off and replace the factory-made connectors with matching field-made connectors, potentially voiding the PV module and/or MLPE warranty.
- Use jumpers, which are cables with connectors at both ends, to bridge incompatible connectors and avoid inter-mating.
HelioVolta suggests implementing procurement specifications to ensure cross-brand compatibility. Recognizing that product availability is often limited, HelioVolta delineates enhanced quality control and O&M procedures for projects with higher-risk system configurations.
Intermating PV connectors is not code compliant per NEC 2023
Merely following NEC 2023 can solve some of this. HelioVolta finds 40% of all major and critical issues observed relate to intermating PV connectors. Intermated PV connectors are not compliant with NEC 2023. Per Penalva:
“Intermated connectors are not compliant unless their positive and negative parts have been tested together and UL certified for intermateability. Typically, brands only do this testing and UL certification with their own models; for example, MC4 and MC4 Evo2 connectors from Staubli were tested and UL certified together, and they are approved to intermate — it’s two parts from different models, but they still have the same manufacturer.”
So, just meeting NEC 2023 with a UL certified 6703 connector would reduce the risks noted in this report by 40%? Penalva confirms: “We are confident that 40% of the issues reported could be avoided by complying with NEC 2023”
Any good PV connector news?
My two cents per Watt? Codes and standards really need to step up and address this — and help might be on the way. The HelioVolta report concludes by highlighting innovations in the connector space, including the rise of crimpless connectors, efforts to standardize connector terminology led by Sandia National Laboratories, and an initiative to develop a universal connector standard from National Renewable Energy Laboratory (NREL).
Final word: Preventable.
The standout line in the report: “Most connector issues were readily avoidable: inter-mating (i.e., crossmating, mismatch), exposure to the elements, and under or over-torquing make up over 60% of all connector issues.”
HelioVolta’s report notes that preventing connector failure also requires supporting EPC and O&M field teams with better tools, training, and documentation methods. Trainings must cover proper installation techniques, measuring thermal anomalies (“hot connectors”), and visual inspection guidelines.
Finally, conducting third-party inspections of connectors during construction and throughout the project lifecycle helps asset owners ensure the safety of their fleet over time.
To download the white paper, visit www.heliovolta.com/connector-white-paper.
Comments are closed here.