Take the heat: How solar can benefit from thermally conductive silicones
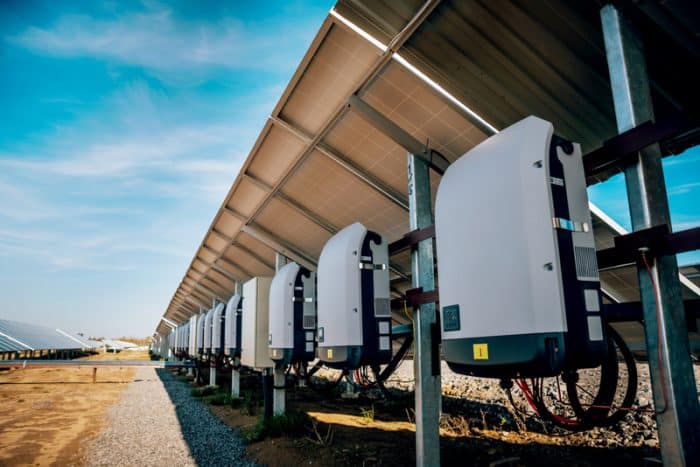
Although the renewable energy sector continues to experience challenges ranging from grid instability and labor shortages to permitting delays, there is good news on the materials front. Silicones can meet important requirements for two critical technologies in solar + storage applications — PV inverters and battery energy storage systems (BESS).
Achieving higher efficiency through better control and management of electricity flow is a key goal for PV inverters, while BESS offer the potential to increase grid flexibility. For both, performance optimization depends, in part, on thermal management. Both must withstand the high levels of heat that are generated by power electronics, as well as fire propagation, a leading safety concern.
Of course, there are other considerations, including resistance to harsh outdoor conditions. Manufacturers need materials that enable cost-effective and energy-efficient production at high volumes. Thermally conductive silicones can address all these requirements and more.
Why choose silicones?
Silicone, a polymer containing silicon and oxygen, is known for chemical inertness, resistance to water and oxidation, and stability at high and low temperatures. It is supplied in many formats: adhesives, encapsulants, interface materials, gels, conformal coatings, greases and sealants. Within the silicone family are thermally conductive versions, which are formulated with special additives to dissipate heat. In the case of solar, that means moving heat away from sensitive electronics to prevent damage, interruptions or failure.
Thermally conductive silicone materials typically fill gaps between a heat source and a heat sink to amplify heat dissipation speed and effectiveness. They replace air that would otherwise fill these gaps with a much more powerful thermal management solution.
Designers can choose thermally conductive silicones that withstand high heat and meet specific flame ratings including UL94 V-0. Because they resist dust, moisture and humidity, thermally conductive silicones also are well suited to outdoor use. Their flexibility and stress-relieving properties make them a good choice for applications that experience vibration or slight movements.
Thermally conductive silicones can improve manufacturing efficiency and sustainability. For example, curing, a chemical reaction that is required to achieve silicone’s final properties, can take place at room temperature or by extracting moisture from the air, which avoids the need for adding heat from ovens.
One common alternative to silicone encapsulants is polyurethane (PU), an organic polymer offering cost benefits. However, PU encapsulants used in confined spaces are subject to higher stress under thermal cycling than silicone encapsulants, which can lead to cracking and failure. Heat aging tests reveal that, compared to PU materials, silicone encapsulants deliver higher reliability, which contributes to a lower failure rate and longer service life.
Protecting PV inverters
Currently, silicone thermal encapsulants and other silicone materials are widely used in PV inverters. They are helping manufacturers gain a competitive advantage based on safety, robustness and long service life equal to the lifespan of the solar energy system.
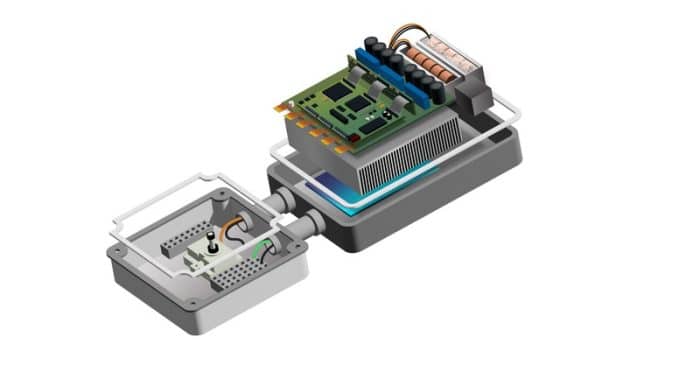
Thermally conductive silicones can deliver higher temperature stability compared to organic counterparts, permitting higher voltages. Thermally conductive silicones also contribute to reliability and long-term performance. Inverter designs relying on organic materials typically fail before designs that use silicones.
Silicone thermal encapsulants fill gaps between electronic components and the enclosure in the inverter’s inductance module. These materials have a low viscosity, or low resistance to flow, for easy filling and dispensing with equipment such as static mixers. Some inverter modules have complex geometries that impede flow. In these scenarios, specialized silicone-based materials can provide a high-flow solution.
In addition to encapsulants, designers can use silicone thermal interface materials (TIMs), and thermal gels to help protect inverter components. Silicone TIMs are also designed to fill small air gaps that are poor conductors of heat. However, compared to silicone thermal encapsulants, silicone TIMs provide broader and higher levels of thermal conductivity. In PV inverters, TIMs are applied or installed between the insulated gate bipolar transistors (IGBTs) and printed circuit board (PCB). In a solar string, they support the use of 1500V DC/AC inverters that handle up to 300 kW of power.
