A Brief Primer on Rising Solar Module Costs and How to Overcome Them
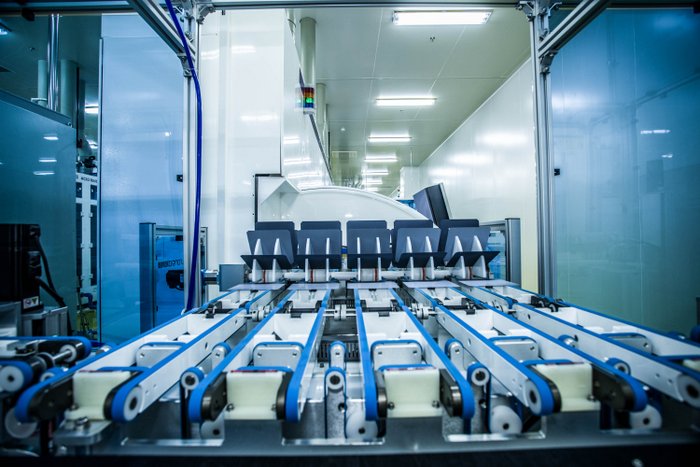
Since the solar boom began more than a decade ago, residential solar installers have been able to count on one thing: the price of solar modules would keep going down, year after year. In fact, since the late 2000s, module prices have dropped some 90%. But those days of ever-decreasing module costs have come to a stop: supply has tightened and prices are creeping upward.
To help explain why this is happening, let’s look at what’s been going on upstream in the solar module manufacturing process, all the way up to the processed raw material at the foundation of every crystalline panel—polysilicon, or poly.
Most of the world’s poly supply today comes from China, where over the past decade many new giant factories that process the raw silicon into silicon rods and ingots have been built to meet the demands of the growing solar industry. These rods and ingots are then sliced into wafers, the base material of the solar cell, and the cells are strung, integrated and laminated into those amazing modules harvesting energy from the sun on your customers’ rooftops. The most expensive part of a solar module is, you guessed it, the polysilicon wafer that is the foundation of the solar cell.
In recent years, rapidly expanding polysilicon capacity has led to a continual downward trend in PV module pricing. However, over the past year this trend has reversed course with booming global demand for PV modules and now limited polysilicon capacity. The price of poly is now the highest it has been in a decade. There just isn’t enough production capacity to keep up—and building new poly factories is not a quick proposition—so the laws of supply and demand have kicked in. Add in ridiculous increases in shipping and logistics costs, and voila!, higher module prices for the residential installer in Everytown USA.
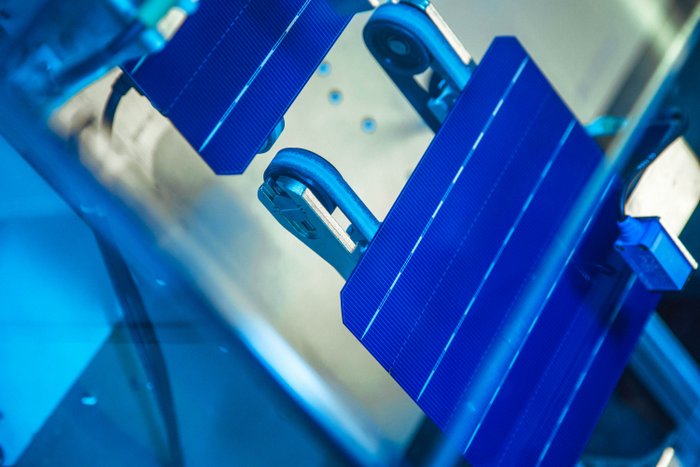
This should not come as a shock. Many essential materials and finished goods are in short supply, from semiconductors to steel to lumber. One could draw a parallel between the residential solar and home construction/renovation contracting industries here—like with poly, lumber supplies are tight and the prices have skyrocketed.
Being smarter about how you run your business and adding the value proposition in your customer interactions can help avoid a business slowdown and offset a few cents per watt in higher module costs. After all, it’s still a strong market out there.
What other costs can be reduced? Are there other efficiencies you can dial in around your customer acquisition costs, procurement and inventory control, and software utilization? Are you using value-based selling techniques with your customers in such a way that they still understand the underlying economics of going solar? Are you choosing the highest-quality modules like LONGi and other components so that your customers get the best performing systems for the money?
Fear not: market analysts say this module price inflation is temporary and should only last a few quarters, once the polysilicon and module supply-demand imbalance stabilizes. And the lessons learned and operational improvements made during this bumpy time can pay big dividends in the long term, regardless of materials costs.
This post was contributed and sponsored by LONGi Solar.
Comments are closed here.