How to select conduit for your next commercial solar installation
A site survey will determine conduit paths, and designers determine which cables require protection, depending on the type of circuit and the hazards they may face. Conduit is most commonly used on circuits that leave PV arrays, protecting string conductors in outdoor source circuits and also at PV output circuits from combiner boxes to inverters. They may also be used indoors to distribution boards. Building and fire codes have wiring requirements that may specify cable and conduit ratings. Different types of circuits may only require cable protection at certain points, and conduit performance may differ in each location.
Sales and marketing director Tim Creedon from Flexicon Ltd, a supplier of more than 50 types of electrical conduit, says where the cables are run and how they are secured is important. Whether cables are run on a roof or under a building, and whether there is shelter available, determines the type of conduit needed.
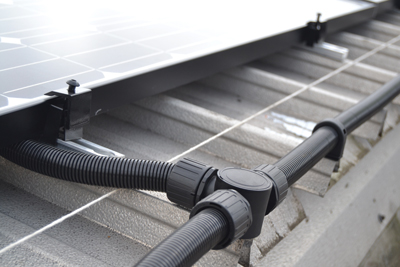
The flexible conduit is supported and fixed into position using Flexicon’s FCL conduit clips.
The minimum and maximum operating temperatures determine the amount of temperature protection the conduit needs to provide, whether metallic systems can be used and whether techniques need to be used to absorb thermal expansion and contraction. Whether the conduit will be subjected to vibration or movement determines whether flexible or rigid conduit is needed. The length of the conduit also matters; long conduit runs with large amounts of expansion may benefit from using threaded IMC instead of compression fittings that may vibrate loose over time.
Site-specific UV conditions determine the amount of sunlight resistance the conduit should provide. Whether it is located outdoors or indoors and the types of weather conditions the conduit will be exposed to will help determine the minimum ingress protection (IP) rating the conduit needs to have. If it is used outdoors or underground and will potentially have moisture inside that would condense under the right conditions, the NEC states that the conduit must be rated for wet locations. PVC will be required in situations where the operating environment, salt spray, weather or location underground will require additional oil or corrosion resistance.
The type of maintenance that takes place in the installation area is also important, according to Creedon. Hazards may come from nearby grazing animals, industrial trimmers or routine wash-down processes. He believes designers should assess not only the types of hazards the conduits will face, but also those that are likely throughout the lifetime of installation.
Other environments may require the extra physical and mechanical protection of galvanized metallic conduit: hazardous areas with risk of explosion, fire, EMC screening, vandalism, theft or electric shock. Stronger protection may be needed in high areas such as roofs or parking garages or for connections under a building.
Common practices
Brown says that in practice, the best conduit should be selected for the solar application that is code compliant and long-lasting, but that is not always the case.
“Most contractors first look at price; second, whether the job requires the conduit to be an agency listed product, and then the lifetime the customer requires,” he says. “They will choose between standard UL ratings and higher performance rated products that offer longer life expectancies and are more expensive. A contractor may only need five-year performance and can get by with less expensive products, or some contractors can use a non-UL product and prefer the extra performance properties — it depends on the installation.
“Then, they choose conduit products by the environment, the heat, the weight, flexibility requirements, sunlight exposure and life expectancy of the product,” Brown continues. “If there is a concern on weight of the product, they choose non-metallic over metallic. If there is a possibility of vibration and flexing, where flexible pieces are needed for connections that turn, liquid-tight conduit is chosen to protect those wires. In a region where there is seismic activity, flexible conduits are used in conjunction with a loop for movement and expansion. Some cables, such as those that are buried underground, don’t need the extra protection that liquid-tight conduit provides, and contractors can get away with using a coated PVC pipe.”
Conduit life expectancies depend on the installation environment, the exposure and the climate. If the conduit is located where it is routinely stepped on, it can become brittle and crack. According to Brown, a standard PVC tube in Florida will hold up for 8-10 years before cracking. AFC’s Extreme Temperature Liquid-Tight Flexible Metal Conduit, which is made with materials similar to those used in automotive windshields, will last more than 20 years in the sun.
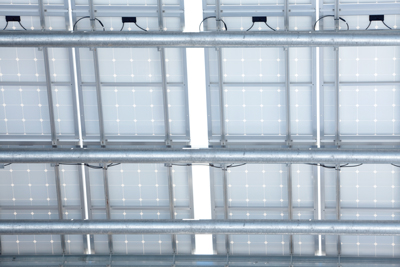
Tubing or conduit? Depends on if it is structural or UL listed cable protection.
Conduit options over the long haul
Over the long term, corrosion resistance is important in metal raceways, especially those that are in water, salt/marine and underground environments. In polymer-based conduit, UV resistance is important to prevent degradation and cracking.
The first UL standard for liquid-tight flexible steel conduit (UL360) arrived in 1976, and the first for liquid-tight non-metallic conduit (UL1660) came in 1993. Brown says compared to what was available for a solar installation in 1976, today’s conduit has evolved and looks much different.
“Now, much higher quality steel is used in the conduit with metallic cores,” he says. “The galvanizing process is better and more environmentally friendly. Cores are made without the heavy metals that weren’t regulated at the time. There are more types of conduit now, and the performance of thermoplastic materials has improved over the years. The chemical makeup of the PVC has changed.
“Lead stabilizers, which determined how the material was bonded together during processing, were removed in 2002. Now, there are better stabilizers; some are zinc and others are bio-based, making them more environmentally friendly. The plasticizers that make the thermoplastics flexible and other physical properties of the thermoplastics have evolved and continue to do so,” he continues. “Every few years, there is a new chemical used to comply with a different government or EPA guideline. Conduit has evolved to perform better, with higher quality, able to handle more tension and provide better flexibility.”
Comments are closed here.