Silicone TIMs can take the form of dispensable pads that are screen- or stencil printed for higher production throughputs and lower total cost of ownership. For thinner bond lines, however, silicone thermal greases may be required. Because these greases are non-curable, they remain in a paste-like state that helps optimize surface wetting, a leading factor in lower thermal interface resistance. However, compared to curable materials, they are less stable under harsh conditions.
Silicone thermal greases are easy to rework and, depending on the formulation, have viscosities that range from non-flowable to semi-flowable. Application methods include squeegees, needle dispensing and screen printing.
Silicone thermal gels are also used to protect the IGBTs in PV inverters. Although thermal gels have limited adhesion, they are flowable and can be applied as printable pads or dispensed like a liquid gap filler. Compared to fabricated thermal pads, thermal gels are significantly less expensive and can support thinner bond lines ranging from 150 µm to 5 mm.
Although silicone thermal gels do not support primer-less adhesion, they have low shear viscosity for high throughput. They can be applied with high precision for greater yields. These soft, compressible and stress-relieving gels are reworkable and suitable for part designs with small shapes and intricate geometries. Thermal gels cure at room temperature but, like thermal encapsulants, can be cured more rapidly by using ovens.
Better BESS protection
Silicone materials are being adopted in BESS applications as well. Designers and fabricators are either selecting thermally conductive silicones at a project’s inception or learning about them through trial and error. Many are ultimately transitioning to silicones as a solution to the limitations of less-reliable materials.
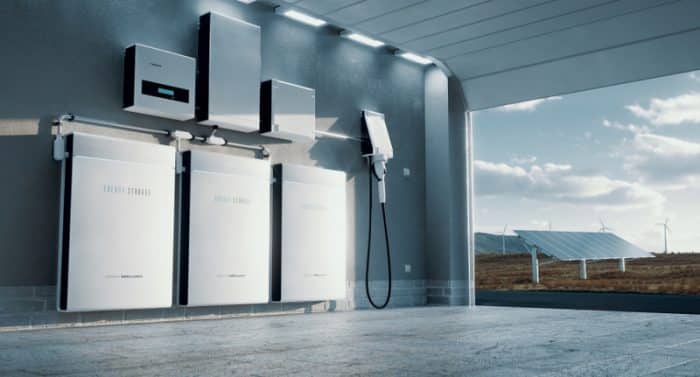
Typically, these BESS systems use lithium-ion batteries because of their cost-effectiveness. However, Li-ion batteries are susceptible to thermal runaway, where a battery cell enters an uncontrollable, self-heating state.
In battery pack assemblies, thermally conductive silicones are used in modules with prismatic, pouch or cylindrical cells. Along with thermal stability, these advanced silicone materials can resist the spread of fire.
Prismatic or pouch cells | In modules with prismatic or pouch cells, thermally conductive silicones provide reliable adhesion for component staking. They relieve stresses caused by varying rates of thermal expansion among metals, ceramics, plastics, and glass. These adhesives enable efficient, high-volume manufacturing with primer-less adhesion, moisture curing, and compatibility with metered mixers and automated dispensers.
Thermally conductive gap fillers are soft, compressible, two-part silicone materials that combine thermal management with mechanical stress relief and vibration dampening. They are suitable for gap tolerances ranging from 150 µm to 5 mm.
During product assembly, silicone gap fillers spread readily across substrates and remain in place, even in the vertical position. They provide excellent interfacial contact for reliable cross-joint strength and durable thermal dissipation.
Cylindrical cells | In battery pack modules with cylindrical cells, Li-ion batteries are arranged in an array and spaced closely together. Thermally conductive silicone adhesives attach individual cells to a substrate. To fill the spaces between cells, thermally conductive silicone encapsulants or foams may be used for fire protection. Both provide important advantages.
Encapsulants supply dependable strength and fire protection during normal operations and in the event of a cell failure. With their low moisture uptake, they also provide electrical isolation. Furthermore, silicone encapsulants deliver mechanical stress relief and vibration damping. Low viscosity allows them to fill molds with complex geometries. For efficient production, they can be used in automated mixing and dispensing equipment.
Silicone foams offer a lightweight, fire-resistant alternative to encapsulants but have much lower thermal conductivity. In fact, they provide thermal insulation to prevent heat transfer to adjacent cells during an event. Both products have similar viscosities and curing times, but silicone foams are the most compressible and have the lowest density of all products described in this article.
Supporting a safer, sustainable future
With demand for energy-efficient, heat-resistant solar + storage applications on the rise, so too is the need for versatile and practical materials that help promote thermal management. While the rate of thermal runaway incidents in lithium-ion batteries is fairly low, the risk of combustion remains an industry concern.
Thermally conductive silicones can withstand and dissipate the high amounts of heat generated by these storage applications and can help reduce the spread of fire. These versatile materials not only enhance the thermal management and durability of solar components, they also contribute to the overall efficiency and sustainability of solar energy systems. As the world increasingly turns to clean energy solutions, thermally conductive silicones helps meet these demands and promotes a safer and more sustainable future.
Cody A. Schoener, PhD, is marketing manager for Dow Performance Silicones at The Dow Chemical Company. Prior to this role, he spent 8 years as a technical and developmental scientist for The Dow Chemical Company servicing polyurethane and cellulosic chemistries. He earned his PhD in chemical engineering from University of Texas at Austin in 2012.
Comments are closed here.