The Pitch | What Makes a Quality Solar Module?
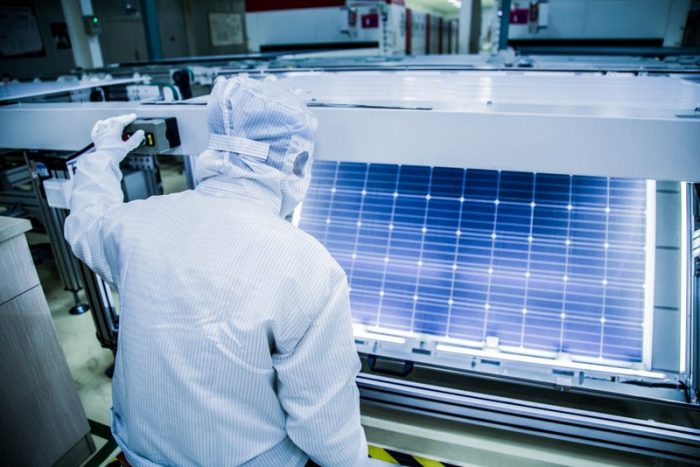
Selecting an underperforming solar module can sink the performance and economic value of a solar project. Today on The Pitch, we get a crash course in solar module quality testing from Tristan Erion-Lorico, VP of sales and marketing with PV Evolution Labs and CJ Fu, director of product and solutions with LONGi.
We discuss: PV Product Quality Testing, 2022 Module Scorecard takeaways , what makes a Top Performer, How LONGi adds quality controls to its processes and what else goes into module procurement due diligence. Below is a part of the transcript. Be sure to watch the whole 12 min episode.
Crowell: PVEL produces an annual Module Scorecard that grades various modules based on their performance, and the 2022 scorecard was just revealed last week. What are the biggest takeaways this year?
Erion-Lorico: We’ve got some really good news stories for the industry. Test results are getting better for a few tests. We see the best results in PVEL’s history in thermal cycling after doing that test for more than a decade. Results have kept edging up. Potential induced degradation, for the last like three or four years we’ve reported this is the worst result ever, this is the worst result, ever and we keep saying that. We’ve seen that turn around and PID is improving from last year, so we’re hoping that that’s on an upward trajectory as well.
Despite those strong results, it’s not all positive news. We do highlight some of the modules that didn’t do so well in testing, and that’s letting the industry know what to look out for in terms of high degradation or diode failures or other testing failures.
Crowell: CJ, essentially every year that LONGi has manufactured a module it has been graded a PVEL Top Performer. In terms of production process and quality control assessments, what is LONGi doing behind the scenes to achieve this consistent result?
Fu: We have implemented a lifecycle quality system that covers product design, new material qualification, manufacturing process, third party testing and after-sale service. We invest heavily in R&D to make sure our products and technology is best in class. In the last 10 years, LONGi has invested more than $1.5 billion R&D. We establish the testing capability in-house and conduct extensive testing to verify the quality of our products. Collaboration with third-party labs such as PVEL is a key component of our lifecycle quality system.
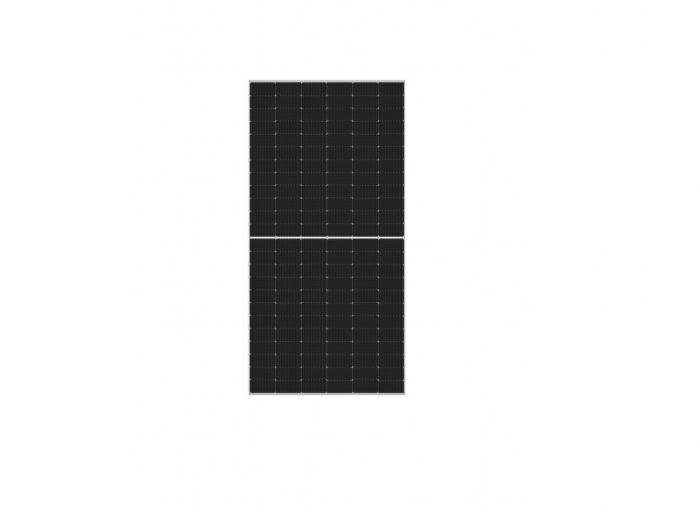
Crowell: The LONGi Hi-MO 4, 72-cell bifacial model specifically the LR4-72HBD, was one of only six models out of 121 to be a Top Performer in every single category PVEL measured to give a sense of how hard this is to do. What are some of the variables within that bill of materials (BOM) for instance that if you changed or altered something, how it might affect the final performance of that product?
Fu: The Hi-MO 4 72-cell bifacial double-glass module is a great example of how our lifecycle quality system works. We put many thoughts into product design, material selection and production process to ensure the reliability of our final product. So, one example I’d like to mention is that the module BOM decision between double glass structure and the transparent back sheet. They conducted many rounds of reliability testing for different kinds of transparent back sheets, and test results showed some concerning failures such as yellowing, cracking or delamination. On the other hand, the double glass module showed consistently better performance in the stress tests such as the damp heat and UV test. This data helped us decide to go with the double glass structure, and the decision has been also verified by the excellent results from the PVEL reports.
Crowell: Beyond just looking at the scorecard, as a module buyer, how do I ensure the modules I’m ordering will be top quality?
Erion-Lorico: Buyers with higher risk will want to do factory audits to make sure that the equipment in the factory is calibrated. They’ll want to do pre-shipment inspections and have a third party in the factory. That’s a service that PVEL doesn’t offer, but it’s a best practice that we recommend.
Crowell: If I’m just doing an under-a-MW rooftop project though, I would assume that having someone in the factory is too much due diligence or out of my price range.
Erion-Lorico: There are some manufacturers where their test results are based on one bill of material, and you don’t know how the rest of them perform. If multiple bills of material are submitted, we average those to determine if it’s a top performer. So, if they submit a few garbage BOMs that pull them down, they won’t reach that status.
Fu: That’s a good point. One thing LONGi did different, like Tristan mentioned, is we didn’t just pick the cherries off this whole tree. We sent a number of production BOMs to show the customer that the production will be carried through this range of BOM materials. That they are all going to be going through the third-party verification.
Erion-Lorico: They’re specifying, you know, five BOMS with different encapsulants and different glass and what have you, so that if there’s an issue with an encapsulant supplier, they can pivot to provide modules with another one, and those have been third-party tested. Where manufacturers that are only submitting one or two BOMs for PQP, if there’s an issue with their cell supplier or something, now they’re offering up untested products.
Comments are closed here.